ПРОИЗВОДСТВО МЕДИ
§ 28. Медные руды
В самородном состоянии медь встречается редко. Наиболее распространенными рудами меди являются руды, содержащие сульфиды CuS и Cu₂S; например, медный колчедан, содержащий халькопирит CuS x FeS, медный блеск, содержащий халькозин Cu₂S. Из сульфидных руд получают около 80% меди. Менее распространены руды, содержащие кислородные соединения Cu₂O и редко встречаются руды с углекислыми соединениями CuCO₃ x Cu(OH)₂. Содержание меди в рудах мало и составляет 1 - 3%. Кроме меди, руды содержат небольшое количество цинка, свинца, никеля и других металлов и много пирита FeS₂.
Пустая порода руд состоит из песчаника, известняка, глины или их смесей.
Медь из руд чаще всего извлекается пирометаллургическим способом и реже - гидрометаллургическим, применяемым при переработке измельченных бедных руд методом выщелачивания.
§ 29. Пирометаллургический способ получения меди
Получение меди пирометаллургическим способом состоит из обогащения, обжига, плавки на штейн, продувки в конверторе, рафинирования.
Обогащение медных руд производится методом флотации. Руда измельчается дроблением и размолом до зерен размером 0,05 - 0,5 мм. При отделении частиц, содержащих медь, от частиц пустой породы используется различная смачиваемость их водой. Частицы, содержащие медь, плохо смачиваются водой, а частицы пустой породы, наоборот, хорошо смачиваются. Через смесь, состоящую из измельченной руды, реагентов, воды и пенообразующих веществ, в флотационных машинах продувают воздух. При этом образуются пузырьки, к которым прилипают несмачиваемые водой частицы, богатые медью. Последние вместе с пузырьками всплывают на поверхность воды в виде пены. Частицы пустой породы, смачиваемые водой, осаждаются на дно ванны. Таким образом, получается медный концентрат, содержащий 10 - 35% меди.
Медные руды, а также концентраты, содержащие большие количества серы, подвергаются обжигу. С целью уменьшения содержания серы обжиг производится в вертикальных многоподовых печах, а также в печах с кипящим слоем. Более совершенным является обжиг в кипящем слое.
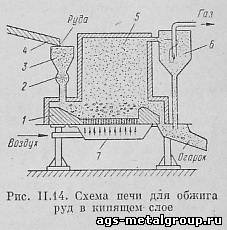
На рис. 11.14 приведена схема соответствующей печи. Шихтовые материалы - концентрат, известняк и кварц транспортером 4 подводятся к бункеру 3 и из него через дозатор 2 поступают на под 1 и далее под воздействием струй воздуха из воздушной коробки 7 непрерывно подбрасываются вверх и в горячей камере 5 поддерживаются во взвешенном, псевдосжиженном состоянии. Слой частиц как бы кипит и каждой частице обеспечивается наилучший контакт с газами. Из камеры газы затем поступают в пылеуловитель 6. В камере за счет тепла химических реакций поддерживается температура в 600 - 700' С. Железо и сера окисляются. В результате обжига получается продукт - огарок, используемый для получения меди. Отходящие газы улавливаются, очищаются от пыли и используются в производстве серной кислоты.
После обжига руда и медный концентрат подвергаются плавке на штейн, представляющий собой сплав, содержащий в основном сульфиды меди и железа (Cu₂S и FeS). Штейн содержит 20 - 50% меди, 20 - 40% железа, 22 - 25% серы, около 8% кислорода и примеси никеля, цинка, свинца, золота и серебра. Чаще всего плавка производится в пламенных отражательных печах (рис. 11.15). Длина печей до 40 м, ширина 6 - 9 м. В печь загружается свыше 100 т руды. Температура в печи в зоне плавления достигает 1450' С. Печь футерована динасовым кирпичом. Из бункера 1, расположенного на вагонетке, через воронки 2 в печь загружаются руда 4 и флюс на под 5. Топливо сжигается в топке 6; газы из печи удаляются через дымоход 7. Получающийся в результате плавки штейн выпускается через летку 8. В печи поддерживается слабоокислительная атмосфера.
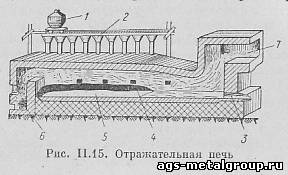
Получение черновой меди осуществляется продувкой штейнов в конверторах. Чаще всего для этого используют крупные горизонтальные конверторы емкостью до 10 - 120 т и более (рис. II.16). Конвертор состоит из кожуха 6, днищ 1, футерован магнезитовым кирпичом. Заливка конвертора жидким штейном, а также выпуск готового металла и шлака производятся через горловину 3. Флюсы (песок) вводятся приспособлением 2. Дутье подается через фурмы 4 под давлением в 0,75 - 1,25 атм (75 - 125 кН/м²) от воздухораспределительной трубы 5. Конвертор на катках 8, установленных на постаменте 9, может с помощью привода 7 поворачиваться вокруг горизонтальной оси. Тепло в конверторе получается без подачи топлива за счет химических реакций. Температура в конверторе достигает 1200 - 1300 С. При этом происходит окисление сульфида железа за счет кислорода воздуха.
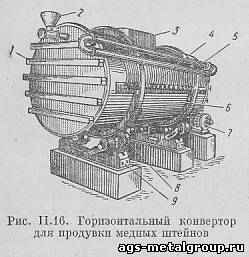
Полученная черновая медь, содержащая 0,5 - 1,5% примесей (золото, серебро, свинец, сурьма и др.), разливается на чушки или при наличии миксера в жидком виде поступает на рафинирование (очистку).
Огневое рафинирование производится в пламенных отражательных печах емкостью до 250 т, отапливаемых мазутом или пылевидным топливом. Рафинирование состоит в окислении примесей, имеющих большее сродство к кислороду, чем медь, кислородом воздуха, который по железной трубке подается непосредственно в металл под давлением в 1,5 - 2 ат (150 - 200 кН/м²). Получаемые окислы PbO, ZnO, Sb₂O₃ и др. шлакуются или улетучиваются. Золото и серебро остаются растворенными в меди. После скачивания шлака производится восстановление меди «дразнением». В металл вводят сырые, а затем сухие деревянные бревна и ими перемешивают жидкую медь. Газы, выделяющиеся из дерева, восстанавливают медь и способствуют удалению сернистого газа. Восстановление меди обугленной древесиной идет по реакции
Cu₂O + С = 2Cu + СО;
Cu₂O + СО = 2Cu + СО₂.
Полученную медь разливают на слитки или анодные пластины для электролиза. После огневого рафинирования медь содержит не более 0,3 - 0,5% примесей.
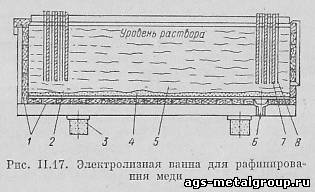
Электролитическое рафинирование обеспечивает получение меди более высокой чистоты и позволяет извлекать золото, серебро, селен, теллур и другие примеси. Процесс ведется в электролизных ваннах 1 (рис. II.17), изготовляемых из дерева с облицовкой внутри листами свинца 2, асфальтом, бакелитом или метлахскими плитками, устанавливаемых на изолирующих подставках 3. В ванну в качестве электролита 5 заливают 12 - 16-процентный водный раствор медного купороса в серной кислоте. На анодную шину 7 навешивают пластины из черновой или рафинированной огневым способом меди весом 200 - 250 кг, толщиной 40 - 50 мм, на катодную шину 8 - тонкие (толщиной 0,6 мм) листы электролитической меди. В процессе пропускания постоянного тока силой 10 000 - 15 000 а при напряжении 0,3 в анодные пластины растворяются и чистая медь отлагается на катодных пластинах. За 10 - 12 дней на катодной пластине отлагается около 100 кг меди. Расход электроэнергии составляет 250 - 300 квт/ч на 1 т (0,9 - 11 МДж/кг) меди. Ценные металлы (золото, серебро и др.) оседают на дно вместе со шламом А Шлам выпускается через отверстие 6, откуда они извлекаются при помощи специальной обработки. Катодную медь переплавляют и разливают на слитки. Медь выпускается пяти марок: М0, М1, М2, МЗ и М4. Медь марки М0 содержит 99,95% меди, а медь М4 - 99,0%.