СВОБОДНАЯ КОВКА
§ 15. Сущность процесса и виды ковки
При ковке металла между плоскими бойками имеет место свободное течение его в стороны, поэтому такая ковка получила название свободной.
Свободная ковка экономически выгодна при получении фасонных заготовок стальных деталей с высокими механическими свойствами в условиях индивидуального и мелкосерийного производства.
К преимуществам ковки по сравнению с другими способами обработки металлов, например литьем, резанием, штамповкой, относятся: ее универсальность в отношении веса, формы и размеров партии изготовляемых заготовок; обеспечение высоких механических свойств металла в изделиях, отсутствие затрат на дорогостоящую технологическую оснастку; возможность использования сравнительно маломощных машин - орудий благодаря концентрированному приложению усилий ковки в ограниченном бойками небольшом объеме деформируемого металла.
В промышленности свободная ковка применяется для изготовления поковок шестерен, турбинных роторов и дисков, валов, шатунов, колец и других ответственных деталей машин. Свободная ковка является пока незаменимой в производстве крупных деталей, несмотря на ряд присущих ей недостатков. К ним относятся, например, сравнительно низкая производительность труда и небольшая точность ковки, вызывающая необходимость значительных припусков и напусков металла, что приводит к повышению расхода материала и стоимости готовых деталей.
Свободная ковка разделяется на ручную и машинную. Ручная ковка применяется редко, главным образом в ремонтных мастерских при изготовлении небольших поковок и почти не имеет промышленного применения на заводах. Машинная ковка производится на ковочных молотах и прессах. На молотах изготовляют поковки массой от 0,5 до 100 кг, используя в качестве исходного материала сортовой прокат сечением до 250х250 мм и обжатую болванку (блюмсы) сечением до 450Х450 мм. На гидравлических ковочных прессах изготовляют поковки массой от 100 кг до 230 т, из стальных слитков массой от 1,2 до 350 т.
§ 16. Основные операции технологического процесса ковки и приемы их выполнения
Технологический процесс машинной свободной ковки состоит из ряда элементарных кузнечных операций, выполняемых в определенной последовательности с целью получения из исходной заготовки простой формы (слитка, блюмса) фасонной поковки требуемых размеров и формы.
Кроме чисто кузнечных операций полный технологический процесс изготовления поковки, фиксируемый в специальной технологической карте, включает также заготовительные операции (резку или рубку заготовок и их контроль), нагрев металла под ковку, охлаждение поковок, контрольные операции по проверке размеров и механических свойств поковки (если это требуется техническими условиями), а также операции первичной термической обработки поковок (отжиг, нормализацию), выполняемые обычно в кузнечном цехе.
Основными операциями процесса свободной ковки являются осадка, вытяжка, прошивка, гибка, рубка. К менее распространенным кузнечным операциям относятся передача металла, закручивание и кузнечная сварка. Кроме перечисленных операций в процессе изготовления поковок применяются и их разновидности: высадка в подкладных кольцах, представляющая собой частичную осадку заготовки по ее высоте; обкатка по диаметру (после осадки), вытяжка и раздача кольцевых поковок на оправке. В ряде случаев технологический процесс ковки включает операции горячей штамповки в подкладных штампах под молотом.
Наличие тех или иных кузнечных операций, а также порядок их чередования определяются формой изготовляемой поковки. Так, например, при изготовлении поковок типа валов применяются главным образом вытяжка и рубка, а в случае ковки коленчатых валов вытяжка и передача металла. При изготовлении кольцевых поковок применяют осадку, прошивку, раздачу, а иногда и вытяжку на оправке. Для ковки фланцевых поковок характерны высадка, прошивка, обкатка по диаметру.
При машинной ковке заготовка укладывается на нижний неподвижный боек молота или пресса, а затем деформируется или непосредственно верхним подвижным бойком или с применением подкладного инструмента, помещаемого между верхним бойком и заготовкой.
Бойки бывают плоскими и вырезными (рис. IV.20, а). Вырезные бойки используют при ковке валов, их применение ускоряет процесс ковки и повышает пластичность металла во время деформации.
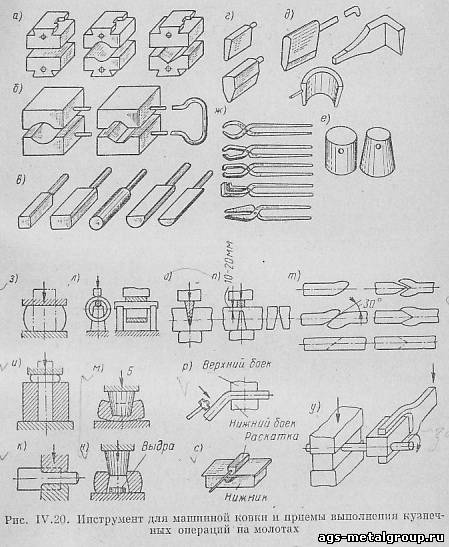
Подкладными инструментами служат: обжимки (рис. IV.20, б) для отделки цилиндрических и граненых поверхностей после предварительной вытяжки поковок на плоских бойках; раскатки (рис. IV.20, в) для местной деформации металла, например при ковке односторонних уступов; пережимки (рис. IV.20, г) для разметки материала при ковке и пережима металла заготовки на объемы, идущие на образование отдельных частей поковки; тоноры (рис. IV.20, д) и квадраты для рубки металла; прошивни (рис. IV.20, е) для пробивки отверстий; оправки для калибровки прошитых отверстий; оправки для раздачи отверстий и вытяжки пустотелых поковок (рис. IV.20, л).
Для переноса, поддержания, подачи и кантовки небольших заготовок пользуются клещами различных конструкций и размеров (рис. IV.20, ж). При ковке крупных поковок для этой цели используют простейшие приспособления: самозажимные клещи, воротяжки, вилки, подвешиваемые на цепном блоке консольно-поворотных кранов, устанавливаемых у молотов, а также механические кантователи и манипуляторы подвесного и напольного типов.
При осадке заготовка устанавливается вертикально на нижний боек молота (рис. IV.20, з) и деформируется ударами верхнего бойка по торцу заготовки. Осадка вызывает увеличение поперечного сечения заготовки за счет уменьшения ее высоты. Во избежание продольного изгиба длина осаживаемой заготовки не должна превышать 2,5 ее диаметра. Разновидностью осадки является высадка, представляющая собой частичную осадку заготовки по высоте (рис. IV.20, и). При высадке заготовку устанавливают в стальное подкладное кольцо на бойке молота и деформируют только верхнюю свободную часть заготовки.
При вытяжке (рис. IV.20, к) заготовка укладывается плашмя поперек бойков молота и деформируется последовательными обжатиями. После каждого удара заготовка кантуется т. е. поворачивается на 90° вокруг продольной оси, и подается вперед в направлении вытяжки. Вытяжка вызывает увеличение длины заготовки за счет уменьшения площади ее поперечного сечения.
При изготовлении кольцевых поковок с отверстиями большого диаметра применяют раздачу (раскатку) колец на оправке (рис. IV.20, л), представляющую собой частный случай вытяжки. При раздаче увеличиваются наружный и внутренний диаметры поковки за счет уменьшения толщины ее обода. Поковку после каждого удара молота поворачивают на небольшой угол клещами вокруг стальной оправки, установленной на опорных стойках (скобе) на нижнем бойке молота.
Прошивка - операция, посредством которой в заготовках получают сквозные отверстия. Отход металла при прошивке называется выдрой. Применяют два способа прошивки: с применением подкладного кольца и прошивку с двух сторон, с переворачиванием поковки.
При прошивке на кольце осаженная заготовка, обычно небольшой толщины, укладывается на стальном кольце, находящемся на нижнем бойке молота. В центре заготовки устанавливается конусный прошивень, широким основанием вниз, который затем внедряется в заготовку сначала легкими, а затем сильными ударами верхнего бойка. При этом металл вначале выдавливается из-под прошивня в стороны, а затем происходит срез его по цилиндрической поверхности, с образованием выдры, проваливающейся вниз под давлением прошивня. При этом способе прошивки объем металла выдры составляет около 3/4 объема получаемого отверстия.
При прошивке с двух сторон, применяемой для поковок большой толщины, заготовку укладывают непосредственно на боек молота, устанавливают на ней конусный прошивень, узким основанием вниз (рис, IV.20. л) и легкими ударами верхнего бойка по прошивню производят глухую прошивку примерно на 3/4 высоты заготовки. Затем прошивень удаляют клещами или ударами по тыльной стороне поковки, положенной на кольцо, и, установив поковку на боек глухим отверстием вниз, производят сквозную прошивку ее с обратной стороны (рис. IV. 20, и). Выдра получается небольшой высоты и по объему составляет около 1/4 объема прошиваемого отверстия.
Рубка металла также производится двумя приемами: сначала нагретая заготовка надрубается кузнечным топором с одной стороны (рис. IV.20, о), а затем переворачивается на 180' и разрубается окончательно стальным прутком квадратного сечения - квадратом (рис. IV.20, п).
Гибку при изготовлении штучных поковок выполняют ударами кувалды по концу заготовки, зажатой между бойками молота (рис. IV.20, р). При изготовлении партии одинаковых поковок гибку осуществляют в нижнике (подкладном штампе) с применением вершника или раскатки (рис. IV.20, с).
Для закручивания колен поковки вала одно колено зажимают бойками молота, а на другое надевают массивную вилку, конец которой медленно поворачивают (рис. IV.20, у).
Кузнечная сварка (рис. IV. 20,т) почти полностью вытеснена более совершенными способами электрической и газовой сварки.
§ 17. Разработка чертежа поковки
Чертеж поковки является основным технологическим документом для кузнечного цеха. По нему производится изготовление и приемка готовой поковки. Чертеж поковки разрабатывается по чертежу готовой (обработанной на станках) детали и представляет собой графическое изображение поковки, выполненное в определенном масштабе с указанием всех размеров необходимых для ее изготовления.
Поковка отличается от готовой детали наличием припусков на механическую обработку и напусков металла.
Напуском металла называется местное увеличение припуска, упрощающее конфигурацию поковки ввиду невозможности или нерентабельности ее изготовления в соответствии с точной формой детали. Напусками металла перекрываются отверстия небольшого диаметра, небольшие по высоте уступы на валах, пазы, проточки и т. п.
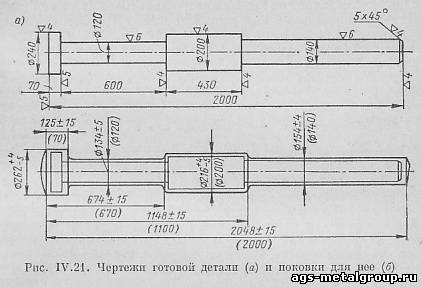
Величина припуска зависит от сложности формы и габаритных размеров детали и учитывает дефекты наружного слоя металла (окалину, вмятины от нажимов кузнечного инструмента, обезуглероживание поверхности), которые должны быть удалены при обработке резанием для получения необходимой чистоты поверхности и точных размеров детали.
Номинальные (округленные) размеры поковки с учетом припусков и напусков металла проставляются над размерными линиями на чертеже поковки. Под размерными линиями, в скобках, проставляются размеры готовой детали.
На чертеже поковки указываются также допустимые предельные отклонения от номинальных размеров поковки со знаками плюс и минус, учитывающие возможную точность ковки на молоте или прессе.
Припуски и допуски на типовые поковки (пластины, валы кольца и т. п.), изготовляемые ковкой на гидравлических прессах и молотах, выбираются по таблицам ГОСТов 7062 - 67 и 7829 - 70. Величины припусков по диаметру для крупных прессовых поковок гладких валов длиной от 1 до 20 м составляет 16 - 55 мм на сторону, а величины предельных отклонений от ±6 до ±18 мм. Припуски по диаметру для поковок гладких валов длиной 250 - 2500 мм; изготовляемых на молотах, составляют 5 - 18 мм, а предельные отклонения от ±2 до ± 5 мм соответственно.
Пример чертежа поковки вала с уступами, изготовляемого ковкой на молоте, приведен на рис. IV.21.
§ 18. Оборудование для свободной ковки
Оборудование кузнечных цехов делится на основное и вспомогательное.
К основному оборудованию, выполняющему деформацию металла при ковке, относятся молоты и прессы.
К вспомогательному оборудованию относятся машины для резки заготовок - пресс-ножницы, дисковые пилы; нагревательные печи; механизмы, транспортирующие и поддерживающие заготовки при ковке - ковочные подъемные краны, кантователи, манипуляторы.
Основное кузнечное оборудование различается по скорости рабочего хода, т. е. хода, на протяжении которого производится деформирование поковки. Скорость бойка молота к моменту удара по заготовке значительна и достигает 7 - 8 м/сек; последующая деформация металла осуществляется за счет кинетической энергии, накопленной тяжелыми падающими частями (поршнем, штоком, бабой и верхним бойком) к моменту удара бойка о заготовку. Поэтому говорят, что молоты - это машины динамического действия, работающие ударом. Ковочные гидравлические прессы деформируют металл значительным статическим усилием, при сравнительно небольшой скорости рабочего хода - 0,1 - 0,3 м/сек.
По виду энергии, приводящей в движение падающие части, молоты разделяются на паровые и приводные (с электроприводом). Паровые молоты без особых переделок могут работать и на сжатом воздухе, поэтому их часто называют паровоздушными молотами. Приводные молоты разделяются на пневматические, с индивидуальным компрессором, встроенным в станину молота, рессорные и рычажные. Из них наибольшее применение имеют пневматические молоты.
По принципу действия пара или сжатого воздуха на поршень различают молоты простого и двойного действия. В молотах простого действия давление пара (или воздуха) на поршень снизу используется только для подъема падающих частей вверх. Падение их вниз происходит только под действием силы тяжести. В молотах двойного действия пар (воздух) поступает и в верхнюю часть цилиндра молота, над поршнем, при движении падающих частей вниз. В этом случае они получают добавочные ускорение и скорости, и, следовательно, молот двойного действия развивает ббльшую силу удара, чем молот простого действия, при той же массе падающих частей.
По конструкции станины паровоздушные молоты разделяются на одностоечные, для более легких работ, с массой падающих частей от 0,25 до 1 т и двухстоечные с массой падающих частей от 1 до 8 т. Наиболее удобными для ковки крупных фасонных поковок являются тяжелые мостовые трех- восьмитонные молоты, обеспечивающие возможность подхода к бойкам со всех сторон.
Устройство и принцип действия паровоздушного двухстоечного молота показаны на рис. IV.22.
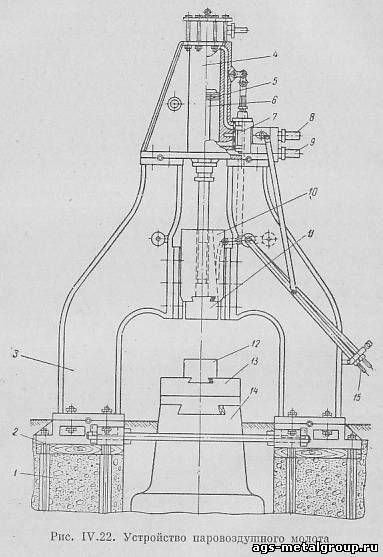
К бетонному фундаменту 1 через эластичную прокладку из дубовых досок 2, смягчающую действие ударов, крепятся фундаментными болтами стойки станины 3. К верхней части стоек на болтах крепится подцилиндровая плита, отлитая вместе с цилиндром 4. Внутри цилиндра может передвигаться под действием пара или воздуха поршень 5, соединенный со штоком 6, к которому прикреплена баба 10, являющаяся основным элементом падающих частей молота. Верхний боек 11 крепится к бабе молота посредством соединения типа ласточкина хвоста и стального клина. Таким образом, падающие части молота состоят из поршня, штока, бабы и верхнего бойка. Суммарная масса падающих частей и характеризует мощность молота.
Деформируемая ударами верхнего бойка заготовка устанавливается на нижнем неподвижном бойке 12. Последний через переходную подушку 13 крепится к массивному шаботу 14, который устанавливается на прокладке из дубовых брусьев на бетонном фундаменте.
Свежий пар поступает по паровпускной трубе 8 через цилиндрический золотник 7 в криволинейные каналы в отливке цилиндра.
Перемещение золотника посредством системы рычагов от рукоятки управления 15 позволяет направлять пар попеременно в верхнюю и нижнюю полости цилиндра (над поршнем и под поршнем).
При нажиме машинистом молота рукоятки вниз золотник 7 молота поднимается вверх и тогда свежий пар по верхнему криволинейному каналу в стенке цилиндра поступает в верхнюю полость цилиндра, давит на поршень сверху и вызывает ускоренное движение падающих частей вниз. При этом отработанный пар из нижней полости цилиндра через нижний криволинейный канал в стенке отливки цилиндра выходит под золотником в паровыхлопную трубу 9.
При подъеме рукоятки управления 15 вверх золотник 7 перемещается вниз. Свежий пар, поступая из паровпускной трубы 8, обходит среднюю часть золотника, имеющую меньший диаметр, и поступает под поршень в нижнюю полость цилиндра по нижнему каналу в стенке цилиндра. Давление пара на поршень снизу вызывает подъем его вместе с бабой молота вверх. Отработанный пар при этом выходит через верхний криволинейный канал, проходит сверху вниз сквозь полый золотник и поступает в паровыхлопную трубу 9.
В верхней части цилиндра крепится предохранительный буфер, предупреждающий удар поршня в крышку цилиндра при чрезмерном заполнении свежим паром нижней полости цилиндра. Пар давлением в 7 - 9 ат (0,7 - 0,9 МПа) поступает к молотам по трубопроводу из центральной котельной. Если молот работает на сжатом воздухе, то последний подается по трубопроводу от компрессорной станции.
Мощность молота выбирают в зависимости от веса и сложности формы поковки. Так, например, на полутонном молоте можно отковать фасонную поковку массой до 25 кг или гладкий вал массой до 100 кг, а на пятитонном - фасонную поковку массой до 700 кг или гладкий вал массой 1500 кг.
Пневматические (приводные) молоты с массой падающих частей 75 - 1000 кг широко применяются в кузнечных цехах и ремонтных мастерских для ковки небольших поковок и для штамповки в подкладных штампах.
Пневматический молот имеет два вертикальных параллельно расположенных цилиндра - рабочий, в котором ходит поршень составляющий одно целое с бабой, и компрессорный. Поршень компрессорного цилиндра приводится в возвратно-поступательное движение шатуном от кривошипного вала, который получает вращение от электродвигателя через редуктор. Все части молота смонтированы на литой пустотелой станине.
При движении поршня компрессора происходит попеременное сжатие воздуха в нижней и верхней полостях компрессорного цилиндра. Сжатый воздух через распределительные каналы и поворотные краны попеременно поступает в верхнюю и нижнюю полости рабочего цилиндра. В результате при вращении кривошипного вала поршень-баба молота непрерывно двигается вверх и вниз, нанося автоматические удары по поковке. Имеющаяся система управления обеспечивает работу молота и по остальным циклам: единичные удары, прижим поковки, удерживание бойка на весу и т. д. Сила удара регулируется нажимом на рукоятку управления.
Гидравлические ковочные прессы применяют для ковки крупных поковок.
В гидравлическую прессовую установку входят: собственно пресс; механизм, питающий пресс жидкостью высокого давления (привод); устройства, питающие пресс жидкостью низкого давления (резервуары-наполнители). В качестве рабочей жидкости в ковочных прессах применяется вода с раствором в ней 2 - 3 % эмульсола, состоящего из минерального масла, олеиновой кислоты и едкого натра.
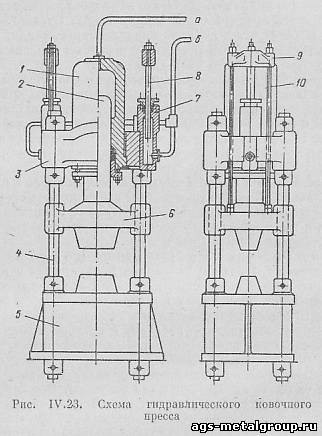
Схема четырехколонного гидравлического ковочного пресса приведена на рис. IV.23. В нижней поперечине (плите) пресса 5, установленной на бетонном фундаменте, закреплены при помощи массивных гаек четыре колонны 4. Эти колонны связывают нижнюю поперечину с верхней (архитравом) 3, образуя жесткую станину пресса. Диаметр этих колонн у мощных прессов достигает 1 м, а высота - 25 м. В верхней поперечине закреплен главный рабочий цилиндр пресса 1, в который входит главный плунжер 2, соединенный с подвижной поперечиной (траверсой) 6, к которой крепится верхний боек. Нижний боек закреплен в нижней плите пресса 5.
Холостой ход траверсы с бойком вниз до соприкосновения со слитком осуществляется при поступлении в главный цилиндр жидкости низкого давления из наполнительного бака. Наполнительные баки бывают закрытые, жидкость в которых находится под давлением сжатого воздуха в 4 - 8 кГ/см² (0,4 - 0,8 МПа), или открытые, устанавливаемые выше уровня рабочего цилиндра пресса.
Рабочий ход осуществляется при подаче жидкости под высоким давлением в 200 - 500 кГ/см² (20 - 50 МПа) в главный цилиндр пресса по трубе а. При этом происходит движение плунжера с траверсой вниз по направляющим колоннам 4 и осуществляется деформация слитка, лежащего на нижнем бойке.
Обратный ход - подъем траверсы с верхним бойком после рабочего хода осуществляется двумя возвратными (подъемными) цилиндрами 7, закрепленными в верхней поперечине. При обратном ходе жидкость под давлением (или пар в парогидравлических прессах) поступает по трубе б в нижнюю часть подъемных цилиндров, давит на подъемные плунжеры 8 и заставляет их поднимать траверсу 6 посредством тяг 10 и поперечины 9.
Жидкость высокого давления подается либо насосом или насосно-аккумуляторной установкой (чисто гидравлические прессы), либо специальным умножителем давления - паровым мультипликатором (парогидравлические прессы).
Насосно - аккумуляторный привод обеспечивает наибольшие величину и скорость рабочих ходов пресса, достигающую 0,5 м/сек.
Мультипликаторный привод имеет меньший к. п. д., но обеспечивает большее число ходов пресса в минуту (до 60) при небольших обжатиях на отделке поковок (шлихтовочные ходы) и допускает получение значительных рабочих усилий на бойке пресса за счёт применения более высоких давлений рабочей жидкости (400 - 500 кГ/см²) (40 - 50 МПа).
Гидравлические прессы работают без ударов и сотрясений почвы, усилия, развиваемые ими, воспринимаются колоннами и не передаются на фундамент. Поэтому для них не нужен шабот и массивный фундамент, как у тяжелых молотов.
Одностоечные ковочные прессы для ковки небольших поковок сложной формы выпускаются усилием в 300 и 600 т (2,94 и 5,9 МН). Четырехколонные прессы для крупных поковок строятся усилием 500 - 15000 т (4,9 - 147 МН).
Мощные ковочные прессы имеют два-три рабочих цилиндра и могут работать с различными усилиями при действии одного, двух или трех цилиндров.
На прессе усилием в 1000 т (9,81 МН) можно ковать слитки массой до 8 т, а на прессе усилием в 15 000 т (147 МН) - слитки массой до 350 т. При сравнении мощности молота и пресса принимают 1 т массы падающих частей молота примерно эквивалентной 100 т (0,981 МН) усилия пресса.
§ 19. Технология ковки типовых поковок
Технологический процесс свободной ковки состоит из подбора заготовки и подготовки ее к ковке, нагрева металла, собственно ковки на молоте или прессе для придания заготовке заданной формы и размеров и, наконец, отделки и контроля поковки.
При серийном производстве поковок на заводах разрабатываются технологические карты, в которых фиксируется вся последовательность процесса изготовления поковки по операциям и переходам ковки. К технологической карте прикладывается чертеж поковки.
Ниже приводятся технологические процессы ковки двух типовых поковок: вала с фланцем и шестерни.
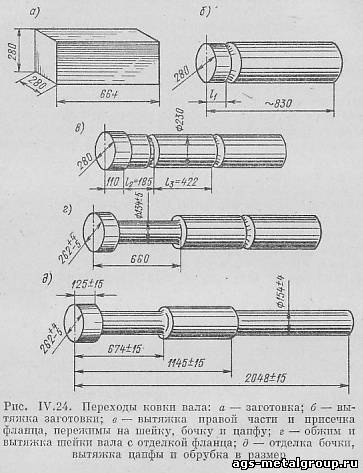
Ковка вала с фланцем. Поковка вала массой 382 кг из стали 45 изготовляется на молоте 3 т из заготовки длиной 664 мм, сечением 280 х 280 мм.
Заготовка (рис. IV.24,а), отрезанная кислородным резаком, нагревается в камерной печи до 1200' С и подается на боек молота консольным краном с подвесным кантователем.
За первый переход (рис. IV.24,б) заготовка проковывается по диагоналям квадрата и протягивается на диаметр 280 мм (несколько больший диаметра фланца), так как при последующем пережиме на фланец неизбежна утяжка металла в углах. За второй переход выполняется пережим металла угловой пережимкой с выкружкой на длине присечки l₁, которая определяется делением объема металла, идущего на образование фланца, на площадь сечения F₁ заготовки диаметром d₁ = 280 мм:

За третий переход правая часть заготовки (рис. IV.24,в) протягивается на диаметр d₂ = 230 мм, несколько больший диаметр бочки вала D₂ = 216 мм, с учетом утяжки металла при последующем пережиме металла на шейку и правую цапфу вала.
В четвертом переходе выполняется пережим на длинах присечки:
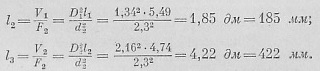
За пятый переход обжимается шейка вала, сначала раскатками и на плоских бойках, а затем в обжимках диаметром 135 мм в размер по эскизу (рис. IV.24,г). Отделывается по диаметру фланец до поковочного размера. После этого правая часть поковки закладывается в печь для подогрева до 950' С. Невысокий подогрев, достаточный для окончания ковки вала, предупреждает рост зерен металла, в почти начисто откованной бочке и готовой левой части вала.
В шестом переходе протягивается до окончательных размеров бочка вала в обжимках диаметром 215 мм.
В последнем переходе (рис. IV.24,д) обжимается на бойках цапфа вала, отделывается в обжимках диаметром 155 мм и отрубается концевой отход. Ковка заканчивается при 800' С. После проверки размеров и качества ковки поковка направляется на участок термической обработки для нормализации: нагрева в печи до 850 - 870'С с последующим охлаждением на воздухе. Цель нормализации - измельчение структуры металла и повышение механических свойств поковки.
§ 20. Механизация ковочных работ и технико-экономические показатели ковки
Для механизации трудоемких и тяжелых операций ковки крупных поковок на молотах и гидравлических прессах применяют манипуляторы.
Манипулятор, или «механический кузнец» снабжен мощными механизированными клещами, которыми зажимается один конец заготовки или слитка массой до 30 т. Поворачиваясь относительно своей оси, клещи могут приподниматься и перемещаться в разных направлениях. Манипулятор может перемещаться по рельсам или по полу цеха. Это позволяет кузнецу без труда осуществлять все нужные изменения положения поковки.
Помимо манипулятора при ковке крупных поковок используются специальные мостовые краны, оснащенные подвесными кантователями для подачи и поворачивания слитков массой до 200-300 т.
Гидравлические прессы снабжаются выдвижными столами, которые облегчают подачу и удаление слитков, смену бойков и другого инструмента.
В последние годы на ряде заводов внедрена автоматизация управления ковочными гидравлическими прессами и обслуживающими их манипуляторами. При этом используется. следящее устройство СШТ-11, обеспечивающее автоматическое управление прессом с помощью радиоактивных изотопов. Успешная эксплуатация этого устройства на Невском машиностроительном заводе им. В. И. Ленина обеспечила улучшение условий тяжелого труда машиниста пресса, повышение точности ковки в два-три раза, снижение общей трудоемкости изготовления деталей с повышением производительности пресса на 15-30%.
Наши ученые и производственники работают сейчас над решением задач дальнейшей автоматизации технологических процессов ковки и скоростной разработки технологических карт с применением электронно-вычислительных машин, а конструкторы - над созданием кузнечных машин с программным управлением.
Технико-экономические показатели ковки характеризуются следующими данными. Выпуск поковок с 1 т массы падающих частей молота составляет 200 - 400 кг/ч, с 1000 т давления гидравлического пресса 2,5 - 4 т/ч. Выход годного металла, определяемый отношением массы партии готовых поковок к массе исходных заготовок, при изготовлении поковок из сортового проката на молотах составляет в среднем 90 - 94%, а при ковке из слитков под прессами - 62 - 66% .
Коэффициент весовой точности поковок k вт = G д/G пк (где G д - вес детали, G пк - вес поковки), характеризующий техническую культуру производства, находится в среднем при свободной ковке в пределах 0,40 - 0,50. Таким образом, объем металла, снимаемого резанием, составляет 150 - 100% от веса готовой детали.