§ 19. Плавка стали в электродуговых печах
Более удовлетворительная атмосфера электрических печей и высокие температуры позволяют выплавлять в них стали высокого качества с низким содержанием вредных примесей, шлаковых включений и газов. В электрических печах выплавляют в основном высококачественные инструментальные, нержавеющие, жаростойкие, жаропрочные, шарикоподшипниковые стали и др.
Для выплавки стали наиболее часто используются электродуговые печи, в которых электрическая дуга возбуждается между графитированными или угольными электродами и металлической шихтой (дуга прямого действия). Схема устройства дуговой электропечи с тремя электродами приведена на рис. 11.5. Она состоит из сварного кожуха 1, имеющего форму цилиндра с выгнутым овальным основанием, футеровки 4, съемного или отворачивающегося свода 6, состоящего из металлического каркаса с динасовой или хромомагнезитовой футеровкой. Свод имеет три отверстия, через которые проходят электроды 7, удерживаемые и автоматически перемещаемые по вертикали электрододержателями с помощью механизма 8, управляемого регулятором. Дуга возбуждается между электродами 7 и металлической шихтой 10. Печь покоится на опорных станинах 3 и роликах. С помощью механизма 2 печь при выпуске стали может наклоняться в сторону выпускного отверстия и желоба 5, а при скачивании шлака - в сторону загрузочного окна 9.
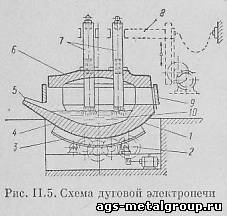
Печи питаются трехфазным переменным током через трансформатор мощностью до 40000 ква и более, понижающий напряжение до 130 - 300 в. В шихту печей вводят стальной лом, легированные отходы, чугун, флюсы (известняк, плавиковый шпат), железная руда, легирующие добавки и раскислители. Шихта в электродуговые печи загружается сверху с помощью бадьи с открывающимся дном или грейфером. Мелкие печи загружаются шихтой через загрузочное окно.
Плавка стали в основных электродуговых печах. Плавка производится с полным окислением примесей, с частичным их окислением или вовсе без окисления - методом переплава. Первый метод позволяет выплавлять сталь с наименьшим содержанием вредных примесей, последний (упрощенный) не обеспечивает получения такой стали и она получается более загрязненной примесями и водородом. Плавка в электропечи с полным окислением примесей состоит из заправки пода, завалки шихты, плавления, окислительного и восстановительного периодов и выпуска стали. Электрический ток включается после заправки пода и завалки шихты. Применение кислорода сокращает период плавления на 10 - 15%. В период плавления почти полностью окисляются кремний, алюминий, титан и частично марганец, углерод и фосфор. Шлак в конце периода плавки содержит около 40% СаО, 20% SiO2, 8% MnO, 12% FeO и до 1% Р2О5. Целью окислительного периода является дальнейшее окисление примесей (углерода, марганца, хрома и др.), максимальное удаление фосфора и газов, а также нагрев металла. Окисление производится за счет присадок в печь руды или подачи кислорода. По расплавлении шихты в печь присаживают руду и известь и удаляют полученный шлак, содержащий фосфор. Для более полного удаления фосфора наводят и удаляют второй шлак. Содержание фосфора снижается до 0,01 - 0,012%.
В процессе кипения стали в окислительном периоде содержание углерода снижается, удаляются азот и водород, а также сера. Окислительный период заканчивается удалением окислительного шлака. В восстановительном периоде производятся раскисление металла, удаление серы и окончательная доводка химического состава стали. Сперва в ванну вводят ферромарганец и кокс или электродный бой, доводят содержание марганца и углерода до требуемого, наводят шлак повышенной основности (вводят в печь 70% извести, 15% плавикового шпата и 15% шамотного боя) и приступают к диффузионному (через шлак) раскислению стали под белым или карбидным шлаком.
После доводки химического состава и раскисления металл выпускают из печи. В основных электродуговых печах выплавляют легированные и высоколегированные стали для слитков, а также для фасонных отливок.
Плавка стали в кислых электродуговых печах. Плавка стали в кислых электродуговых печах отличается более высокой производительностью (продолжительность плавки меньше), меньшими затратами электроэнергии (на 30 - 40%) и огнеупоров. При кислом процессе корректировка состава металла более сложна, расходуется большее количество ферросплавов и предъявляются повышенные требования по ограничению содержания в шихте серы и фосфора. Особенность плавки в кислой электродуговой печи заключается в самораскислении металла кремнием, который перед этим в условиях высокой температуры восстанавливается железом и углеродом из кремнезема футеровки печи. При выплавке высококачественных сталей чаще всего применяется диффузионное раскисление металла (через шлак). В кислых печах выплавляются углеродистые и низколегированные стали для отливок.
§ 20. Технико-экономические показатели работы электродуговых печей
Производительность электродуговых печей в значительной мере зависит от емкости печей, которая колеблется в пределах 0,5 - 180 т и более. Производительность средних основных печей составляет 12 - 15 т/сутки на каждые 1000 ква мощности трансформатора печи. Расход электроэнергии в печах средней емкости составляет 650 - 750 квт•ч/т (2,34 - 2,7 кДж/г), расход графитированных электродов 6,5 кг/т.
Производительность электрических дуговых печей резко повышается за счет применения кислорода, который подают под давлением в 8 - 12 ат (0,8 - 1,2 МПа) железными трубами через завалочные окна прямо в металл или через свод печей водоохлаждаемой фурмой на поверхность шлака. Плавку можно также ускорить применением электромагнитного перемешивания металла с помощью статоров, устанавливаемых под днищами печей. Уменьшение простоев печей и интенсификация теплового режима печи часто достигается применением для сооружения сводов более стойких магнезитохромитовых огнеупорных кирпичей вместо динасовых.
§ 21. Плавка стали в индукционных печах
Индукционные электрические печи используются для выплавки высококачественных сталей и сплавов со специальными свойствами. Тепло для получения высоких температур получается в виде джоулевого тепла, выделяемого в твердом и жидком металле за счет вихревых токов, индуктируемых пульсирующим электромагнитным полем. Последнее создается индуктором(первичной катушкой), питаемым током высокой частоты (100 кгц - 10 Мгц) от высокочастотного генератора. Устройство крупной индукционной печи емкостью 8 т приведено на рис. II.6. Печь состоит из тигля 1 с основной футеровкой, индуктора 3, выполненного из медной трубки в виде соленоида. Внутри индуктора циркулирует вода, а на его корпус подается ток высокой частоты. Печь имеет футировку 2, съемный свод 5 и сливной носок 4. Плавка в индукционных печах ведется как в воздушной среде, так и в вакууме. В случае плавки в вакууме выпуск стали из печи, заливка ее в изложницу и эвакуация слитков из печи производится также в вакууме. Выплавка стали в вакууме дает возможность резко повысить ее качество. Плавка стали в индукционных печах ведется методом переплава. Отсутствие в этих печах угольных электродов, производящих науглероживание металла, позволяет выплавлять в них низкоуглеродистые стали с минимальным количеством неметаллических включений и газов, особенно при плавке стали в вакууме, в контролируемой или нейтральной атмосфере. В вакуумных индукционных печах выплавляют высоколегированные жаростойкие, жаропрочные и конструкционные стали и сплавы с особыми свойствами.
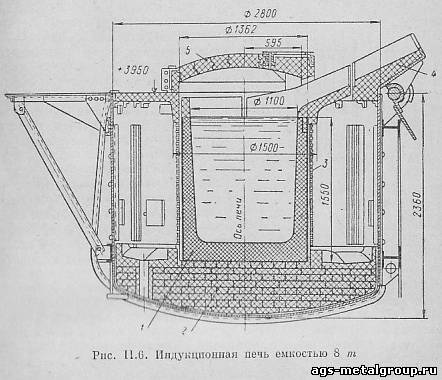
§ 22. Дуговая вакуумная плавка c расходуемым электродом
Влияние на качество стали футеровки и атмосферы печи, электродов и других факторов исключается при плавке под вакуумом (или в защитной атмосфере) в медном тигле. Для охлаждения тигля в стенках его циркулирует вода. Схема такой плавильной установки приведена на рис. 11.7.
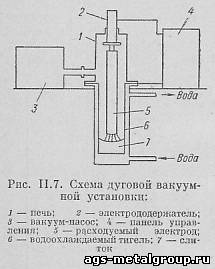
В печь с вакуумом подвешивается расходуемый (подлежащий переплавке) электрод, состоящий из стальной заготовки, предварительно выплавленной в обычной электропечи. Химический состав металла электрода соответствует химическому составу выплавляемого металла, но содержит примеси и газы, от которых он освобождается в процессе переплавки в вакууме. Иногда электроды, представляющие собой шихту для дуговой вакуумной плавки, получают спеканием брикетов или порошков соответствующего состава. Печи питаются постоянным током напряжением около 80 в. Плотность применяемого тока составляет около 500 а/см² (5•10⁶ А/м²) сечения слитка. Расходуемый электрод (шихта) служит катодом, а получаемый в водоохлаждаемом медном тигле слиток очищенного металла - анодом. Между электродом и жидким металлом в тигле образуется электрическая дуга, тепло которой обеспечивает непрерывное расплавление расходуемого электрода. Из жидкого металла в условиях вакуума удаляются газы и примеси. Таким способом получают слитки жаропрочных сплавов, а также слитки таких металлов как молибден, титан, цирконий и др. диаметром 300 - 600 мм весом 0,9 - 5,5 т. Недостатком вакуумной плавки с расходуемым электродом является сложность оборудования и высокая стоимость выплавляемого металла.
§ 23. Электрошлаковый переплав стали
Способ электрошлакового переплава расходуемых электродов в водоохлаждаемом тигле разработан Институтом электросварки им. Е. О. Патона. Способ позволяет производить рафинирование сталей без применения вакуума. Упрощенная схема электрошлакового переплава стали приведена на рис. II.8. Плавящиеся электроды 3 из стали, подлежащей рафинированию, в начале процесса приближаются к сухарям (выступам) поддона 7. При подаче напряжения между двумя электродами и сухарями возникают электрические дуги. За счет тепла дуг флюс расплавляется и образует слой шлака 6. По мере образования слоя шлака достаточной толщины электрические дуги исчезают, и в течение всего процесса переплава тепло возникает за счет прохождения тока через слой шлака, имеющего высокое электросопротивление. Шлак при этом перегревается до температуры 2000' С. В перегретом шлаке металл электродов расплавляется, очищается от примесей и образует слой 2, быстро кристаллизующийся в водоохлаждаемом тигле 1 с образованием слитка 8. По мере расплавления электродов они продвигаются подающим устройством 4 сверху вниз и вместе с тем опускается и слиток 8. Легирующие добавки вводятся из дозатора 5. Металл электродов после расплавления взаимодействует с сильно перегретым шлаком. Происходит рафинирование стали. Содержание серы снижается на 30 - 50%, а других вредных примесей в 2 - 3 раза. Стальной слиток электрошлакового переплава отличается отсутствием грубых строчечных включений, высокой плотностью, чистой поверхностью, отсутствием волосовин, трещин, пор и высокими и однородными механическими свойствами. Методом электрошлакового переплава производится сталь специального назначения: шарикоподшипниковая, инструментальная и др. Плавка методом электрошлакового переплава значительно дешевле плавки в вакуумных печах.
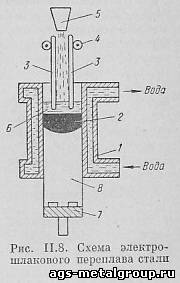
§ 24. Комбинированные методы плавки стали
При выплавке качественных и высококачественных сталей в некоторых случаях различные периоды плавки стали осуществляются в двух сталеплавильных агрегатах различного типа. Например, окисление примесей чугуна производят в кислом конверторе, затем сталь выпускают в ковш, перевозят и заливают в мартеновскую печь, в которой производят рафинирование, доводку и раскисление стали. Процессы такого типа носят название дуплекс-процессов.