Сборка новых звеньев и разборка снятых с пути со всеми сопутствующими операциями выполняются на производственных базах путевых машинных станций.
Базы располагаются, как правило, вблизи крупных железнодорожных станций с тем, чтобы их производственный персонал в зимнее время осуществлял работы по снегоборьбе. Станция, к которой примыкает база, должна иметь путевое развитие, обеспечивающее маневровую работу с вагонами, в которых поступают материалы верхнего строения пути, и формирование всех хозяйственных поездов.
Базу строят в пункте, располагающем источниками энерго- и водоснабжения, вблизи жилого поселка, в котором имеются школа, больница, учреждения культурного обслуживания. При выборе места строительства базы учитываются также объемы путевых работ с тем, чтобы выполнять их без передислокации базы даже в перспективе.
Современная производственная база - это высокомеханизированное предприятие индустриального типа. На ней осуществляются:
- выгрузка, складирование и технологическое перемещение материалов верхнего строения пути;
- выгрузка, складирование в зимнее время и отгрузка в летнее время балластных материалов (если фронт работ расположен далеко от щебеночного завода или асбестового карьера);
- сборка новой путевой решетки;
- разборка снятой путевой решетки, сортировка, складирование и отгрузка старогодных материалов верхнего строения пути;
- ремонт старогодных шпал;
- погрузка и вывоз на перегон собранной путевой решетки;
- содержание и ремонт путевых машин, механизмов и транспортных средств.
Для обеспечения этих задач база имеет соответствующее путевое развитие, в том числе технологические пути, подъемно-транспортное оборудование в виде козловых и стреловых кранов, машины по сборке новой и разборке старой путевой решетки, шпалоремонтные мастерские, склады новых и старогодных материалов, пути для выгрузки и складирования балластных материалов, механические мастерские и депо путевых машин, гаражи, склады горюче-смазочных материалов, диспетчерскую, административные, санитарно-гигиенические, культурно-бытовые и тому подобные помещения (рис. 13.3).

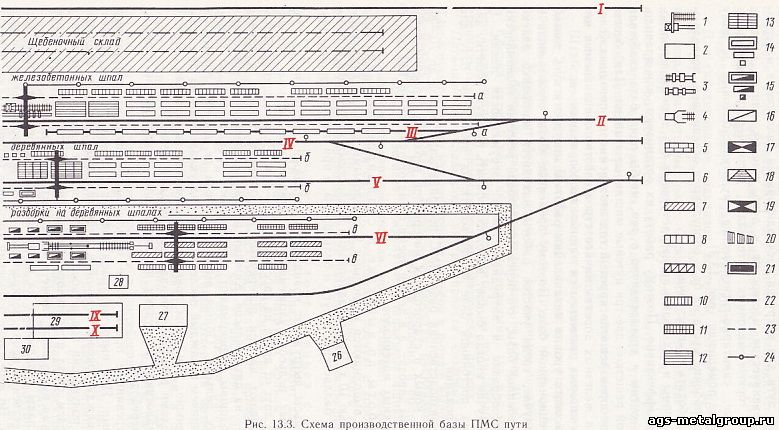
Все рабочие места на базе оборудуются освещением, позволяющим работать круглосуточно.
Машины и механизмы производственных баз должны использоваться эффективно. Поэтому работу их организуют, как правило, в две смены и круглогодично с тем, чтобы одна база снабжала путевой решеткой две-три путевые машинные станции. Для обеспечения сборки решетки круглый год независимо от погодных условий на железных дорогах начато строительство отапливаемых цехов, в которых размещаются машины по сборке звеньев.
Высокого уровня механизации работ можно достигнуть только на стационарной базе. Поэтому временные базы строят лишь в том случае, когда участок работы находится настолько далеко от постоянной базы, что перевозка готовой решетки экономически нецелесообразна и затруднена из-за загруженности линии. В этом случае иногда бывает выгодно собирать путевую решетку зимой на постоянной базе и перевозить на временную базу для складирования.
Производственная база ПМС перерабатывает в год до 70 - 80 тыс. т. новых и старогодных материалов верхнего строения пути. На базы завозят, а в летнее время с них отгружают до 160 тыс. т балластных материалов.
Работы по выгрузке и складированию материалов выполняются козловыми и стреловыми кранами грузоподъемностью 10 т. При складировании балластных материалов используются балластеры, струги и бульдозеры, а при отгрузке - экскаваторы.
Рельсы выгружают кранами на стеллажи, состоящие из старогодных рельсов, уложенных на старогодные шпалы, находящиеся друг от друга на расстоянии 1,5 - 2 м. Рельсы длиной 12,5 м укладывают на три поперечных старогодных рельса, а длиной 25 м - на пять рельсов. Каждый ряд новых рельсов, уложеннных на подошвы, перекрывают поперечными прокладками из старогодных рельсов. Общая высота штабеля не должна превышать 2 м, причем в каждый последующий ряд укладывают на два рельса меньше. Эти меры повышают устойчивость штабеля. Между штабелями рельсов устраивают разрывы не менее 2 м.
Аналогично оборудуют площадки для складирования стрелочных переводов.
Деревянные пропитанные шпалы выгружают из полувагонов кранами. При выгрузке тросы заводят с одной стороны полувагона между боковой стенкой и штабелем шпал, затем в открытые люки полувагона под штабель и поднимают наверх опять между штабелем шпал и противоположной боковой стенкой полувагона. Кранами выгружают также и железобетонные шпалы.
Шпалы укладывают на подкладки из старогодных шпал, преимущественно вдоль подкрановых путей, под консолью козлового крана. Во избежание появления трещин в бетоне и даже поломки железобетонных шпал между каждым их рядом на подрельсовые площадки шпал укладывают деревянные 'прокладки толщиной 40 - 50 мм. В штабель можно укладывать не более 12 рядов железобетонных шпал.
Накладки при выгрузке также штабелюются.
Для складирования подкладок, костылей, болтов и других деталей скрепления устраивают площадки с настилом из старогодных шпал или бетонных плит. Скрепления, поступающие в полувагонах или на платформах, выгружают кранами, оборудованными электромагнитными плитами. Для выгрузки скреплений, поступающих в полувагонах, выгодно устраивать углубленные в землю бетонные бункера.
Склады скреплений располагают так, чтобы избежать излишнее перемещение при сборке путевой решетки.
Штабеля звеньев собранной путевой решетки размещают не ближе 2,45 м от пути. Высота штабеля зависит от высоты крана, производящего штабелевку звеньев и погрузку их на подвижной состав. Между штабелями звеньев с деревянными шпалами для пожарной безопасности устраивают разрывы не менее 10 м.
Сборка путевой решетки как с деревянными, так и с железобетонными шпалами может производиться на пути-шаблоне или специальных звеносборочных полуавтоматических линиях.
Путь-шаблон укладывают внутри пролета козловых кранов. Такой путь собирают из старогодных рельсов и шпал и выправляют на балласте с подбивкой шпал. Для удобства раскладки материалов, механизмов, инструмента, прохода рабочих и выполнения работ по монтажу звеньев междупутья и шпальные ящики засыпают балластом до верхней постели шпал. Особенно удобен для этих целей асбестовый балласт, создающий ровную и хорошо уплотняемую поверхность. На междупутья можно уложить железобетонные плиты, забракованные для их использования по прямому назначению.
При сборке на пути-шаблоне звеньев с деревянными шпалами, как правило, шпалы развозят для каждого звена козловыми кранами. После выгрузки краном шпалы вручную раскладывают по эпюре. В разложенных шпалах сверлят костыльные отверстия электрическими дрелями с применением специальных шаблонов-кондукторов для установленной ширины колеи, типа рельсов и с соблюдением постоянного расстояния от шнурового конца шпал. Просверленные отверстия антисептируют.
Вслед за этим на шпалы укладывают подкладки и наживляют обшивочные костыли и основные наружные. Подкладки и костыли в объеме, необходимом на одну смену работы, развозят до начала смены козловыми кранами в контейнерах для каждого звена и размещают на междупутье.
Далее козловыми кранами раскладывают рельсы. Концы рельсов при этом выравнивают по наугольнику. Первым пришивают к шпале костылями рельс по шнуровой нити, противоположный рельс пришивают по шаблону. Костыли забивают электропневматическими костылезабивщиками ЭПК-2 или пневматическими молотками. Затем на звенья устанавливают противоугоны; на концы звеньев укладывают стыковые накладки и болты с шайбами и гайками. Концы рельсов и накладки зачищают и на них наносят слой графитовой смазки.
При отсутствии на базе козловых кранов для перемещения рельсов, шпал и скреплений возможно применение кранов ПКД, стреловых кранов, дрезин ДГК'.
Сборка звеньев с железобетонными шпалами - работа более трудоемкая. Масса железобетонной шпалы 250 кг, что значительно превышает массу деревянной шпалы. Промежуточные рельсовые скрепления для железобетонных шпал типа КБ имеют 11 различных деталей, при деревянных шпалах и костыльном прикреплении - только три-четыре. Поэтому при сборке рельсо-шпальной решетки с железобетонными шпалами предварительно укомплектовывают закладные и клеммные болты.
Закладной болт комплектуется изолирующей втулкой, шайбой и гайкой, а клеммный болт - клеммой, шайбой и гайкой.
Железобетонные шпалы развозят козловыми кранами, но меньшими партиями, чем партия деревянных шпал, с тем, чтобы сократить расстояния перемещений шпал при их раскладке по эпюре.
После раскладки шпалы выравнивают по шнуру, на них укладывают резиновые прокладки и металлические подкладки. Затем в отверстие подкладки вставляют закладной болт, а на подкладки укладывают подрельсовые прокладки.
Рельсы развозят и раскладывают козловыми кранами.
Гайки закладных и клеммных болтов завинчивают электрическими шуруповертами ШВ-1 с проверкой положения рельсовых нитей по шаблону.
Для облегчения работ по развозке и раскладке рельсовых скреплений в ОПМС-1 Октябрьской дороги сконструировали специальные самоходные тележки, которые передвигаются по объемлющему пути. Рельсы этого пути располагают за концами шпал пути-шаблона.
После развозки шпал козловым краном и раскладки их по эпюре первая тележка начинает продвигаться по фронту работ. На тележке погружены резиновые прокладки, подкладки и скомплектованные закладные болты. По мере продвижения тележки рабочие укладывают эти детали скрепления на шпалы.
Вторая тележка развозит подрельсовые прокладки и клеммные болты. Затем козловые краны раскладывают на подкладки рельсы, а монтеры пути устанавливают на места клеммные и закладные болты и завинчивают гайки этих болтов шуруповертами.
На работах заняты 32 чел. (в том числе 6 чел. на комплектации болтов). Производительность линии 750 м в смену.
Звеносборочную линию ППЗЛ-500 производительностью 500 м в смену обслуживают 14 чел., что в 3 раза меньше, чем при ручной сборке.
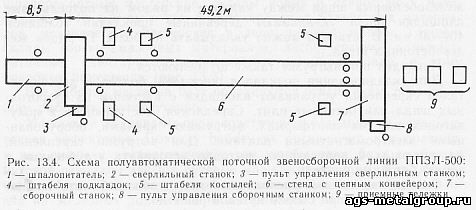
Порядок работы на линии следующий (рис. 13.4). Козловой кран подает шпалы на шпалопитатель, откуда они автоматически поступают на сверлильный станок. После сверления и антисептирования костыльных отверстий шпалы направляются на цепной конвейер. Здесь на шпалы вручную раскладывают подкладки и наживляют обшивочные костыли.
Конвейер подает шпалы к сборочному станку, перед которым наживляют пришивочные костыли. Выше цепного конвейера расположены ролики, на которых козловыми кранами укладывают рельсы. В сборочный станок рельсы и шпалы подаются автоматически.
В заключение на сборочном станке вдавливаются наживленные костыли в шпалу (рис. 13.5).
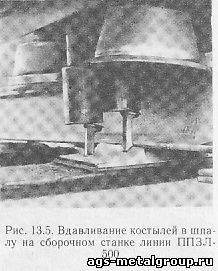
Механизированная поточная линия ЗЛХ-800 имеет более высокую производительность - 700 - 800 м в смену.
Звеносборочная линия ЗЛЖ-650 (рис. 13.6) производительностью 650 м в смену обслуживается 24 монтерами пути, тремя механиками, бригадиром пути и дорожным мастером. Технология сборки звеньев с железобетонными шпалами на этой линии следующая. Шпалы козловым краном укладывают на шпалопитатель. Дальнейшее перемещение шпал осуществляется на тележках с подъемником, имеющим возвратно-поступательное движение. На тележках на шпалы раскладывают резиновые прокладки и подкладки и устанавливают закладные болты. Скомплектованные таким образом шпалы гидравлическими домкратами поднимаются к сборочному станку. Одновременно к сборочному станку по роликам перемещаются рельсы.
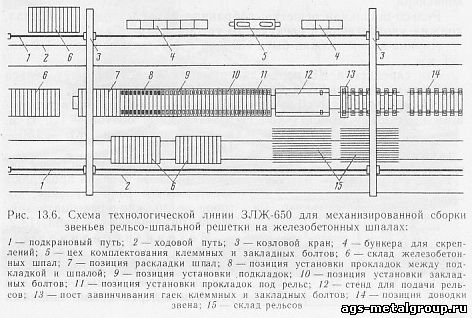
После подъема шпалы и прижатия подкладок к подошве рельса устанавливают клеммные болты, полностью скомплектованные заранее. Клеммные и закладные болты заболчиваются автоматически. При подъеме следующей шпалы рельс с предыдущими шпалами перемещается строго на шаг эпюры.
Управление линией осуществляется с центрального пульта, размещенного в закрытой кабине. Протяженность линии 80 м.
Звеносборочная линия ЗЛХ-650 (рис. 13.7) производительностью 650 м в смену монтируется на двух путях: на одном пути размещен участок подготовки звена, на другом - участок сборки.
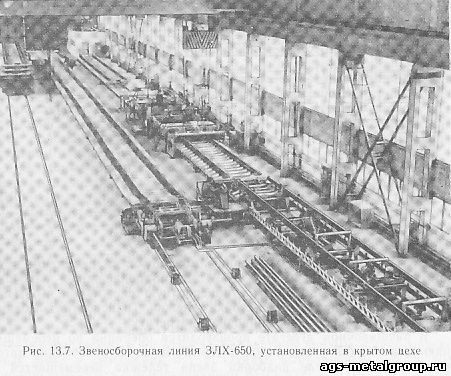
На первом участке козловыми кранами загружают головной стенд линии железобетонными шпалами. Вслед за этим раскладывают прокладки, подкладки и устанавливают закладные болты. Шпалы перемещаются по потоку циклично и автоматически.
Затем поперечным транспортером шпалы передаются на второй поток, где они подходят под движущиеся рельсы. Здесь устанавливаются клеммные болты и завинчиваются гайки клеммных и закладных болтов.
Звеносборочная линия ПЗЛ-850 производительностью 850 м в смену изготовлена с использованием специальной траверсы, которой оборудованы козловые краны. Траверса (рис. 13.8) имеет конструкцию, позволяющую брать из штабелей железобетонные шпалы и располагать их по эпюре.
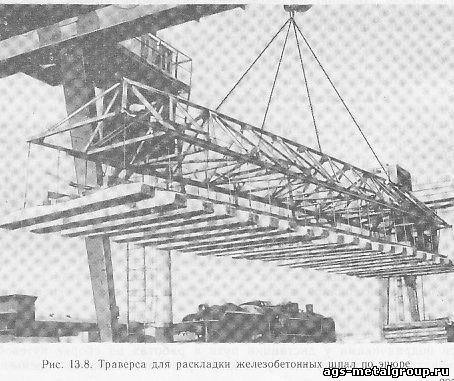
Звено собирается на пяти стендах, перемещаясь от стенда к стенду в процессе его монтажа на специальных тележках с возвратно-поступательным ходом и с шагом 12,5 м.
Звеносборочная линия «Смолянка» производительностью 800 - 1000 м в смену сконструирована на принципе конвейера.
Рельсо-шпальная решетка, собранная из железобетонных шпал, должна удовлетворять следующим требованиям:
- ширина колеи должна быть 1520 мм с допуском не более +2 мм, - 1 мм;
- при скреплении КБ перед завертыванием гаек подошву рельса необходимо прижимать к наружным ребордам подкладки;
- гайки клеммных болтов затягиваются с усилием, соответствующим крутящему моменту 150 Н м, закладных болтов - 120 Н м, а при скреплении ЖБ - 150 - 180 Н м.
В собранных для участков с автоблокировкой звеньях проверяют электрическое сопротивление, которое не должно превышать значений, приведенных в табл. 13.2.
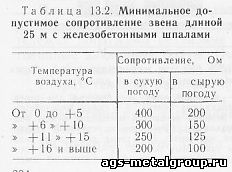
Механизированная поточная звеноразборочная линия ЗРС предназначена для демонтажа рельсо-шпальной решетки с деревянными шпалами и костыльным скреплением. Линию монтируют на рельсовом пути протяженностью 140 м (рис. 13.9). Звено подлежащей разборке решетки укладывают краном на транспортную тележку так, чтобы подошвы рельсов опирались на стойки тележки. Транспортная лебедка перемещает тележку к расшивочному агрегату.
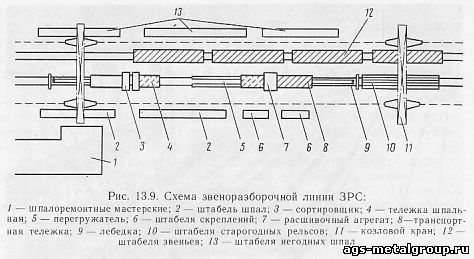
В расшивочном агрегате производятся операции по перемещению звена, захвату подкладок.и отрыву шпал. Эти операции автоматизированы. После разборки звена тележка перемещается к перегружателю. На перегружателе происходит подъемка шпал с рельсами над тележкой и последняя возвращается на исходное положение. Рельсы с перегружателя убираются краном. На место первой тележки под вывешенные перегружателем шпалы подается вторая тележка, на которую и опускаются шпалы. Лебедка перемещает тележку к сортировщику, где шпалы сортируются на годные и негодные для ремонта.
Производительность линии 90 м/ч. Линию обслуживают 10 чел., в том числе 6 монтеров пути.