ОСНОВНЫЕ СВЕДЕНИЯ О ПРОЦЕССЕ РЕЗАНИЯ МЕТАЛЛОВ
§ 1. Методы обработки металлов резанием
Подавляющее число деталей машин приобретают форму и размеры только после механической обработки - обработки металлов резанием. До обработки будущая деталь называется заготовкой. Чтобы получить необходимую деталь, с заготовки нужно снять часть металла, называемую припуском. Процесс снятия припуска режущим инструментом с целью получения детали заданной формы, размеров и точности называется резанием.
Для осуществления процесса резания заготовке и инструменту необходимо сообщить определенный комплекс движений. Эти движения можно разделить на основные (для осуществления процесса резания) и вспомогательные (для подготовки к процессу резания и завершения операции). Основных движения два: главное движение - движение резания и движение подачи.
Главное движение непосредственно позволяет осуществлять процесс резания (образования стружки), движение подачи дает возможность вести процесс снятия стружки со всей обрабатываемой поверхности.
В зависимости от характера выполняемых работ и вида режущего инструмента различают следующие методы обработки металлов резанием: точение, сверление, шлифование, фрезерование, строгание, протягивание и др. На рис. 1 приведены схемы различных методов обработки металлов резанием.
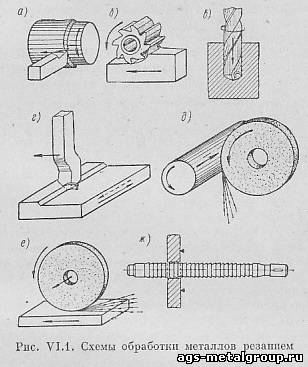
При точении заготовке сообщается вращательное главное движение, а инструменту движение подачи (рис. 1, а).
При фрезеровании главное (вращательное) движение сообщается инструменту (фрезе), а движение подачи - заготовке (рис. 1, б).
При сверлении как главное (вращательное) движение, так и движение подачи обычно сообщается инструменту (рис. 1, в).
При строгании на продольно-строгальных станках главное (возвратно-поступательное) движение сообщается заготовке, а движение подачи - инструменту (рис. 1, г).
При строгании на поперечно-строгальных станках и при обработке на долбежных станках главное движение сообщается инструменту, а движение подачи - заготовке.
При шлифовании главное движение всегда вращательное, оно осуществляется инструментом (шлифовальным кругом). При круглом шлифовании (рис. 1, д) одновременно вращается и заготовка, чем обеспечивается круговая подача. Так как в большинстве случаев длина шлифуемой детали больше ширины круга, оказывается необходимой еще и продольная подача (вдоль оси заготовки), которая осуществляется заготовкой или кругом. Применяется также радиальная подача, обеспечивающая постепенное снятие припуска на всю глубину.
При плоском шлифовании продольная подача осуществляется чаще всего заготовкой, а поперечная подача - шлифовальным кругом или заготовкой. (рис. 1, е).
При протягивании главное движение прямолинейное и сообщается инструменту (протяжке), а постепенное снятие стружки (подача) обеспечивается разностью высот каждых двух смежных зубьев протяжки (рис. 1, ж).
§ 2. Геометрия резцов
Схема обработки детали точением и взаимное расположение обрабатываемой детали и инструмента приведены на рис. 2, а. На детали в процессе резания различают обрабатываемую и обработанную поверхности и поверхность резания.
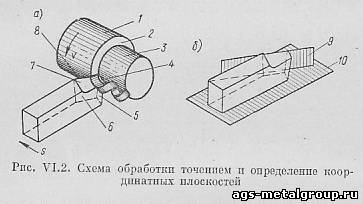
Обрабатываемая поверхность 1 - это поверхность заготовки на том ее участке, который предстоит обработать на данной операции; обработанная поверхность 3 - поверхность, получающаяся после отделения срезаемого слоя, т. е. после обработки; поверхность резания 2 - поверхность, образуемая на обрабатываемой детали, режущей кромкой резца.
Принцип работы любого режущего инструмента основан на действии клина. Рабочую часть резца, осуществляющую резание, ограничивают: передняя поверхность 7, по которой сходит образующаяся в процессе резания стружка; главная задняя поверхность 6 резца, обращенная к поверхности резания; вспомогательная задняя поверхность 5 - поверхность резца, обращенная к обработанной поверхности детали.
Главная режущая кромка 8 образуется пересечением передней и главной задней поверхностей. Вспомогательная режущая кромка 4 образуется пересечением передней и вспомогательной задней поверхностей. Точка пересечения главной и вспомогательной режущих кромок называется вершиной резца.
Взаимное расположение поверхностей резца, а также их расположение относительно обрабатываемой детали определяются группой углов. Для определения углов, характеризующих геометрию резца, вводится понятие о координатных плоскостях: плоскости резания и основной плоскости (рис. 2, б).
Плоскость резания 9 касательная к поверхности резания и проходит через главную режущую кромку. Основная плоскость 10 параллельна направлениям продольной и поперечной подач. У резцов с призматическим телом эта плоскость совпадает с нижней опорной поверхностью резца.
Углы резца измеряются в главной секущей плоскости, перпендикулярной к проекции главной режущей кромки на основную плоскость (рис. 3, а). Главным задним углом α называется угол, образованный главной задней поверхностью инструмента и плоскостью резания. Этот угол необходим для уменьшения трения между обрабатываемой деталью и резцом. Практически угол α принимается в пределах 6 - 12˚.
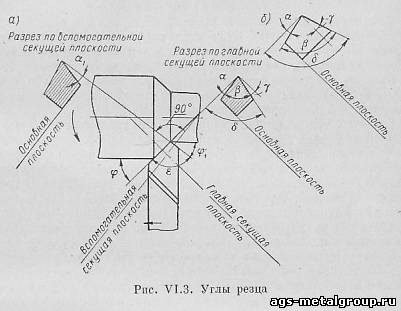
Передним углом γ называется угол между передней поверхностью и нормалью к плоскости резания. Величина переднего угла оказывает существенное влияние на процесс стружкообразования. Величина угла γ колеблется в широких пределах - от +25 до - 10˚.
Угол заострения β - это угол между передней и главной задней поверхностями. Чем он больше, тем прочнее режущая часть инструмента и тем лучше условия отвода тепла от режущего лезвия.
Углом резания δ называется угол между передней поверхностью и плоскостью резания.
Из рис. 3 очевидно, что α + β + γ = 90˚; δ = α + β = 90˚ - γ.
Если угол δ < 90 (рис. 3, а), то угол γ имеет положительное значение. При δ > 90' (рис. 3, б) угол γ приобретает отрицательное значение.
При положительном значении γ облегчаются условия схода стружки, но зато уменьшается прочность режущего клина, ухудшаются условия отвода тепла от режущего клина. Кроме того, действие силы резания, направленное по нормали к передней поверхности, вызывает в режущем клине деформации изгиба и среза.
При отрицательном значении угла γ прочность клина повышается, улучшаются условия отвода тепла, а силы резания вызывают только деформации сжатия, которые хорошо выдерживаются как инструментами из стали, так и из твердых сплавов. Однако в этом случае условия схода стружки значительно ухудшаются, а следовательно, увеличивается мощность, затрачиваемая на резание.
Вспомогательный задний угол α₁ измеряется в вспомогательной секущей плоскости. Этот угол необходим для уменьшения трения по вспомогательной задней поверхности и принимается в большинстве случаев равным главному заднему углу α.
Важное значение в процессе резания имеют углы в плане. Различают главный и вспомогательный углы в плане. Углы в плане измеряются в основной плоскости (рис. 3, а).
Главным углом в плане φ называется угол между проекцией главной режущей кромки на основную плоскость и направлением продольной подачи. В зависимости от условий обработки угол φ принимается равным от 10 до 90˚. Наиболее часто употребляются резцы с углом в плане φ = 45˚. Чем меньше главный угол в плане, тем более чистой получается поверхность. Но с уменьшением угла φ увеличивается отжим резца от заготовки, снижается точность обработки и могут возникнуть вибрации, при которых работать практически невозможно.
Вспомогательный угол в плане φ₁ - угол между проекцией вспомогательной режущей кромки на основную плоскость и образующей обработанной поверхности. Вспомогательный угол в плане оказывает большое влияние на чистоту обработанной поверхности и в зависимости от условий обработки выбирается от 0 до 30˚.
Режущий инструмент с углом φ₁ = 0 позволяет получить малую шероховатость при больших подачах (до 3 - 5 мм/об).
Углом при вершине ε называется угол между проекциями главной и вспомогательной режущих кромок на основную плоскость. Чем больше этот угол, тем лучше условия отвода тепла от режущих кромок, тем больше стойкость резца.
Угол между главной режущей кромкой и плоскостью, проведенной параллельно основной плоскости через вершину резца, называется углом наклона главной режущей кромки λ (рис. 4). Он считается положительным, если вершина резца является наинизшей точкой режущей кромки (рис. 4, а), и отрицательным, когда вершина резца является наивысшей точкой кромки (рис. 4, б). Угол λ равен нулю, если главная режущая кромка параллельна основной плоскости (рис. 4, в).
Угол λ влияет на массивность головки резца и направление схода стружки.
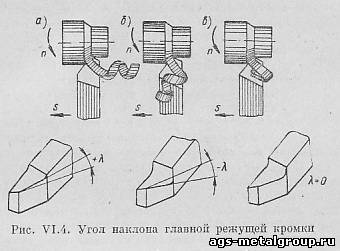
При нулевом или положительном значении угла λ стружка сходит в направлении, обратном подаче, при этом она будет наматываться на заготовку и царапать обработанную поверхность. Но положительное значение угла λ делает головку резца массивнее и более стойкой, а потому при обдирочных работах, когда не предъявляется высоких требований к качеству обработанной поверхности, рекомендуется положительное значение угла λ (до +5˚).
У резцов с отрицательным значением угла λ направление схода стружки обратное, т. е. от обработанной поверхности к обрабатываемой, но при этом ослабляется головка резца. Поэтому резцы с отрицательными углами λ применяются при чистовой обработке.
§ 3. Элементы резания при точении
К элементам резания при точении относятся: скорость резания, глубина резания и подача.
Скоростью резания υ называется величина перемещения поверхности резания относительно режущей кромки в единицу времени в процессе осуществления главного движения.
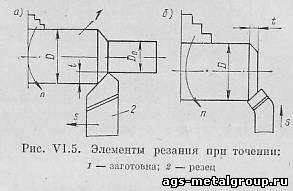
При токарной обработке, когда обрабатываемая заготовка диаметром D (рис. 5, а) вращается с некоторым числом оборотов n в минуту, скорость резания будет изменяться по длине режущей кромки. Однако в расчетах скорости резания принимается ее максимальное значение, определяемое по формуле
где D - наибольший диаметр поверхности резания в мм.
При токарной обработке различают продольное точение, когда резец перемещается в направлении, параллельном оси заготовки (рис, 5, а), и поперечное точение (рис. 5, б), когда резец перемещается в направлении, перпендикулярном оси вращения заготовки.
В случае поперечного точения, когда резец перемещается от периферии к центру или, наоборот, от центра к периферии, скорость резания при постоянном числе оборотов переменна. Она имеет наибольшее значение у периферии и равна нулю в центре. Однако и в этом случае в расчет принимается максимальная скорость резания, соответствующая диаметру D.
Величина подачи s при точении определяется перемещением инструмента за один оборот заготовки. В ряде случаев бывает необходимо знать величину минутной подачи sм.
Между подачей s (в мм/об) и минутной подачей sm (в мм/мин) существует следующая зависимость: sm = sn мм/мин, где n - число оборотов заготовки в минуту.
Глубина резания t - величина срезаемого слоя за один проход, измеренная в направлении, перпендикулярном к обработанной поверхности (рис. 5, а). Глубина резания при продольном точении представляет собой полуразность между диаметром заготовки и диаметром обработанной поверхности, полученной после одного прохода, 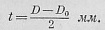
При поперечном точении за глубину резания принимается величина срезаемого слоя (рис. 5, б), измеренная в осевом направлении (перпендикулярно к обработанной поверхности). С изменением подачи или глубины резания изменяется поперечное сечение стружки. На рис. 6 показано поперечное сечение стружки при продольном точении.
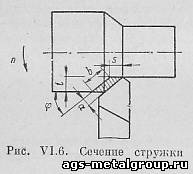
Шириной среза b называется расстояние между обрабатываемой и обработанной поверхностями, измеренное по поверхности резания. Толщина среза α - расстояние между двумя последовательными положениями поверхности резания, полученное после одного оборота обрабатываемой детали.
При γ = 0, α = s sin φ, b = t/sin φ, где φ - главный угол в плане.
Площадь поперечного сечения среза f = αb = ts мм².
§ 4. Процесс образования стружки
Основоположниками науки о резании металлов являются русские ученые И; А. Тиме, К. А. Зворыкин и Я. Г. Усачев. И. А. Тиме показал, что процесс образования стружки происходит по элементам (рис. 7, а).
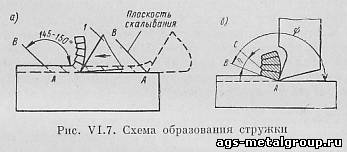
Резец 1 при своем движении деформирует находящийся перед ним металл; при этом в срезаемом слое металла создается определенное напряженное состояние. Когда напряжение превышает силу внутреннего сцепления частиц металла, происходит сдвиг элемента стружки. При дальнейшем движении резца таким же образом отделяются второй и последующие элементы стружки.
Плоскость АВ, по которой происходит скалывание отдельных элементов стружки, принято называть плоскостью скалывания, а угол ψ между плоскостью скалывания и направлением движения резца - углом скалывания. Угол скалывания для мягких металлов независимо от величины угла резания δ составляет 145 - 150˚.
В процессе резания перемещение (деформация) металла происходит в срезаемом слое не только по плоскости скалывания АВ, но и по так называемой плоскости сдвига АС в пределах каждого элемента стружки. Угол между плоскостью сдвига АС и плоскостью скалывания АВ называется углом сдвига η (рис. 7, б).
Основная деформация при резании пластических металлов происходит по плоскостям сдвига, так как кристаллы металла оказываются вытянутыми вдоль этих плоскостей. Благодаря этому прочность металла в стружке меньше по плоскостям сдвига, чем по плоскостям скалывания. Это подтверждается тем, что стружка при ее перегибе разламывается не по плоскостям скалывания, а по плоскости сдвига.
В зависимости от условий обработки стружка может быть различных видов (рис. 8): сливной, стружкой скалывания, надлома.
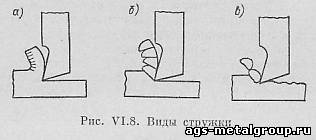
Вязкие металлы (мягкая сталь, медь, алюминий и т. д.) образуют сливные стружки, имеющие вид сплошной прямой ленты, плоской или винтовой спирали. Отдельные элементы этой стружки довольно прочно связаны друг с другом (рис. 8, а).
При обработке менее вязких металлов (сталей повышенной твердости, некоторых марок латуни и т. п.) образуется стружка скалывания (рис. 8, б). У нее отчетливо видны плоскости скалывания между отдельными элементами, а верхняя сторона имеет пилообразную форму. Элементы этой стружки имеют менее прочную связь, поэтому стружка после образования нескольких завитков обычно отламывается под действием собственного веса.
Стружка надлома (рис. 8, в) получается при обработке хрупких металлов (чугун, бронза) и неметаллических материалов. Связь между отдельными элементами стружки настолько слаба, что эти элементы представляют собой совокупность частиц неправильной формы.
Вид образующейся стружки зависит не только от свойств обрабатываемого металла, но также и от скорости резания, геометрии резца и ряда других факторов.
§ 5. Тепловые явления при резании металлов
В процессе резания металлов выделяется тепло. Основным источником образования теплоты при резании является работа, затраченная на деформацию срезаемого слоя, трение стружки о переднюю поверхность инструмента и трение задней поверхности резца о поверхность резания. Исследованиями установлено что больше всего выделяется теплоты в результате деформации срезаемого слоя.
Установлено, что в среднем при токарной обработке 50- 86% всей выделяющейся теплоты уходит в стружку, 40 - 10%- в резец, 9 - 3% - в обрабатываемую заготовку и около 1% - в окружающую среду. При увеличении скорости резания количество остающейся в стружке теплоты значительно увеличивается, а поступление ее в резец и обрабатываемую деталь соответственно уменьшается. При скоростях резания около 100 м/мин [1,5 м/с] в стружке остается около 80% теплоты, а при скоростях порядка 500 м/мин [8 м/с] стружкой уносится 97 - 99% и только 1 - 3% теплоты поступает в резец, обрабатываемую деталь и окружающий воздух.
Больше всего на температуру в зоне резания влияет скорость резания. Поэтому при больших скоростях резания, хотя доля поступления теплоты в инструмент и уменьшается, общее количество ее настолько велико, что по сравнению с нормальными скоростями резания в значительной степени повышаются как температура стружки, так и температура резца.
На температуру резания оказывают также влияние подача, глубина резания, геометрия режущей части резца и его размеры.
§ 6. Износ и стойкость резцов
Под влиянием высокой температуры, развивающейся в процессе резания и вызывающей потерю режущей частью резца необходимой твердости, а также вследствие механического истирания граней режущего клина сходящей стружкой и поверхностью резания резец изнашивается, затупляется.
При точении наблюдается износ режущего инструмента как по его передней, так и по задней поверхностям. На износ резца большое влияние оказывают материал обрабатываемой детали, режимы резания, геометрия инструмента и качество заточки резца.
Наибольшее количество режущих инструментов изнашивается в основном по задним поверхностям. В результате износа задней поверхности около режущей кромки образуется площадка (рис. 9, а). Шириной h₃ этой площадки характеризуется степень износа задней поверхности.
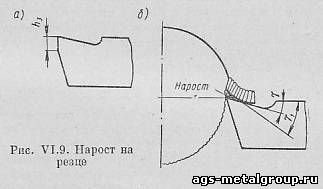
Расход режущего инструмента и качество обработки в большой степени зависят от затупления инструмента. При достижении определенной величины износа увеличиваются силы резания, повышается температура резания, ухудшается чистота обработанной поверхности, снижается точность обработки.
Существует несколько критериев износа резцов. В производственных условиях за критерий затупления принимается соответствующая величина износа.
Для токарных резцов с пластинками твердых сплавов рекомендуются следующие допустимые значения h₃ (в мм)
При черновой обработке сталей........ 1,0 - 1,4
» » » чугуна ...... 0,8 - 1
При чистовой обработке сталей ........ 0,4 - 0,6
» » » чугуна ...... 0,6 - 0,8
Для отрезных резцов с пластинками твердых сплавов h₃ = 0,8 ÷ 1 мм. Для резцов с керамическими пластинками допустимая величина износа h₃ = 0,6 ÷ 0,8 мм.
С понятием об износе инструмента неразрывно связано понятие о его стойкости. Стойкостью резца называется тот период времени, в течение которого его износ при непрерывной работе доходит до установленной величины, т. е. критерия затупления. Стойкость измеряется в минутах и обозначается буквой Т. Она зависит от таких же факторов, как износ. Наибольшее влияние на износ и, следовательно, на стойкость резца оказывает скорость резания. Обычно режимы резания выбираются таками, чтобы стойкость резца Т была в пределах 30 - 60 мин.
Явления тепловыделения и износа инструмента присущи любому виду обработки металлов (точению, фрезерованию, сверлению и т. д.). Закономерности этих явлений легли в основу при назначении режимов резания.