ОБЪЕМНАЯ ШТАМПОВКА
§ 21. Сущность процесса горячей штамповки и область ее применения
В отличие от свободной ковки, когда деформация металла на плоских бойках происходит в разных направлениях, при штамповке течение металла ограничено стенками рабочей полости (ручья) штампа и происходит по заданным направлениям до определенного предела. При этом форма и размеры ручья штампа полностью определяют конфигурацию изготовляемой поковки. Штампы по конструкции могут быть одноручьевыми - для деталей простой формы, и многоручьевыми - для сложных.
Для изготовления поковок методами горячей объемной штамповки применяют штамповочные молоты, кривошипные ковочно-штамповочные прессы, фракционные прессы, горизонтально-ковочные машины, ротационно-ковочные машины, ковочные вальцы. На выбор того или иного оборудования для штамповки оказывают влияние форма и размеры изготовляемой поковки, ее материал, серийность производства, требуемая точность размеров и другие факторы. В ряде случаев целесообразно применять комбинированный процесс штамповки на различных видах оборудования, например штамповку коленчатого вала автомобильного двигателя производят на штамповочном молоте, а последующую штамповку фланца на конце вала выполняют на горизонтально-ковочной машине. Часто комбинируют предварительное формообразование заготовки на ковочных вальцах с последующей штамповкой ее на кривошипном прессе.
Горячая штамповка по сравнению с ковкой обладает рядом преимуществ. К ним относятся: высокая производительность, в десятки раз превышающая производительность свободной ковки, однородность и точность получаемых поковок; высокое качество поверхности штампуемых поковок, что позволяет обрабатывать их только в местах сопряжений с другими деталями; возможность получения поковок весьма сложной конфигурации, с минимальными напусками металла. Внедрение горячей штамповки взамен ковки обеспечивает массовый выпуск дешевой продукции благодаря значительному снижению расхода металла на поковки и трудоемкости их последующей обработки.
К недостаткам штамповки относятся: относительно небольшая масса поковок (обычно до 200 - 300 кг) и высокая стоимость штампов, которые в отличие от универсальных кузнечных инструментов являются специализированным инструментом, пригодным для изготовления только одной определенной поковки. Поэтому применение штамповки экономически выгодно лишь при серийном или массовом производстве. Горячую объемную штамповку применяют в машиностроении и других отраслях промышленности для изготовления сложных по форме заготовок ответственных деталей машин из стали и цветных сплавов.
После штамповки поковки подвергают отделочным операциям: обрезке облоя и зачистке заусенцев, правке и калибровке, очистке поверхности.
Облоем называют некоторый избыток металла в исходной заготовке, вытесняемый в заключительной фазе процесса штамповки в облойную канавку, состоящую из узкого зазора - мостика и расширенной части - магазина (рис. IV.25,а). Применяют два основных метода штамповки: в открытых штампах, с образованием облоя, и в закрытых штампах - безоблойную.
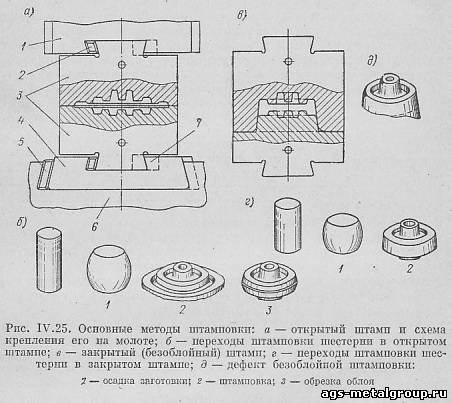
Открытым называют штамп, из рабочей полости которого облой имеет выход в облойную канавку, расположенную по периметру ручья штампа (рис. IV.25,а). Такой штамп состоит из двух частей (половин) 3 - верхней и нижней. Верхняя часть посредством хвостовика (в виде ласточкина хвоста) и стального клина 2 крепится в пазу бабы 1-штамповочного молота и при работе молота наносит удары по нагретой заготовке, устанавливаемой клещами в ручей нижней, неподвижной половины штампа. Нижняя часть штампа крепится клином в штамподержателе 4 (переходной стальной подушке), а последний также посредством клина 5 - в пазу шабота 6 молота. Смещение штампов в долевом направлении предупреждается стальными сухарями (шпонками) 7.
Образующийся при штамповке облой затрудняет вытеснение металла наружу из ручья штампа, так как щель канавки в мостике узка (2 - 5 мм). При этом давление металла в полости штампа повышается и он вынужден заполнять весь сложный ее рельеф, обеспечивая хорошее формообразование поковки. Отход металла в облой составляет в среднем 10 - 20% от массы поковки. Переходы штамповки поковки шестерни в открытом штампе приведены на рис. IV.25,б.
Метод штамповки в открытых штампах на молотах и прессах является наиболее распространенным и универсальным, так как он применим для изготовления поковок как простой, так и весьма сложной формы (шатунов, крестовин, коленчатых валов и др.).
3акрытым, или безоблойным, называют штамп, полость которого не имеет выхода для избытка металла (рис. IV.25,6). В отличие от открытых штампов, имеющих поверхность разъема в виде плоскости, закрытые штампы имеют разъем по сложной поверхности с направляющим замком, обеспечивающим точное соударение половин штампа в конце процесса штамповки. При этом выступ нижней части штампа при последних ударах молота запирает рабочую полость, расположенную в основном в верхней части штампа, закрывая выход металлу из ручья штампа (рис. IV.25,в).
Безоблойная штамповка обеспечивает снижение расхода металла до 20% и экономию на затратах, связанных с обрезкой облоя. Переходы штамповки поковки той же шестерни в закрытом штампе приведены на рис. IV.25,г.
Однако закрытые штампы для деталей сложной формы конструктивно трудно выполнимы, дороги в изготовлении и быстро выходят из строя. Кроме того, применение безоблойной штамповки требует точной резки заготовки по объему (массе), повышенной внимательности штамповщиков и точной установки заготовки по центру ручья штампа, иначе возможен брак по односторонним торцевым заусенцам и незаполнению формы штампа (рис. IV.25,д).
В качестве исходного материала при горячей штамповке в открытых и закрытых штампах применяют обычно стальной прокат круглого и квадратного профиля или прессованные прутки из цветных металлов и сплавов.
Массу исходной заготовки Gз при штамповке в открытых штампах определяют по формуле Gз = Gшп + Gy + Go, где Gшп - масса штампованной поковки; Gy - масса угара при нагреве; Go - масса облоя.
Массу штампованной поковки Gшп определяют по ее объему Vшп, подсчитанному по номинальным размерам чертежа поковки (с учетом припусков и напусков металла) Gшп = Vшпу, где у - плотность металла в г/см³.
Массу угара Gy принимают при пламенном нагреве равной 3% от Gшп, а при электронагреве токами высокой частоты или контактном - 0,5% от Gшп.
Массу облоя Go ориентировочно определяют по формуле Go = nyfoS, где n = 0,5 ÷ 0,8 - коэффициент заполнения облойной канавки металлом; fo - поперечное сечение облойной канавки в см² (выбирается по таблице справочника в зависимости от веса поковки); S - периметр поковки в плоскости разъема штампов в см.
Чертеж штампованной поковки является основным технологическим документом, определяющим конфигурацию и размеры поковки после штамповки. По нему проектируют ковочный, обрезной и проколочный штампы, а также принимают готовую продукцию контролеры ОТК. Чертеж штампованной поковки (рис. IV.26,6) разрабатывают по чертежу готовой детали (рис. IV, 26, а) в соответствии с принятым технологическим процессом штамповки.
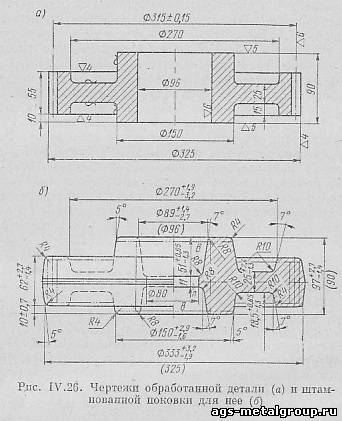
При проектировании детали, намеченной к изготовлению горячей штамповкой, и составлении ее рабочего чертежа конструктор должен наряду с эксплуатационными требованиями к детали учитывать и технологические требования к ее конструкции, обеспечивающие возможность изготовления детали штамповкой.
Основные требования технологичности конструкции для горячештампованных деталей, обычно не обрабатываемых кругом, сводятся к правильному выбору плоскости разъема штампа, назначению штамповочных уклонов и напусков металла на поверхностях поковки, перпендикулярных к этой плоскости, выбору допусков на размеры и переходных радиусов закруглений по необрабатываемым элементам детали согласно требованиям ГОСТа 7505 - 55. Штамповочные уклоны (5 - 7°, рис. IV.26,б) несколько раскрывают ручьи (полости) в сторону плоскости разъема, что облегчает удаление поковки из штампа. Переходные радиусы закруглений (R4 - R10 мм) позволяют обеспечить лучшее течение металла в штампе и способствуют повышению прочности и стойкости штампов.
При штамповке в ковочных штампах на молотах и прессах невозможно получение сквозных отверстий в поковках. Поэтому их заменяют встречными выемками - наметками в (см. рис. IV. 26,б), между которыми остается нетолстая пленка и, удаляемая проколкой при обрезке облоя после штамповки.
Конструктор должен знать и о том, что благоприятное для прочности и износоустойчивости детали расположение волокон металла в ней (макроструктура) обеспечивается тем или иным методом деформирования заготовки в процессе штамповки. Направление волокнистости должно соответствовать направлению приложения наибольших эксплуатационных нагрузок детали.
§ 22. Технология штамповки на молотах
Штамповочные молоты. Для штамповки разнообразных поковок из стали массой 0,1 - 300 кг применяют паровоздушные штамповочные молоты с массой падающих частей 0,5 - 25 т, фрикционные молоты 0,5 - 2 т и бесшаботные молоты с энергией удара до 100 000 кГ.м (981 кДж).
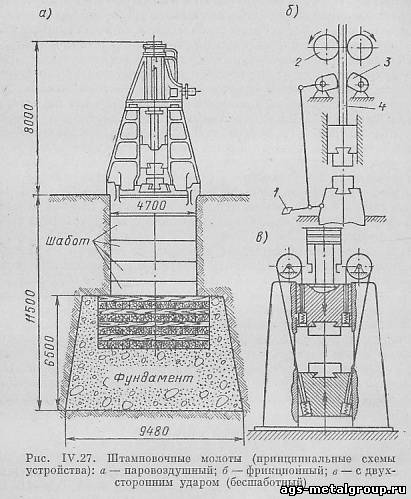
Паровоздушный штамповочный молот двойного действия (рис. IV.27,а) отличается от ковочного удлиненными регулируемыми направляющими бабы, обеспечивающими точное совмещение верхнего и нижнего штампов при ударе; креплением стоек молота непосредственно на шаботе, а не на отдельном фундаменте; утяжеленным шаботом, что повышает к. п. д. удара молота и точность штамповки. Молот имеет педальное управление вместо ручного, что обеспечивает возможность управления молотом самим кузнецом - штамповщиком. Молот снабжен толстым штоком вместо нормального. Такие штоки не ломаются от усталости металла и обеспечивают большую жесткость удара штампов.
У фрикционного молота простого действия (рис. IV. 27,б) баба молота с верхним штампом, двигающаяся в направляющих, прикреплена к доске, которая проходит между двумя вращающимися от электродвигателя чугунными валками 2. Когда один из валков, ось которого снабжена эксцентриком, прижимается к доске посредством вертикальной тяги, то она силами трения поднимается вверх вместе с бабой. После разжима валков баба с доской и штампом начинает падать, но задерживается тормозными самозаклинивающимися кулачками 3. Штамповщик, нажимая на педаль 1, разжимает кулачки, и при падении штампа с бабой осуществляется штамповка. Затем ролики снова поднимают бабу и удары продолжают следовать один за другим, пока не будет отпущена педаль.
Массу падающих частей молота, необходимую для штамповки данной поковки, можно приближенно определить умножением суммарной площади горизонтальной проекции поковки с облоем (в см²) на условный удельный тоннаж молота. Его значение практически принимают 4 кГ/см² для паровоздушных молотов двойного действия и 6 кГ/см² для молотов простого действия.
Бесшаботные молоты (рис. IV.27,в) имеют две соударяющиеся бабы, а шабот у них отсутствует. Энергия удара здесь почти целиком расходуется на деформацию поковки и взаимно поглощается бабами, не передаваясь на фундамент. Верхняя баба является ведущей, она приводится в движение давлением пара или воздуха, поступающего в цилиндр молота через золотниковое устройство. Нижняя баба получает рабочее движение от верхней посредством стальных лент, перекинутых через шкивы.
Мощность бесшаботного молота, выражаемая эффективной энергией удара Lэ = 80 000 кГ·м (785 кДж), примерно эквивалентна мощности обычного штамповочного молота двойного действия с массой падающих частей 40 т. Применяют такие молоты для штамповки крупных поковок, массой до 3600 кг.
Способы штамповки на молотах. В зависимости от характера производства (мелкосерийное, серийное или массовое) применяют следующие основные способы штамповки на молотах: в подкладных штампах, в одноручьевых штампах закрепленного типа, в многоручьевых штампах закрепленного типа.
Штамповка в подкладных штампах применяется в условиях мелкосерийного производства поковок, когда размер партии единовременно изготовляемых деталей составляет не менее 20 - 40 шт. Этим способом штампуются обычно мелкие детали массой до 3 - 5 кг.
Штампы выполняют облегченного типа и при штамповке подкладывают между плоскими бойками ковочного молота. Штамп, изображенный на рис. IV,28,б состоит из нижней 1 и верхней 4 частей, в которых сделаны ручьи 2 по форме изготовляемой поковки (шатуна). Для обеспечения совпадения половин штампа при их наложении в нижней части запрессованы направляющие шпильки 3, которые при штамповке входят в отверстия 5 верхней части. Штампы снабжены рукоятками 6.
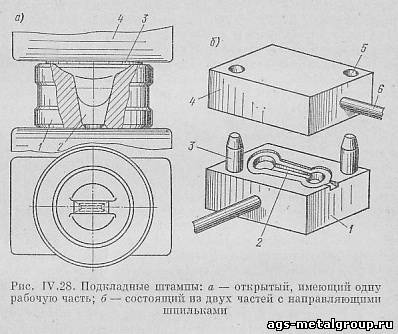
Для деталей круглых в плане, с выступами и ступицами штампы обычно делают из одной нижней части, в этом случае роль верхней части штампа выполняет верхний боек молота (рис. IV.28,а).
Штамповка производится, как правило, с одного нагрева из мерной прокатанной заготовки, причем в случае штамповки сложных по форме деталей заготовку предварительно куют под молотом, сообщая ей форму, близкую к форме ручья штампа.
При штамповке поковки обуха в открытом штампе, состоящем из корпуса 1 и вкладыша 2 (рис. IV. 28, а), кузнец устанавливает расплющенную на конце цилиндрическую заготовку вертикально в ручей штампа и осаживает ее серией ударов верхнего бойка 4 молота. Незначительный по объему облой 3 при этом вытесняется между торцевой поверхностью штампа и лицевой поверхностью верхнего бойка. В процессе штамповки подручный кузнеца удерживает штамп на нижнем бойке циркульными клещами, охватывающими заточку штампа, а по окончании штамповки поворачивает штамп на ребро, после чего поковка выбивается ударом ручника по вкладышу 2. Затем штамп охлаждают в воде и процесс штамповки повторяется.
При изготовлении поковки со сквозным отверстием производится прошивка его на прошивном кольце конусным прошивнем, с последующей калибровкой поковки в том же штампе. После штамповки торцевой облой обычно не обрезается, а удаляется вместе с припуском при последующей обработке поковок на токарном станке.
Технологический процесс изготовления поковок в подкладном штампе с направляющими шпильками (рис. IV.28, б) состоит из предварительной ковки нагретых до 1200' С мерных заготовок, штамповки их с того же нагрева за 4 - 5 ударов молота и обрезки облоя обрезным штампом на кривошипном прессе (рис. IV.29).
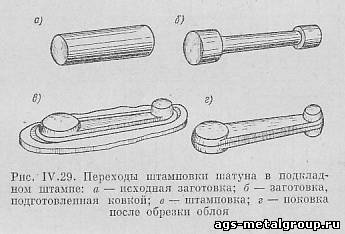
Штамповка в одноручьевых штампах закрепленного типа применяется в условиях крупносерийного и массового производства в основном для деталей, имеющих форму тел вращения: шестерен, фланцев, горловин, т. е. в тех случаях, когда штамповка может производиться без предварительной ковки, непосредственно из мерной заготовки круглого профиля, или из заготовки, осаженной на угловой площадке штампа.
Штампы применяются как открытого типа, с образованием облоя, так и безоблойные (см. рис. IV.25). Штампы изготовляются массивными (весом в 100 - 300 кг и более) из кованых кубиков легированной штамповой стали марок 5ХНМ, 5ХНТ, 5ХГМ и др., которые затем обрабатываются на металлорежущих станках. Рабочие части штампа подвергаются закалке и отпуску до твердости HRC38 - 44.
Штамповка в многоручьевых закрепленных штампах применяется для изготовления деталей сложной формы с переменными сечениями по длине: шатунов, коленчатых валов, изогнутых рычагов, крестовин и т. п., в условиях крупносерийного и массового производства.
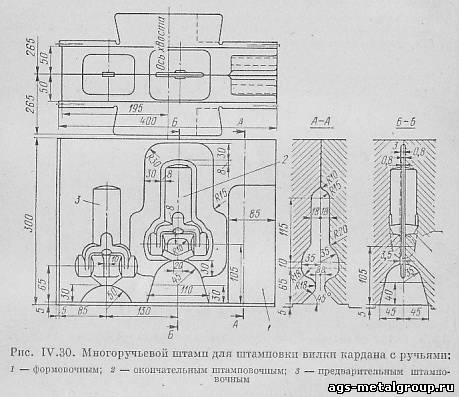
Штампы этого типа (рис. IV.З0) выполняются с несколькими ручьями. Одна группа ручьев - заготовительных - служит для предварительного формообразования заготовки, другая группа- штамповочных - для предварительной и окончательной штамповки.
Мерная заготовка из проката сначала последовательно обрабатывается в заготовительных ручьях, в которых ей придается форма, близкая к очертаниям штамповочного ручья, а затем с того же нагрева штампуется в предварительном и окончательном штамповочном ручьях. Перекладка заготовки из ручья в ручей производится штамповщиком вручную, клещами. Тяжелые заготовки перекладываются клещами, подвешенными к тельферу или роликовой тележке, перекатываемой по монорельсу, или специальными манипуляторами.
К заготовительным ручьям (рис. IV.31), служащим главным образом для предварительного перераспределения металла заготовки вдоль ее оси, относятся протяжной, подкатной, пережимной, формовочный, гибочный, а также площадка для осаживания и расплющивания заготовки.
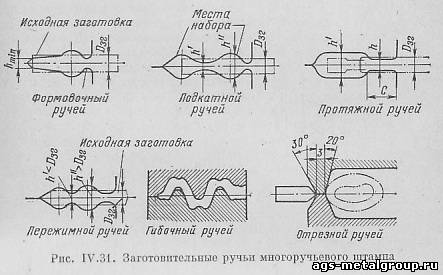
Протяжной ручей уменьшает поперечное сечение исходной заготовки и увеличивает ее длину. В процессе вытяжки заготовка после каждого удара кантуется и подается вперед.
Подкатной ручей служит для точного распределения металла по длине заготовки за счет уменьшения ее поперечных сечений на одних участках и увеличения их (набора металла) на других участках. По заготовке наносят два - четыре удара, сопровождаемых каждый раз кантовкой ее на 90'. Из подкатного ручья заготовку перекладывают в предварительный штамповочный ручей, а иногда в гибочный или формовочный.
Пережимной ручей выполняет пережим и расплющивание заготовки за 1 - 2 удара молота, после чего заготовка плашмя переносится в штамповочный ручей.
Формовочный ручей деформирует заготовку за один удар в вертикальной плоскости, придавая ей форму, соответствующую очертаниям поковки в плоскости разъема.
Гибочный ручей изгибает заготовку за один-два удара.
К штамповочным ручьям относятся предварительный и окончательный ручьи.
Предварительный ручей (рис. IV.З0, 3) служит для получения формы поковки, близкой к конечной, и для снижения износа окончательного ручья, от которого он отличается большими штамповочными уклонами и радиусами закруглений, а также отсутствием канавки для облоя.
Окончательный ручей (рис. IV.З0, 2) служит для получения окончательных формы и рельефа поковки. В нем по поковке наносят один или несколько ударов возрастающей силы до момента соударения опорных плоскостей штампов, различимого на слух по звонкому удару.
Отрезной ручей (рис. IV.31) служит для отделения оштампованной поковки с облоем от прутка в том случае, если из исходной заготовки штампуется последовательно несколько небольших поковок за один нагрев. Поковка укладывается перешейком на нож нижнего штампа и одним ударом отсекается от прутка.
Технологический процесс горячей штамповки в многоручьевом штампе состоит из следующих операций: резки сортового проката на мерные заготовки на пресс-ножницах; нагрева заготовок в методической или камерной печи до 1100 - 1200' С; штамповки заготовки последовательно в ручьях штампа на молоте при температуре 1200 - 900' С; обрезки облоя (и проколки пленки) на кривошипном прессе при 900 - 800' С (или в холодном состоянии); термообработки поковок (нормализации или отжига); очистки поковок от окалины и холодной калибровки их на чеканочном прессе в случае необходимости.