§ 7. Охлаждение и смазка при резании металлов
В целях уменьшения трения и охлаждения инструмента и обрабатываемой детали весьма широко применяют охлаждающе-смазывающие жидкости.
В практике обработки металлов резанием наиболее употребительны охлаждающе-смазывающие жидкости: эмульсии, компаундированные масла, сульфофрезолы, минеральные и растительные масла, раствор соды в воде, скипидар и керосин.
Помимо охлаждающей способности, применяемая при резании жидкость должна обладать высокой смазывающей способностью, хорошо проникать между трущимися поверхностями, легко вступать в реакцию с обрабатываемым материалом и создавать предохранительную пленку.
Эффективность применения охлаждения зависит от физико-механических свойств обрабатываемого материала, смазочно-охлаждающей жидкости, интенсивности охлаждения (количество подводимой жидкости в минуту) и от способа ее подвода к зоне резания.
При обильном охлаждении с интенсивностью 8 - 12 л/мин [0,13 - 0,2 л/с] при точении стали резцами из быстрорежущей стали допускается повышение скорости резания на 20 - 25%, при точении чугуна на 12 - 15% (при обработке чугуна на износ резца влияет главным образом механическое истирание, а не высокая температура резания). Эффективность охлаждения зависит не только от состава и свойств жидкости, но и от способа ее подвода к зоне резания.
В настоящее время применяются следующие способы охлаждения: свободно падающей струей, высоконапорное охлаждение, охлаждение воздушной эмульсией и распыленной жидкостью.
Охлаждение свободно падающей жидкостью - наиболее распространенный способ охлаждения. Жидкость насосом подается на стружку в месте ее отделения от детали (при точении) или же на вращающийся инструмент (при фрезеровании); попадая в зону резания она охлаждает стружку, инструмент и обрабатываемую деталь и понижает температуру в зоне резания на 50 - 100' С. Стойкость инструмента в зависимости от материала детали и скорости резания повышается в 2 - 4 раза.
Из-за малой скорости подачи жидкости (0,2 - 1,5 л/сек) интенсивность охлаждения при этом способе сравнительно небольшая, однако ввиду простоты он имеет самое широкое распространение.
Высоконапорное охлаждение находит применение при обработке труднообрабатываемых сталей. Смазочно-охлаждающая жидкость под большим давлением (15 - 20 ат) [(1,5 - 2,0) х 10⁶ Па] подводится к режущей кромке резца снизу со стороны его задней поверхности, через узкую щель шланга. При высоконапорном охлаждении наблюдается значительное повышение стойкости резца по сравнению с обычным методом охлаждения.
Охлаждение воздушной эмульсией и распыленной жидкостью (эмульсией или маслом) в виде тумана характеризуется малым расходом эмульсии и чистотой рабочего места. Жидкость направляется к режущей кромке со стороны задней поверхности резца под большим давлением.
§ 8. Образование нароста на резцах
Так как стружка оказывает на переднюю поверхность резца очень большое давление, между ними возникают большие силы сцепления при обработке некоторых металлов. В результате происходит как бы слипание (сваривание) двух металлов: нижних частиц стружки с передней гранью резца. Слипание, а также сопротивление неровностей передней поверхности резца движению стружки, создают силу трения, которая препятствует ее сходу. Когда эта сила становится больше сил сцепления между частицами металла стружки, нижние слои стружки как наиболее спрессованные в процессе резания отделяются от остальной части стружки и задерживаются, или, как говорят, застаиваются на передней поверхности резца. Постепенно наслаиваясь друг на друга, они образуют между стружкой и передней гранью резца неподвижный, плотный, сильно спресованный слой, который называется наростом (рис. 9, б). Нарост имеет клиновидную форму. Твердость нароста в 2 - 3 раза больше твердости обрабатываемого металла, и он сам может срезать слой металла. Являясь как бы продолжением режущего клина резца, нарост изменяет его передний угол (γ₁ с учетом нароста больше γ, полученного при заточке), а следовательно, оказывает влияние на процесс деформации срезаемого слоя, износ резца и силы, действующие на резец, а также на качество обработанной поверхности.
Нарост защищает режущую кромку от истирающего действия со стороны сходящей стружки и со стороны обработанной поверхности и до известной степени предохраняет ее от воздействия теплоты, возникающей при резании.
При грубой (черновой) обработке нарост не оказывает вредного влияния на процесс резания. Когда необходимо получить высокое качество обработанной поверхности, нарост нежелателен. Изменение размеров нароста приводит к большой шероховатости (ухудшению чистоты, обработанной поверхности) и к изменению размера обработанной поверхности по диаметру.
Образование нароста зависит от режима резания, геометрии резца и условий работы. Наибольшее влияние на образование нароста оказывает скорость резания υ. При скоростях резания около 80 м/мин [1,3 м/с] и более нарост не образуется и обработанная поверхность получается с наименьшей шероховатостью. Тот же результат получается при очень низких скоростях резания порядка 1 - 2 м/мин [0,016 - 0,034 м/с] и меньше, при которых нарост также не образуется.
Наиболее интенсивно нарост образуется при работе со скоростями резания в диапазоне 10 - 20 м/мин [0,16 - 0,34 м/с].
Прерывистое резание (например, при строгании, фрезеровании и т. п.) сопровождается резко переменной (ударной) нагрузкой на инструмент. Поэтому нарост в этом случае не образуется. Не обнаруживается нарост также при обработке чугунов и других материалов, при резании которых образуется стружка надлома и как следствие создается пульсирующе-ударная нагрузка на режущую кромку.
§ 9. Силы резания и мощность при точении
При срезании стружки обрабатываемый металл оказывает сопротивление резанию Р, преодолеваемое резцом (рис. 10, а). При токарной обработке эту силу удобно рассматривать как равнодействующую трех взаимно перпендикулярных составляющих (рис. 10, б).
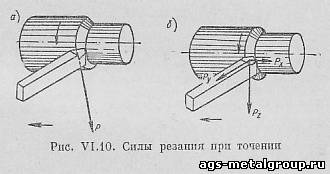
Сила резания Pz направлена вертикально и совпадает с направлением главного движения. Эта сила стремится отжать резец вниз. По ней рассчитывается эффективная мощность резания.
Сила подачи Px расположена в горизонтальной плоскости и направлена в сторону, противоположную продольной подаче. По ней рассчитывается механизм подачи станка.
Радиальная сила Py расположена тоже в горизонтальной плоскости, но направлена перпендикулярно к оси обрабатываемой детали и воздействует на ее прогиб. При обработке длинных деталей малого диаметра влияние этой силы можно снизить за счет увеличения главного угла в плане.
Все эти силы измеряются в килограммах [ньютонах] и определяются с помощью специальных динамометров. Исследования показывают, что сила Px составляет 10 - 25% силы Pz, а сила Py - З0 - 50% силы Pz.
Сила резания Pf, приходящаяся на 1 мм² площади поперечного сечения стружки f, называется удельным давлением резания. Pf = Pz/f кГ/мм².
Величина удельного давления зависит от обрабатываемого материала, глубины резания и других факторов.
Удельное давление резания для данного металла, полученное при определенных условиях: глубине резания t = 5 мм, подаче s = 1 мм/об, угле резания δ = 75˚, φ = 45˚ и λ = 0 при резании всухую, называется коэффициентом резания k.
Если коэффициент резания k известен, то сила резания может быть приближенно определена по формуле Pz = kf.
Точнее сила резания определяется по эмпирической формуле
где Ср - коэффициент, зависящий от механических свойств обрабатываемого металла; t - глубина резания в мм; s - подача в мм/об.
Значений Ср и показателей степеней xp и yp приводятся в нормативных материалах Научно-исследовательского бюро технических нормативов (НИБТН).
Крутящий момент на шпинделе определяется по формуле
где D - диаметр обрабатываемой детали в мм, а эффективная мощность по формуле
где υ - скорость резания в м/мин[м/с].
Зная коэффициент полезного действия станка η (к. п. д.), можно определить мощность электродвигателя привода главного движения:

§ 10. Скорость резания и влияние на нее различных факторов
Для изготовления одной детали на станке требуется определенная затрата времени. Это время называется штучным Тшт; оно складывается из суммы отдельных времен (в мин) Тшт = То + Тв + Тоб + Тот, где То - основное технологическое время (машинное время); Тв - вспомогательное время (на установку, крепление и съем детали, на управление станком, холостые перемещения режущего инструмента, контроль детали); Тоб - время на обслуживание рабочего места и станка (смазка станка, уборка стружки и т. п.); Тот - время перерывов на отдых и естественные надобности.
Основное технологическое время То - это время, затрачиваемое непосредственно на процесс резания. Основное технологическое время при обточке определяется по формуле
где L - расчетная длина обработки (складывается из длины обрабатываемой поверхности, пути врезания и перебега резца); s - подача резца в мм/об; n - число оборотов шпинделя в минуту; i - число проходов.
Как видно из формулы, увеличение числа оборотов заготовки (или, что то же самое, скорости резания) приводит к уменьшению машинного времени То.
Однако скорость резания нельзя назначать без учета конкретных условий обработки, так как при увеличении скорости резко возрастает интенсивность износа инструмента, т. е. снижается его стойкость - время работы от переточки до переточки. Чем большую скорость резания допускает инструмент при одной и той же стойкости, тем выше его режущие свойства, тем он более производителен.
Допускаемая скорость резания зависит от следующих факторов: механических свойств обрабатываемого материала; материала режущей части резца; стойкости режущего инструмента (фактическое время работы инструмента от переточки до переточки); подачи и глубины резания геометрических элементов режущей части резца; вида обработки (точение, растачивание, подрезание и т. д.); охлаждения.
Обрабатываемый материал. Наибольшее влияние на величину скорости резания оказывают предел прочности при растяжении σв и твердость НВ материала.
Способность металлов поддаваться резанию принято называть обрабатываемостью. Основной характеристикой обрабатываемости является скорость резания, с которой можно обрабатывать металл при определенной стойкости инструмента. Испытуемый металл обрабатывают до полного затупления резца при нескольких скоростях резания, и на основе полученных данных находят величину скорости резания, соответствующую определенной условной стойкости инструмента. При точении такая условная стойкость составляет 60 мин, а в качестве показателя обрабатываемости принимается скорость резания υ₆₀.
Стойкость режущего инструмента. С повышением скорости резания стойкость инструмента снижается. Эта зависимость согласно экспериментальным данным может быть выражена формулой
, где А - постоянная, зависящая от свойств обрабатываемого материала, глубины резания, подачи, материала режущей части резца, геометрии инструмента; Т - время работы резца до затупления (стойкость инструмента) в мин; т - показатель степени, зависящий от свойств обрабатываемого материала, материала режущей части инструмента и характера обработки (показатель относительной стойкости).
При обработке сталей резцами из быстрорежущей стали т = 0,125, при обработке чугуна т = 0,1; для резцов, оснащенных твердым сплавом, т = 0,15 - 0,2.
Подача и глубина резания. Увеличение подачи и глубины резания обусловливает увеличение объема снимаемого металла, а следовательно, увеличение силы резания и количества выделяемого тепла. Это приводит к ускоренному износу резца, к снижению его стойкости, а следовательно, к необходимости уменьшения скорости резания.
В общем виде зависимость скорости резания от глубины резания и подачи может быть выражена следующей формулой:
где Cυ - коэффициент, зависящий от условий обработки (обрабатываемого материала, материала режущей части инструмента, геометрии инструмента, охлаждения и т. д.); t - глубина резания в мм; s - подача в мм/об; xυ, yυ- показатели степеней, величина которых определяется свойствами обрабатываемых металлов, материалом инструмента и условиями обработки.
При точении и растачивании заготовок из углеродистой стали резцами из быстрорежущей стали для подачи s ≤ 0,25 мм/об xυ = 0,25, yυ = 0,33, для подачи s > 0,25 мм/об xυ = 0,25, yυ = 0,66.
Из приведенных значений видно, что изменение подачи более резко сказывается на изменении скорости резания, чем изменение глубины резания, так как показатель степени при подаче больше, чем при глубине.
Геометрические элементы инструмента. Чем больше передний угол, тем меньше сила резания и тепловыделение, тем выше казалось бы должна быть и стойкость инструмента. Однако она повышается лишь до некоторого предела. Увеличение переднего угла γ ведет в свою очередь к уменьшению угла заострения и объема головки резца, вследствие чего уменьшается прочность режущей кромки и ухудшается теплоотвод.
Для каждого материала заготовки, материала резца и других условий есть свое оптимальное значение угла γ. При этом чем выше твердость обрабатываемого материала, тем меньше положительное значение оптимального переднего угла. Аналогично влияет на стойкость величина заднего угла α.
С увеличением главного угла в плане при постоянных значениях подачи и глубины резания увеличивается толщина и уменьшается ширина среза. При этом уменьшается длина режущей кромки, участвующей непосредственно в резании, повышается тепловая нагрузка, приходящаяся на единицу длины режущей кромки, повышается износ резца, снижается его стойкость. При уменьшении углов в плане наблюдается обратная картина. Следовательно, резцы с меньшими углами в плане допускают применение большей скорости резания.
Влияние охлаждения на скорость резания было рассмотрено выше.
Допускаемая резцом скорость резания с учетом влияния перечисленных выше факторов при продольном точении может быть подсчитана по следующей общей формуле:
где Cυ - коэффициент, характеризующий обрабатываемый материал и условия обработки; T - стойкость резца в мин; t - глубина резания в мм; s - подача в мм/об; xυ, yυ, m - показатели степеней, k - общий поправочный коэффициент, представляющий собой произведение ряда отдельных поправочных коэффициентов на условия резания (механические свойства обрабатываемого материала, материал режущей части резца и т. д.).
§ 11. Материалы для изготовления режущих инструментов
Материал рабочей части любого режущего инструмента должен обладать следующими качествами: твердостью, превышающей твердость обрабатываемого материала, при сочетании ее с возможно меньшей хрупкостью; теплостойкостью (или красностойкостью), т. е. способностью сохранять исходную твердость при нагреве до значительных температур в процессе резания; большой износостойкостью; высокой механической прочностью.
Для изготовления рабочей части режущего инструмента применяют следующие материалы: инструментальные углеродистые стали, инструментальные легированные стали; быстрорежущие стали; металлокерамические твердые сплавы; минералокерамические материалы; алмазы.
Углеродистые инструментальные стали. Эти стали содержат 0,7 - 1,2% углерода. Твердость углеродистых инструментальных сталей после соответствующей термической обработки равна НRС 58 - 62; они обладают хорошей вязкостью и высокими механическими свойствами. Наиболее распространенные стали этой группы - стали марок У10А и У12А.
Недостаток углеродистых инструментальных сталей - сравнительно низкая теплостойкость. Они теряют свою твердость, а следовательно, и режущие свойства при температуре до 200 - 250' С. Поэтому инструментальные стали находят ограниченное применение для инструментов, обрабатывающих мягкие материалы или работающих с низкими скоростями (например, для разверток малого диаметра, метчиков и т. п.).
Легированные инструментальные стали. Они содержат 0,9- 1,1% углерода и легируются хромом, вольфрамом и др. Стали этой группы выдерживают температуру до 250 - 300'С, что позволяет повысить скорость резания в 1,2 - 1,4 раза по сравнению со скоростями, допускаемыми углеродистыми инструментальными сталями. Наибольшее распространение получили стали 9ХС, ХВ5, ХВГ. Так как эти стали мало деформируются при термической обработке, они употребляются для изготовления протяжек, сверл, разверток, метчиков, плашек и других инструментов.
Быстрорежущие стали. Стали этой группы содержат 0,7 - 1,55% углерода, 9 - 18% вольфрама, 3,6 - 4,6% хрома, 1,0 - 5,0% ванадия.
Быстрорежущая сталь дает возможность работать при температуре резания до 600'С. Из быстрорежущей стали выполняется только рабочая часть резцов. Пластинки, форма и размеры которых стандартизованы, навариваются на державку из обычной конструкционной стали.
У сверл, крупных метчиков и др. рабочая часть также выполняется из быстрорежущей стали и приваривается к нерабочей, выполняемой из конструкционной стали.
Получили распространение следующие марки быстрорежущих сталей: Р18, Р9, Р18Ф2, Р9Ф5, Р14Ф4, Р9К5; Р9К10, Р18К5Ф2 и Р10К5Ф5. В перечисленных марках сталей буква Р обозначает, что сталь относится к группе быстрорежущих; цифра, стоящая после буквы Р, показывает среднее содержание вольфрама (в %); цифра после буквы Ф - среднее содержание ванадия; цифра после буквы К - среднее содержание кобальта.
После соответствующей термической обработки инструмент из быстрорежущей стали имеет твердость HRC 62 - 65 и может работать при скоростях резания, в 2 - 3 раза превышающих скорости, допускаемые инструментальной углеродистой сталью.
Для придания быстрорежущей стали высокой твердости ее подвергают закалке в масле или селитре и многократному отпуску при высокой температуре.
Наиболее широкое распространение в промышленности получили быстрорежущие стали марок Р9 и Р18. В стали Р9 содержится дефицитного и дорогого вольфрама вдвое меньше, чем в стали Р18, однако она несколько уступает последней в режущих свойствах.
Стали Р18, Р9 и Р18Ф2 относятся к сталям нормальной производительности, остальные стали - к сталям повышенной производительности.
Кобальтовые стали Р9К5, Р9К10, Р18К5Ф2 и Р10К5Ф5 имеют в 2 - 3 раза большую твердость, красностойкость и износостойкость, чем сталь Р18, и наиболее эффективны при обработке высоколегированных сталей твердостью НВ З00 - 350, а также при обработке жаропрочных сплавов и сталей.
Твердые сплавы. Твердые сплавы сохраняют высокую твердость при нагреве до температуры 800 - 900'С. Основу их составляют карбиды (химические соединения с углеродом) тугоплавких металлов. Твердые сплавы не нуждаются в термической обработке и приобретают высокие режущие свойства в процессе их производства. При правильном использовании твердосплавного инструмента им можно работать со скоростями резания, в 5 - 8 раз превышающими скорости резания, характерные для инструмента из углеродистой стали.
Твердые сплавы имеют столь высокие режущие свойства благодаря тому, что карбиды тугоплавких металлов, из которых они в основном состоят обладают исключительно высокими твердостью (HRA 88 - 92), износостойкостью и теплостойкостью. Связующий кобальт придает им некоторую вязкость.
Для изготовления металлорежущих инструментов применяют вольфрамовые твердые сплавы (группа ВК) - ВК-2, ВКЗМ, ВК4, ВК6М, ВК8, ВК8В; титановольфрамовые твердые сплавы (группа ТК) - Т5К10, Т14К8, ТЗ0К4; титанотанталовольфрамовые твердые сплавы - ТТ7К12, ТТ7К15.
Твердые сплавы группы ВК применяются для обработки чугуна, твердых хрупких металлов и неметаллических материалов. Твердые сплавы группы ТК применяются при обработке сталей. Титанотанталовольфрамовые сплавы являются сплавами повышенной прочности и применяются при черновой обработке сталей и при работе с ударом.
Твердые сплавы для оснащения металлорежущего инструмента выпускаются в виде пластинок или в форме сплошных и пустотелых столбиков. Для резцов и торцевых фрез применяются многогранные твердосплавные пластинки. По мере износа эти пластинки не перетачиваются, а переустанавливаются, и в работу вступает следующая грань.
В последнее время получили также некоторое распространение монолитные конструкции инструментов малых размеров (сверла, червячные фрезы и др.) из пластифицированных твердых сплавов.
Минералокерамические материалы. Эти материалы получаются на основе окиси алюминия Al₂О₃. Минералокерамические сплавы обладают высокой твердостью (HRА 89 - 95), износостойкостью и теплостойкостью (1200 С). Минералокерамика является хорошим дополнением к твердым сплавам, особенно при обработке деталей из отбеленного чугуна, закаленных сталей и других труднообрабатываемых материалов, а также при обработке деталей с большими длинами прохода. Скорость резания такими резцами может достигать 200 м/мин [3,5 м/с]. Однако высокая хрупкость ограничивает их широкое применение в промышленности.
Наиболее высокие режущие свойства обеспечивает керамический материал марки ЦМ-332.
Материалы, содержащие кроме окиси алюминия присадки металла в количестве 5 - 40% (керметы), менее хрупки, но они имеют пониженную износостойкость.
Алмазы. Применение алмазов для режущего инструмента, особенно в связи с успешным решением задачи по изготовлению искусственных алмазов, все время расширяется.
Алмазы характеризуются весьма высокой твердостью и износостойкостью. Микротвердость алмазов превосходит микротвердость твердых сплавов примерно в 6 раз.
Недостатком алмазов является их высокая хрупкость, поэтому использование алмазов возможно только в случае тонкой финишной обработки металлов с небольшой глубиной резания и подачей. Для изготовления резцов применяют кристаллы алмаза весом 0,31 - 0,85 карата (0,062 - 0,17 г) и более, которые удерживаются в державке пайкой или механическим креплением. Алмазными резцами обрабатываются только цветные металлы и сплавы и неметаллические материалы.