ПРОКАТНОЕ ПРОИЗВОДСТВО
§ 7. Сущность процесса и элементы теории прокатки
Основными видами прокатки являются продольная, косая и поперечная (рис. IV.7). Продольная прокатка, при которой направление вытяжки совпадает с направлением вращения валков 1 и направлением движения заготовки 2, производится либо между гладкими валками - в этом случае продуктами прокатки являются листы и ленты, либо между валками с проточенными на их поверхности концентричными профильными канавками (ручьями), образующими при совмещении двух валков калибры. В последнем случае продуктами прокатки являются изделия с постоянными по длине профилями поперечного сечения: сортовой прокат, рельсы, балки и т. п.
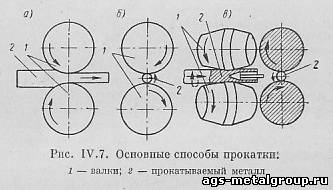
Продольная прокатка наиболее распространена в промышленности - этим способом производится около 90% всей продукции прокатных цехов. Поперечную и косую прокатку применяют для получения тел вращения. Отличительной особенностью этих видов прокатки является вращение валков в одном направлении, а находящейся между валками заготовки - в обратном. Поперечная прокатка используется в производстве цилиндрических шестерен с накатанным зубом, косая - в производстве бесшовных труб и проката периодического профиля.
Деформации металла при продольной прокатке. При продольной прокатке на гладких валках имеют место три вида деформации: обжатие, уширение и вытяжка (рис. IV.8 а,в). Эти деформации связаны между собой по закону постоянства объема металла при пластической деформации. На рис. IV.8,в показана исходная заготовка с размерами Н₀, В₀, L₀, и объемом V₀ и прокатанная полоса, имеющая размеры Нк, Вк, Lk, и объем Vk.
Из закона постоянства объема следует, что V₀ = Vk и, следовательно, H₀B₀L₀ = HkBkLk.
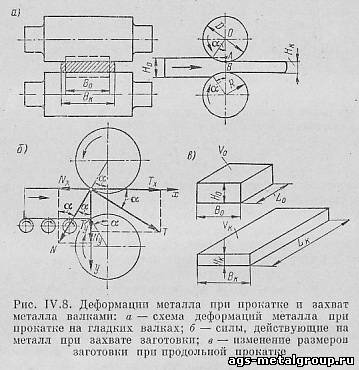
Обозначим относительные изменения соответствующих размеров заготовки при прокатке через так называемые коэффициенты деформации: H₀/Нк = γ - коэффициент обжатия; Вк/В₀ = β - коэффициент уширения; Lk/L₀ = λ - коэффициент вытяжки.
Тогда из равенства H₀B₀L₀ = HkBkLk следует, что: γ = H₀/Нк = BkLk/В₀L₀ = βλ, т. е. обжатие пропорционально вытяжке и уширению; β = Вк/В₀ = H₀L₀/HkLk = γ/λ, т. е. уширение пропорционально обжатию и обратно пропорционально вытяжке; λ = Lk/L₀ = Н₀В₀/НкВк = γ/β, т. е. вытяжка пропорциональна обжатию и обратно пропорциональна уширению.
Таким образом, для получения максимальной вытяжки следует производить прокатку с большими обжатиями и, по возможности, ограничивать уширение полосы. Последнее достигается прокаткой металла в калибрах. Коэффициент вытяжки λ показывает также, во сколько раз уменьшается сечение заготовки после каждого пропуска заготовки через валки прокатного стана: λ = F₀/Fk.
Значение λ принимается равным 1,1 - 2 в зависимости от материала, температуры, скорости и других условий прокатки.
Условие захвата. Для начала процесса прокатки необходимо, чтобы соблюдалось определенное соотношение между толщиной исходной заготовки, поступающей в валки, величиной зазора между валками и диаметром валков. Это соотношение устанавливается условием захвата.
На рис. IV.8, б видно, что при подходе прокатываемой болванки к валкам в точках соприкосновения горизонтальных ребер заготовки с образующими валков начинают действовать силы нормального давления валков на металл N, направленные по радиусам валков, перпендикулярно к их поверхности, и силы трения Т, направленные по касательным к поверхностям валков.
Угол α называют углом захвата.
Спроектируем силы N и Т на оси x и y. Вертикальные составляющие этих сил Ny и Ty называются кующими силами, обжимающими металл по высоте.
Горизонтальные составляющие Nx выталкивают заготовку из валков, а составляющие Tx - втягивают заготовку в зазор между валками. Для начала процесса прокатки необходимо, чтобы выполнялось условие: Tx > Nxx.
Из механики известно, что сила трения Т равна нормальной силе N, умноженной на коэффициент трения μ, причем отношение силы трения к нормальной силе равно тангенсу угла трения ψ, т. е. Т/N = tgψ = μ. Следовательно (рис. 8, б), Tx = T соs α = μN соs α и Nx = N sin α. Подставив полученные выражения в исходное неравенство, имеем μNcosα > Nsinα; поделив правую и левую части неравенства на Nсоsα, получаем μ > tg α или tg ψ > tg α и ψ > α.
Таким образом, для осуществления захвата металла валками необходимо, чтобы коэффициент трения между валками и металлом был больше тангенса угла захвата, или угол трения был больше угла захвата.
Очевидно, что при больших значениях угла захвата болванка не может быть втянута силами трения в зазор между валками, и валки будут лишь скользить по ребрам заготовки. Максимально допустимый угол захвата зависит от материала валков и прокатываемой болванки, шероховатости их поверхностей, наличия или отсутствия ручьев на валках, температуры и скорости прокатки. По производственным данным максимальный угол захвата при прокатке блюмов и сортового металла в калибрах составляет 30 - 32°, при горячей прокатке листа и полосы на гладких валках - 20 - 24°, при холодной прокатке тонких листов и лент на шлифованных валках со смазкой - 3 - 6°.
Улучшение условий захвата при прокатке обеспечивается:
1) увеличением коэффициента трения путем насечки или наплавки валков, что допускается на черновых обжимных операциях прокатки;
2) применением слитков пирамидальной (конусной) формы, причем слиток подается в валки меньшим основанием, и прокатка начинается при малых значениях угла захвата α₁ и заканчивается при больших значениях α₂;
3) увеличением диаметра валков при прокатке с большими обжатиями.
Из рис. IV.8, а следует: АВ = ОВ - ОА = R - ОА, но отрезок ОА = R cos α, поэтому АВ = H₀-Нк/2 = R - R cos α, откуда H₀-Нк = D (1 - cos α).
Проанализируем последнее выражение. Предположив обжатие постоянным, начнем мысленно увеличивать диаметр валков D, при этом второй сомножитель равенства (1 - cos α) должен уменьшаться, что, в свою очередь, означает увеличение соs α, т. е. уменьшение угла захвата α. Таким образом, чем больше диаметр валков при прокатке при данном обжатии, тем меньше угол захвата.
Из практики известно, что прокатку блюмсов, слябов и крупносортных заготовок (полупродуктов прокатки) производят на станах с валками большого диаметра (свыше 800 - 1200 мм), чтобы получить допустимые углы захвата при больших обжатиях.
Затрату работы на деформацию металла при прокатке вычисляют по формуле А = pVIn H₀/Нк кГ∙м (Дж), где р - удельное давление течения металла в- кГ/мм² (Мн/м²); V - обьем прокатываемой болванки в см³ (м³); Н₀ - высота болванки перед прокаткой; Нк - высота полосы после прокатки.