ПРОИЗВОДСТВО СТАЛИ
§ 11. Химические процессы производства стали
Химический состав передельного чугуна характеризуется повышенным содержанием в нем углерода и других примесей. Передельный чугун содержит: 3,5 - 4,2% углерода, 0,2 - 1,75% кремния, 0,5 - 1,75% марганца, до 0,08% серы и до 0,07% фосфора. Сталь отличается от чугуна более низким содержанием углерода и других примесей и чаще всего содержит 0,05 - 1,5% углерода, до 0,5% кремния, 0,5 - 0,8% марганца, до 0,05% серы и до 0,05% фосфора.
Главной целью сталеплавильного процесса является удаление содержащихся в чугуне избыточных примесей с помощью окислительно восстановительных процессов, протекающих в сталеплавильных агрегатах.
В сталеплавильных печах кислород наиболее быстро окисляет железо, концентрация которого значительно превышает концентрацию других элементов в сплаве: 2Fe + O2 = 2FeO + 63 000 кал (264,1 кДж).
Образующаяся закись железа хорошо растворима как в металле, так и в шлаке и играет роль главного носителя кислорода. Атмосферный кислород окисляет шлак, а из шлака поступает в виде закиси железа в металл. Любое повышение содержания кислорода в шлаке сопровождается увеличением его содержания в металле. Кремний, марганец, углерод и другие примеси стали обладают более высоким сродством к кислороду, чем железо, и поэтому они отбирают кислород у железа, восстанавливают его, а сами окисляются (выгорают). Жидкие окислы этих элементов всплывают и попадают в более легкий шлак, покрывающий металл; газообразные окислы уходят в атмосферу или, соединяясь с другими окислами, образуют жидкие вещества, также попадающие в шлак. Окисление примесей идет за счет газообразного кислорода, а также закиси железа по реакциям
- Si + О2 = SiO2; Si + 2FeO = SiO2 + 2Fe
- Mn + 1/2 O2 = MnO; Mn + FeO = MnO + Fe
- 2С + О2 = 2СО; С + FeO = СО + Fe
- СО + 1/2 О2 = СО2
- 2Р + 2 1/2 О2 = Р2О5; 2Р + 5FeO = Р2О5 + 5Fe
- Р2О5 + 3FeO = (FeO)3•P2O5
Фосфор является вредной примесью стали, так как сообщает ей хрупкость (хладноломкость) при комнатных и особенно низких температурах. Поэтому удаление фосфора - важная задача при выплавке стали. Образующийся при сгорании фосфора газообразный ангидрид Р2О5 и его нестойкое соединение с закисью железа трудно удалять из печи, так как при определенных условиях фосфор восстанавливается, переходит в металл и насыщает его. Надежное удаление фосфора достигается только в основных сталеплавильных печах, футерованных основными огнеупорами. В такие печи без опасения разъединения их стенок загружают известь, которая связывает фосфор в прочное химическое соединение и переводит его в шлак:
(FeO)3•Р2О5 + 4СаО = (СаО)4•Р2О5 + 108 340 кал (453,9 кДж).
Однако и это химическое соединение при высоких температурах может отдавать фосфор в металл. Поэтому после образования высокоосновного фосфористого шлака его удаляют из сталеплавильных печей.
Сера, также являясь вредной примесью стали, сообщает ей повышенную хрупкость (красноломкость) при высоких температурах. Удаление серы возможно только в основных печах за счет добавок извести и получения шлаков высокой основности:
- FeS + СаО ↔ CaS + FeO - 4380 кал (18,4 кДж);
- MnS + СаО ↔ CaS + MnO - 7800 кал (32,7 кДж).
Повышение содержания извести обусловливает протекание этих реакций в направлении слева направо, а повышение содержания в шлаке FeO или MnО - течение этих реакций в обратном направлении. Снижение содержания серы в стали достигается особенно хорошо в электрических печах применением восстановительных карбидных шлаков, содержащих графит или карбид кальция:
- FeS + СаО + С = CaS + Fe + СО; MnS + СаО + С = CaS + Mn + СО; 3FeS + СаС2 + 2СаО = 3Fe + 3CaS + 2СО; 3MnS + СаС2 + 2СаО = 3Mn + 3CaS + 2СО.
Закись железа, играющая роль носителя кислорода в сталеплавильных печах, необходима в период выгорания примесей. Однако после этого она должна удаляться из металла, так как подобно сере является вредной примесью, сообщает стали красноломкость и снижает механические свойства. Процесс освобождения стали от кислорода, содержащегося в ней в виде закиси железа FeO, называется раскислением. Этот процесс является важнейшим периодом плавки и производится за счет содержащегося в стали углерода и специально вводимых в сталь раскислителей. Последние добавляются как в конце плавки перед выпуском стали, так и в период выпуска. Раскисление производится присадками в сталь ферромарганца, ферросилиция и алюминия, которые, соединяясь с кислородом, восстанавливают железо. Получающиеся окислы SiO2, MnO и Al2O3 переходят в шлак. Углерод и марганец - наиболее слабые раскислители, а алюминий наиболее сильный. Раскисление идет по реакциям
- FeO + С = СО + Fe; FeO + Mn = MnO + Fe; 2FeO + Si = SiO2 + 2Fe; 3FeO + 2Al = Al2O3 + 3Fe.
Наиболее полно очищенная от кислорода сталь называется спокойной. Слиток такой стали получается плотным, без пузырей, с сосредоточенной усадочной раковиной в прибыльной части слитка. Спокойная сталь может содержать значительные количества углерода (до 2%) и выплавляется в мартеновских и электродуговых печах. Наряду со спокойной сталью в конверторах и мартеновских печах выплавляют кипящую неполностью раскисленную сталь, которая обычно содержит мало углерода (0,02 - 0,3%) и раскисляется только ферромарганцем и небольшими количествами алюминия.
Содержащийся в стали в значительных количествах кислород при остывании ее в изложницах взаимодействует с углеродом. Бурно выделяющаяся окись углерода перемешивает сталь и создает видимость ее кипения. В слитке кипящей стали вместо сосредоточенной усадочной раковины получается много газовых пузырей и пор. Поэтому отход от прибыльной и донной частей слитков снижается. Кипящая сталь дешевле спокойной. Она почти не содержит кремния, хорошо поддается штамповке, но более хрупка на холоду и склонна к старению. Наряду со спокойной и кипящей сталью производится и полуспокойная сталь, раскисленная уменьшенными количествами марганца, кремния и алюминия.
§ 12. Производство стали в конверторах
Производство стали в кислых конверторах. В конверторах выплавляется свыше 17% стали, выпускаемой в нашей стране.
Кислые (бессемеровские) конверторы представляют собою печи грушевидной формы (рис. II.3, а), состоящие из стального кожуха с футеровкой (кладкой) из кислого динасового кирпича емкостью 10 - 50 т и более. В нижней части конверторы имеют приставные днища и воздушную коробку, через которую в конверторы вдувается ненагретый воздух под давлением 2,5 ат (0,25 МПа). Конвертор покоится на колоннах и специальным механизмом может поворачиваться вокруг горизонтальной оси. Перед началом плавки конвертор устанавливают горизонтально, подают дутье, через горловину заливают жидкий бессемеровский чугун, переводят конвертор в вертикальное положение и ведут продувку. Тепло в конверторах получается за счет выгорания примесей чугуна; специального отапливания не требуется. При продувке чугуна кислород воздуха окисляет железо, образует закись железа, растворимую в металле. Наличие кислорода воздуха и закиси железа обусловливает выгорание примесей чугуна: кремния, марганца и углерода по реакциям, приведенным выше. Жидкие продукты реакций всплывают и попадают в шлак, газообразные удаляются через горловину конвертора.
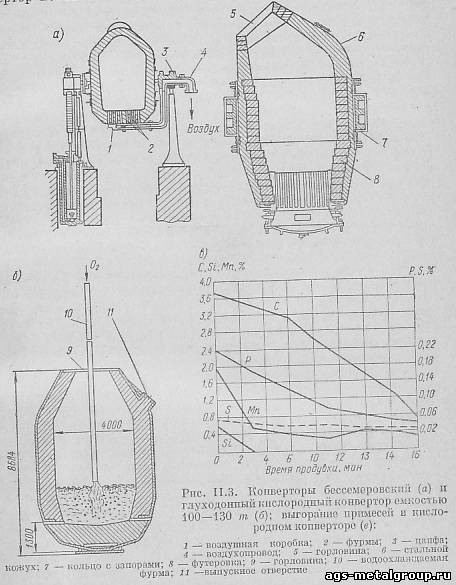
В первый период (примерно 4 мин) интенсивно выгорают кремний и марганец. При этом образуется большое количество тепла и металл разогревается. Особенно много тепла получается при сгорании кремния. Во второй период плавки (с 4 до 10 мин) интенсивно выгорает углерод. Образующаяся окись углерода по выходе из горловины сгорает, образуя длинный факел ярко-белого пламени. После выгорания углерода в третий период (с 10 до 12 мин) начинает выгорать железо с образованием бурого дыма и тогда плавку прекращают. Для этого конвертор опять переводят в горизонтальное положение и прекращают дутье. Металл раскисляют присадкой ферромарганца, ферросилиция, алюминия, добавками чугуна доводят его состав до требуемого и выливают через горловину. Весь процесс плавки в зависимости от хода процесса и емкости конвертора продолжается 20 - 25 мин.
Недостатками плавки стали в конверторе с кислой футеровкой на воздушном дутье являются: необходимость использования высококремнистых, чистых по сере и фосфору чугунов, значительный, угар металла в 8 - 12%, невозможность переплавки больших количеств металлического лома, а также удаления серы и фосфора из чугуна, вследствие чего количество их в бессемеровской стали получается значительно выше, чем у мартеновской. Кроме того, бессемеровская сталь при продувке воздуха сильно насыщается азотом, содержание которого достигает 0,012 - 0,015%. В связи с этим в конверторах на воздушном дутье получают сталь обыкновенного качества, которая по сравнению с качественной сталью обладает пониженной ударной вязкостью, повышенной хладноломкостью, худшей свариваемостью и повышенной склонностью к старению.
Кислородно-конверторный способ производства стали. Основной метод конверторного передела чугуна на сталь в настоящее время - плавка стали в основных глуходонных конверторах с продувкой сверху технически чистым кислородом. Емкость таких кислородных конверторов - 30, 50 и 100 - 130 т. Емкость их предполагается увеличить до 250 - 350 т. Кладка конверторов основная - смолодоломитовая или магнезитохромитовая. Как видно из рис. II.3, б, кислородный конвертор имеет более симметричную форму, глухое съемное дно и сверху выпускное отверстие для стали. В таких конверторах могут перерабатываться чугуны с широкими колебаниями химического состава, но чаще перерабатываются жидкие мартеновские чугуны. Кроме чугуна в конверторы загружают до 30% металлического лома, железную руду и флюсы- известь, боксит и плавиковый шпат. Технически чистый кислород под давлением до 12 ат (1,2 МПа) подается сверху через водоохлаждаемую фурму на зеркало жидкого металла. За счет кислорода и закиси железа происходит интенсивное выгорание кремния, марганца и фосфора (рис. II.3, в). Температура металла в зоне действия кислорода достигает 3000' С, и весь металл в конверторе сильно разогревается. Снижение температуры металла достигается введением охладителей - лома, руды и флюсов. Углерод сначала выгорает медленно, а после разогрева металла выгорание его ускоряется. Контроль за содержанием углерода производится спектральным методом.
В основных кислородных конверторах за счет введения извести и повышенной основности шлаков достигается снижение содержания в стали фосфора и серы. Продолжительность продувки в 100-тонном конверторе составляет 14 - 18 мин, а общая продолжительность плавки 45 мин. В конце плавки металл доводится до заданного состава, раскисляется и выпускается через боковое отверстие, а шлак - через горловину. В кислородных конверторах получают сталь с низким содержанием азота, серы и фосфора как обыкновенного качества, так и качественную, по своим свойствам не уступающую мартеновской стали. Кроме углеродистых сталей выплавляются низколегированные и в качестве опыта легированные стали. Удельные капитальные затраты на строительство конверторных цехов на 35% ниже, чем на строительство мартеновских цехов. Себестоимость конверторной стали на 3,5% ниже, чем мартеновской, а производительность труда в конверторных цехах на 45% выше, чем в мартеновских. Поэтому кислородноконверторный способ передела чугуна можно считать наиболее рентабельным и перспективным. Недостатками способа являются: повышенный расход огнеупоров и высокий угар металла.
Плавка в конверторах поддается автоматизации с использованием счетно-решающих устройств.
Наряду с переделом чугуна на сталь в конверторах стационарного типа разработаны более совершенные процессы получения стали во вращающихся агрегатах. В связи с лучшим перемешиванием металла, двойной сменой шлака эти агрегаты отличаются повышенной производительностью, а выплавляемая в них сталь- повышенным качеством.
§ 13. Производство стали в мартеновских печах
В мартеновских печах выплавляется до 70% стали. К достоинствам этого способа выплавки стали относятся: возможность использования больших количеств металлического лома, менее жесткие требования к составу шихтовых материалов, хорошая управляемость и возможность автоматизации процессов плавки, широкий ассортимент и удовлетворительное качество выплавляемых марок стали, повышенная точность химического состава, а также малый угар металла. Недостатки способа заключаются в периодичности процесса плавки, сложности оборудования, а также в более высокой стоимости выплавляемой стали по сравнению со сталью, получаемой в конверторах.
§ 14. Устройство и работа мартеновской печи
Современные мартеновские печи большой емкости в 500 - 900 т используются для получения слитков, печи малой емкости в 20 - 100 т - в производстве фасонных отливок.

Рабочее пространство печи (рис. 11.4) ограничено сверху сводом, а с боков - стенками и откосами. В передней стенке имеются завалочные окна для загрузки сырых материалов.
Нижняя часть рабочего пространства ограничена откосами и подом, образующими ванну, в которой размещается металл. Под печи имеет наклон в сторону отверстия для выпуска стали. В зависимости от вида огнеупорных материалов металлической ванны мартеновские печи подразделяются на кислые и основные. Последние наиболее распространены на отечественных заводах. Левая и правая головки мартеновской печи служат для подвода горючего газа и нагретого воздуха по отдельным каналам, для смещения и сжигания газа на выходе в рабочее пространство печи. При работе печей на мазуте они имеют только два регенератора для нагрева воздуха; головка имеет один канал для подвода нагретого воздуха и форсунку для сжигания горючего. Получение высоких температур в рабочем пространстве печи 1800 - 2000' С возможно только при использовании нагретого воздуха, а при работе на газе - и нагретого газа (смеси доменного, коксовального и генераторного). Нагревание газа и воздуха осуществляется в регенераторах за счет тепла отходящих газов.
Воздушные и газовые регенераторы представляют собой камеры, заполненные огнеупорным кирпичом, уложенным в виде фигурной насадки. Печь работает поочередно правой или левой стороной. При работе правой стороной насадка правых регенераторов нагрета до высокой температуры. Холодные газ и воздух поступают в правые регенераторы, где нагреваются до 1100 - 1300°С, затем через шлаковики и далее по отдельным каналам проходят в правую головку и по выходе из нее смешиваются; при этом газ сгорает, образуя пламя с температурой 1800 - 2000° С. Проходя через рабочее пространство справа налево, пламя отдает свое тепло металлу и стенкам печи. По выходе в левую головку продукты сгорания с температурой 1650 - 1670° С по каналам направляются в левую пару регенераторов, отдают тепло насадкам, охлаждаются до 500 - 600° С и через систему каналов направляются в боров и через трубу в атмосферу. Часть газов с температурой 500 - 600° С направляется в котлы-утилизаторы, в которых используется их тепло. По мере охлаждения правых регенераторов и нагрева левых производится переключение клапанов. Холодные газ и воздух направляются не в правую, а в левую пару регенераторов. Смена направлений подачи газа и воздуха осуществляется автоматически через каждые 20 - 30 мин.
Наиболее сильному химическому воздействию подвергаются под и откосы металлической ванны печи. В основных мартеновских печах они выкладываются магнезитовым кирпичом и навариваются магнезитовым и доломитовым порошками. В кислых печах под и откосы футерованы динасовым кирпичом и навариваются кварцевым песком. Твердые шихтовые материалы подаются из шихтового двора на рабочую площадку мартеновской печи в металлических коробах (мульдах) и с помощью завалочной машины через завалочные окна загружаются в мартеновскую печь. Жидкий чугун подвозится на рабочую площадку в ковшах и через желоб и завалочные окна заливается в печь. По окончании плавки сталь выпускается через отверстие в задней стенке печи по желобу в сталеразливочный ковш. Шлак выпускается также через специальное отверстие в шлаковозный ковш.
§ 15. Плавка стали в мартеновских печах
Для плавки стали в основных мартеновских печах в зависимости от состава и состояния металлической части шихты применяются различные процессы.
- Скрап-процесс с завалкой в печь 60 - 70% металлического скрапа (лома) и 40 - 30% чугуна. Применяется на заводах, не имеющих доменных печей и жидкого чугуна.
- Скрап-рудный процесс с заливкой в печь 55 - 75% жидкого чугуна и завалкой остального количества скрапа. Кроме того, в печь вводят 12 - 20% (от веса металла) руды. Используется на заводах, имеющих доменные печи.
- Рудный процесс с заливкой в печь жидкого чугуна и добавкой железной руды. Применяется на заводах, имеющих свои доменные печи.
Наиболее часто применяются два первых вида процесса.
§ 16. Плавка стали в основной мартеновской печи
Плавка стали на твердой завалке (скрап-процесс) состоит из нескольких периодов: заправки пода и откосов, завалки и прогрева шихты, плавления, кипения, раскисления, доводки и выпуска стали. Заправка печи заключается в устранении повреждений пода и откосов во время предыдущей плавки. Завалка начинается с подачи в печь руды и известняка, скрапа и чугуна. В период завалки и последующего расплавления происходит образование шлака, содержащего около 35 - 45% СаО, 13 - 17% MnO и 10 - 15% FeO. Кислород воздуха окисляет шлак и через него железо. Образующаяся закись железа распределяется между шлаком и металлом. В первичный шлак попадает значительное количество содержащегося в шихте фосфора. Во избежание его восстановления и возврата в металл первичный шлак через завалочные окна удаляют (скачивают) и, вводя новые порции извести и боксита, наводят новый шлак.
Добавкой руды повышают окислительную способность шлака, в результате чего идет окисление углерода, сопровождающееся выделением больших количеств окиси углерода, что приводит к сильному бурлению - кипению металла. В период кипения происходят интенсивное перемешивание металла, выравнивание его температуры и химического состава, а также более полное удаление из металла частиц шлака.
Химический состав металла и шлака по ходу плавки контролируется многократным отбором проб жидкого металла и шлака и их химическим анализом в экспресс-лаборатории сталеплавильного цеха.
После снижения содержания углерода в металле до требуемого уровня (немного ниже того, который должен быть в стали), а также после получения требуемой температуры ванны и состава шлака кипение стали за счет добавок раскислителей прекращают и доводят химический состав металла до заданного. Содержание углерода, кремния и марганца в спокойной стали повышают добавками ферросплавов, для чего в печь вводят определенные (взвешенные) количества ферросплавов. Окончательное раскисление спокойной стали производится при выпуске стали присадкой 45-процентного ферромарганца и алюминия. Кипящую сталь раскисляют за 3 - 5 мин до выпуска присадкой в ванну ферромарганца и присадками алюминия в ковш. Ферросилиций при раскислении кипящей стали не применяется. В основной мартеновской печи содержание серы понижают получением больших количеств высокоосновного жидкоподвижного шлака и поддержанием на высоком уровне его температуры.
В основной печи, кроме углеродистой, выплавляется и легированная сталь. Легирующие элементы вводятся в сталь в различные периоды плавки. Мало выгорающие присадки (никель) вводят в начале плавки, сильно выгорающие (хром) - в конце плавки. Угар легирующих элементов колеблется от нескольких процентов до 40 - 60 (для титана). Выпуск готовой стали производится в сталеразливочные ковши.
§ 17. Особенности плавки стали в кислых мартеновских печах
В кислых мартеновских печах выплавляют стали, обладающие высокими и однородными механическими свойствами, содержащие меньшие, чем в основных сталях, количества неметаллических включений (инструментальные, шарикоподшипниковые и другие высококачественные стали). Характерными особенностями плавки стали в кислых печах являются:
1) использование шихты и топлива, содержащих мало серы и фосфора, удаление которых из металла в кислых печах затруднено;
2) наличие кислого пода с высоким содержанием SiO2 и высококремнистых шлаков при малом содержании закиси железа, обеспечивающих при высоких температурах благоприятные условия для восстановления кремния из кладки печи по реакциям
- SiO2 + 2Fe = Si + 2FeO - 78 000 кал (326,8 кДж);
- SiO2 + 2С = Si + 2СО - 152 568 кал (640 кДж).
Восстановленный кремний в кислых печах играет роль активного раскислителя.
§ 18. Технико-экономические показатели плавки в мартеновских печах
Работа мартеновских печей оценивается по суточному съему стали с 1 м² пода печи, по годовой производительности (тыс. т/год) и расходу условного топлива (теплота сгорания последнего равна 7000 кал/кг) на 1 т выплавленной стали (1 кг топлива/1 т стали). Величина суточного съема стали с 1 м² пода печи в т/м² рассчитывается как частное от деления суточной выплавки стали на площадь пода на уровне низа завалочных окон печи (порогов). Съем стали в среднем составляет около 8 т/м² и колеблется в пределах 7,3 - 12 т/м². При использовании кислорода съем возрастает до 20 - 30 т/м². Расход условного топлива 130 - 250 кг/т. Производительность мартеновских печей повышается на 25 - 50% за счет применения кислорода, который вводят в зону горения топлива (в факел) или прямо в металл через водоохлаждаемые фурмы, или обоими способами одновременно.
Снижение расхода топлива на 5% и повышение производительности печей на 5 - 8% при одновременном сокращении расхода огнеупоров на 8 - 10% достигается автоматизацией управления тепловым режимом печей. Применение высокоогнеупорных хромомагнезитовых кирпичей вместо динаса для кладки сводов печей повышает производительность печи на 6 - 10%.
Значительная интенсификация процессов выплавки стали, а также резкое повышение стойкости головок печей достигается использованием печей с двумя сталеплавильными ваннами (двухванных). При этом межремонтный срок службы печей возрастает в 2 - 3 раза.