Система блочных машин Генри Модсли пережила своего создателя. Мастер умер в 1831 году, а линия из станков проработала без переделки до начала 20 века! Факт удивительный, но не в нем главное. Важнее то, что именно в эти годы возникло машиностроение - новая отрасль промышленности.
Рабочие и инженеры машиностроительных заводов строили разнообразные новые машины уже не вручную, как раньше, а с помощью других машин - станков. Работы хватало! В 19 веке появились железные дороги и паровозы, первые пароходы и электромоторы. Были изобретены телефон, телеграф, построены первые автомобили, тракторы и самолеты. Для производства всей этой сложной техники, которая к тому же быстро изменялась, становилась все многообразнее и сложнее, нужны были станки высокой производительности. Многие машины стали выпускаться огромными сериями: десятками, а то и сотнями тысяч экземпляров. На машиностроительных заводах станочникам приходилось час за часом, день за днем изготавливать во все возрастающем количестве одинаковые детали.
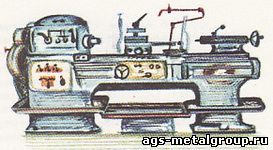
Советский станок ДИП-20. 30 - 40-е годы.
Суппорт Модсли сильно изменил характер работы станочников. Управлять движениями резца, режущего металл, с помощью суппорта и механической передачи гораздо легче, чем работать, держа токарный резец в руках. Но и тут требуются зоркий глаз, хорошая координация движений, повышенное внимание. А ведь человек не машина, он утомляется, устает. Особенно при однообразной работе, когда приходится повторять одни и те же движения. Устав, человек чаще ошибается. Тут недовернул или перекрутил рукоятку, там чуть перекосил заготовку при установке, и уже - брак, испорченная заготовка, потерянное время. Перед инженерами встал вопрос: если Модсли сумел освободить руки рабочего от рабочего инструмента, нельзя ли освободить людей и от ручного управления движением суппорта во время работы станка? Для этого надо было придумать такое устройство, которое как бы «запоминало» всю последовательность движений резца вовремя рабочего цикла - от начала до конца обработки заготовки на станке.
Сначала инженеры решили использовать механическую «память». Если обрабатываемые детали не очень сложны, то проста и программа их обработки. В таких случаях в станок стали устанавливать металлические диски-колесики с криволинейной, заранее рассчитанной поверхностью. По окружности диска скользит стальной палец-щуп. Попадается впадина - щуп опускается, начинается выступ - он поднимается выше. Остальное, как говорится, дело техники. С помощью механической передачи - набора зубчатых колес, валиков и рычагов - движение щупа передавалось рабочему инструменту. Так диски с выступами и впадинами - кулачки - стали исправно «командовать» движением резцов, сверл и других рабочих инструментов. Когда надо - подавали его вперед, когда надо - отводили назад. С помощью кулачков и механической передачи можно изменить скорость и направление движения суппорта.
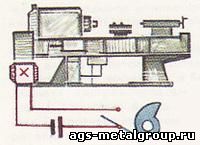
Кулачковый переключатель в электрической схеме управления станком.
Позже кулачки стали использовать для включения и выключения электромоторов станка или установленных на станке электромагнитов. Механическая память проста, надежна, неприхотлива. Кулачки можно заменить, тогда изменится и режим обработки заготовки. Долгие годы механические устройства автоматики и пришедшие им на смену электромеханические устройства вполне устраивали станкостроителей и станочников. Такие устройства позволили создать станки-полуавтоматы.
«Почему же сначала только ПОЛУ-, а не сразу АВТОМАТЫ?» - спросите вы. Дело в том, что автоматизировать движение рабочего инструмента, заставить его работать по заданной программе, только половина дела. Вторая половина - регулировка станка, установка заготовки и снятие готовой детали, замена инструмента, - как и прежде, требовала рабочих рук, ручного труда. Так или иначе станки-полуавтоматы стали на заводах привычными. И тогда - было это в самой середине 20 века - инженеры и ученые предприняли дерзкую попытку создать полностью автоматизированное производство. Такое, чтобы все операции по изготовлению деталей проходили без участия человека.
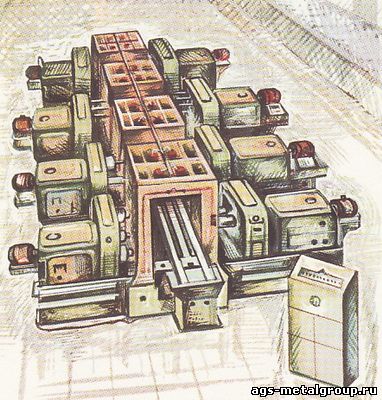
Автоматическая линия для обработки блоков цилиндров грузовых автомобилей ЗИС-150 в 1946 году.
В 1950 году в нашей стране построили первые линии из станков-автоматов. Изготавливали на них детали для автомобилей и тракторов. В каждой линии стояло по восемь металлорежущих станков. В то же время построили целый автоматизированный цех. В нем делали поршни для тракторных двигателей. Все операции - от выплавки металла до упаковки готовых поршней - были доверены автоматам.
Почему я назвал эту попытку советских инженеров дерзкой? Да потому, что для полной автоматизации металлообработки в те годы еще не было необходимой научной и технической базы. Да, детали к станкам подавались автоматически. В автоматическом режиме, согласованно, работали токарные, сверлильные, фрезерные станки. Но через каждые несколько часов линию приходилось останавливать для того, чтобы рабочие вручную заменили износившийся инструмент. Не удалось автоматизировать контроль точности деталей. Много было остановок из-за разрегулировки станков и поломок автоматов. Стоили линии дорого, а изготавливать на них можно было детали только одного типа. Малейшее изменение в чертежах приводило к длительной перестройке всего оборудования.
Из-за невозможности быстрого изменения программы работ такие автоматические линии назвали «жесткими». Механическая память невелика: много ли «запишешь» на одном кулачке? А большое количество кулачков на станке не разместить: слишком сложные механические передачи потребуются. Станкам-автоматам нужна «гибкость», способность быстро переходить к выпуску деталей других размеров, другого типа. Механическая память из-за своего малого объема не в состоянии обеспечить такой переход без длительной переналадки станка. Если разобраться, жесткие автоматические линии уступают в гибкости даже системе блочных машин Генри Модсли. По всем этим причинам первые автоматические линии и цехи стали достоянием истории, так и не совершив нового переворота в машиностроении. Инженеры поняли: для автоматизации станков нужны принципиально новые технические средства.
Такие средства станкостроители получили лишь тогда, когда были созданы надежные и небольшие по размерам, но могучие по своим возможностям электронные приборы.