ТЕХНОЛОГИЯ СВАРКИ ЧУГУНА, СТАЛИ, ЦВЕТНЫХ МЕТАЛЛОВ И СПЛАВОВ. НАПЛАВКА ТВЕРДЫХ СПЛАВОВ. ПАЙКА МЕТАЛЛОВ И СПЛАВОВ
§ 25. Сварка чугуна
Сварка чугуна наиболее часто применяется для исправления дефектов отливок и при ремонтных работах. В местах сварки чугуна образуется структура белого чугуна повышенной твердости: вследствие чего сварной шов трудно подвергается обработке режущим инструментом. Из-за больших напряжений в изделии образуются трещины. Перед заваркой (сваркой) дефекты вырубают до чистого металла и производят разделку V-образных кромок с углом в 60 - 70'. Края трещин засверливают во избежание расширения их при сварке.
Сварку чугуна производят следующими способами. Горячая сварка применяется в тех случаях, когда после сварки шов подвергается обработке режущим инструментом или должен иметь прочность не ниже основного металла. После V-образной разделки кромок чугунную деталь подвергают нагреву до 550 - 600' С и затем производят газовую или электродуговую сварку с применением прутков или электродов из чугуна.
Предварительный нагрев детали уменьшает скорость затвердевания наплавленного чугуна и его охлаждения и способствует устранению отбеливания. После сварки деталь медленно охлаждают в печи или кладут в яму и засыпают сухим песком.
Мелкие чугунные детали подвергаются общему нагреву, а крупные детали - местному нагреву пламенем древесного угля или кокса в зоне, непосредственно прилегающей к сварочному шву.
При газовой и электродуговой сварке применяют присадочные чугунные прутки или электроды диаметром 8 - 12 мм с повышенным содержанием углерода (3,8 - 4,0%) и кремния (3,4 - 3,6%). При газовой сварке в качестве флюса используют буру Na₂B₄O₇ или буру в смеси с борной кислотой в отношении 1:1. Холодная сварка применяется в тех случаях, когда сварной шов не подвергается механической обработке и может иметь пониженную прочность. Этот способ сварки производится быстро, и он наиболее экономичен. Газовая или электродуговая сварка без подогрева производится с применением присадочных прутков или электродов из малоуглеродистой проволоки. Сварной шов имеет структуру отбеленного чугуна.
При сварке крупных и средних деталей для получения надежного соединения чугуна с наплавленным металлом ввертывают на резьбе в кромки свариваемых деталей стальные шпильки в шахматном порядке. К стальным шпилькам хорошо приваривается электродный металл, в результате чего получают прочное соединение чугунных деталей.
Зачистка сварного шва при сварке без подогрева производится абразивными кругами.
Для уменьшения твердости сварного шва производят сварку биметаллическими электродами (содержащими 60 - 70% меди и 30 - 40% железа), монель-металлом (70% никеля и 30% меди), медноникелевыми и железоникелевыми электродами. Прочность сварного соединения при использовании таких электродов составляет 60 - 80% от прочности основного металла.
Сварка белого чугуна осуществляется электрической дугой или газовым пламенем с применением стальной проволоки, сварка ковкого чугуна - газовым пламенем с латунным присадочным прутком или электродуговая - электродом из медноникелевого сплава. Возможна сварка чугуном с последующим отжигом.
§ 26. Особенности сварки стали
Сварку низкоуглеродистой стали можно производить любыми методами - газовым, электродуговым, контактным и др. Электродуговая сварка имеет наибольшее применение. Стали с содержанием углерода менее 0,25% и низколегированные хорошо подвергаются сварке без применения предварительного подогрева и специальных электродов при условии использования рациональных режимов сварки и надежной защиты наплавленного металла от воздействия воздуха.
При сварке конструкционных сталей - углеродистых и среднелегированных во избежание закалки, образования трещин, изменения структуры необходимо применять в зависимости от химического состава стали предварительный нагрев до 300 С с последующим после сварки отжигом или отпуском. При ручной электродуговой сварке следует применять преимущественно постоянный ток; использовать электроды, обеспечивающие в металле шва необходимые свойства. Для повышения прочности сварного соединения в наплавляемый металл вводят в ряде случаев легирующие элементы (Mn, Si, Сr, Ti и др.), способствующие получению мелкозернистой структуры; производят послойную проковку шва; накладывают валики малого сечения; производят местное охлаждение наплавленного металла теплоотводящими медными прокладками или водой во избежание перегрева зоны сварки.
Сварка высоколегированных сталей производится по специальной технологии в зависимости от марки стали.
§ 27. Сварка цветных металлов и сплавов
Сварка цветных металлов и сплавов часто затруднена ввиду образования тугоплавких окислов, способности к поглощению значительного количества газов (кислорода, азота, водорода и др.), уменьшения прочности и резкого возрастания хрупкости при нагреве и др.
Сварка меди и ее сплавов применяется газовая и дуговая.
Теплопроводность меди в шесть раз больше теплопроводности железа. Медь при повышенных температурах соединяется с кислородом, образуя закись Cu₂O и окись меди CuO, а также насыщается водородом; при нагреве в среднем диапазоне температур пластичность и прочность ее резко снижаются.
При нагреве меди в окислительном пламени образуется закись меди Cu₂O, закись меди восстанавливается водородом Cu₂O + Н₂ =- 2Cu + H₂O с образованием водяного пара, который создает внутреннее давление в металле, приводящее к образованию в нем пор и трещин (водородная болезнь).
Для газовой сварки применяют присадочный материал из меди с содержанием фосфора до 0,25% или кремния 0,15% или чистую электролитическую проволоку, вводя в состав флюса раскислитель - фосфорную медь.
Обычно применяемый флюс имеет в своем составе прокаленную буру или смесь, содержащую 70% буры; 10% борной кислоты, 20% поваренной соли.
Во избежание окисления и перегрева меди сварку производят нейтральным пламенем с повышенной скоростью, при расходе ацетилена почти в два раза большем, чем при сварке стали.
Для повышения прочности сварной шов обычно подвергают ковке при температуре 400 - 500' С с последующим отжигом и охлаждением в воде.
Удовлетворительные результаты получаются при сварке дугой на постоянном токе с применением угольных электродов при прямой полярности. Поверхность основного металла в зоне сварки покрывают порошком того же состава, что и для газовой сварки меди.
Сварку меди металлическим электродом выполняют короткой дугой на постоянном токе обратной полярности. Сварочный ток применяют 50 - 100 а на 1 мм диаметра электрода; электроды, присадочные прутки изготовляются из оловянистой или кремнистой бронзы. Рекомендуется производить предварительный нагрев изделий при толщине стенки более 5 - 6 мм.
Сварное соединение хорошего качества получается при сварке в атмосфере защитного газа (аргон, азот или их смеси) вольфрамовым электродом на постоянном токе прямой полярности.
Сварка латуни производится газовая и электродуговая угольными электродами. Сварка латуни затруднена ввиду значительного испарения цинка; температура кипения цинка 907'С близка к температуре плавления латуни 920 - 950 С. Газовая сварка осуществляется окислительным ацетилено-кислородным пламенем для создания на поверхности ванны пленки тугоплавкой окиси кремния и цинка, защищающей металл от дальнейшего испарения и выгорания цинка. Присадочный пруток обычно изготовляют из латунной проволоки ЛК 62-0,5. Присадочные прутки при электродуговой сварке угольным электродом применяют из фосфористой или кремнистой бронзы. При сварке дугу направляют на конец присадочного прутка, касающегося ванны. Флюс употребляют тот же, что и при сварке меди.
Сварка оловянистой бронзы обычно производится электродуговым металлическим электродом. Применяется также сварка электродуговая с использованием угольных электродов. Электрод применяют литой из фосфористой бронзы. Предварительный нагрев детали производят до 300 - 400' С.
При газовой сварке применяют прутки из фосфористой бронзы или латуни; флюс используют того же состава, что и при сварке меди. Ацетилено-кислородное пламя применяют нейтральное.
Сварку алюминия и его сплавов осуществляют различными способами: газовой сваркой, электродуговой (металлическим и угольным электродами), аргоно-дуговой, диффузионной в вакууме и на контактных машинах. Для понижения температуры плавления тугоплавкой окиси алюминия Al₂O₃ (температура плавления 2050'С) и защиты расплавленного металла от окисления применяют специальные флюсы и обмазки. Для газовой и электродуговой сварки угольным электродом используют флюс следующего состава: 45% хлористого калия, 15% хлористого лития, 30% хлористого натрия, 7% фтористого калия, 3% кислого сернокислого натрия. Обмазка металлических электродов состоит из 35% криолита, 50% хлористого калия, 15% натрия. Газовую сварку производят пламенем с небольшим избытком ацетилена.
Присадочный материал применяют того же состава, что и алюминиевый сплав. Толстостенные изделия перед сваркой подогревают до температуры 300 - 400' С. Поверхность свариваемых кромок тщательно очищается, обезжиривается бензином или каустической содой. Разделку кромок детали производят при сварке алюминия толщиной более 5 - 6 мм.
Электродуговая сварка алюминия и его сплавов выполняется на постоянном токе обратной полярности. Высокого качества шва достигают при сварке в защитных средах.
Для контактной сварки алюминия применяется ток большой силы при незначительном времени его протекания.
Сварка магниевых сплавов осуществляется газовым пламенем, электродуговая-угольным электродом, аргонодуговая, диффузионная в вакууме, контактная и др. Сварка газовым пламенем и электродуговая производится с применением специальных флюсов, понижающих температуру плавления тугоплавкой окиси магния. Хорошее качество достигается при аргонодуговой сварке, которая производится без флюса, при сварке ультразвуком и электронным лучом.
§ 28. Наплавка твердых сплавов на поверхность деталей
Наплавка металла на поверхность детали дает возможность придать ей необходимые механические и физико-химические свойства и тем самым повысить надежность и долговечность работы и снизить себестоимость.
На детали, подвергающиеся при эксплуатации значительному износу, наплавляют сплавы, обладающие повышенной твердостью. Нанесение износостойкого слоя на поверхность стали осуществляется наплавкой электродами, присадочными прутками, зернистыми порошками, содержащими легирующие элементы, а также за счет перехода износостойких металлов и их соединений из специальных флюсов (обмазок) при расплавлении. Чем больше карбидов в наплавленном слое и чем он тверже, тем он более износоустойчив. Один из наиболее дешевых способов нанесения износостойкого слоя на поверхности детали - наплавка отбеленного чугуна, при которой наплавленный слой обладает повышенной твердостью и износостойкостью за счет выделения карбида железа.
Высокой износостойкостью обладают наплавки, содержащие карбиды хрома и особенно бора. Для наплавок применяют хромистые чугуны, хромистые стали 3Х13 и др.
При использовании для наплавки электродов марки ХР19 с легирующей обмазкой наплавленный слой, имеющий повышенную твердость (HRC 60 - 62), содержит 3,1% С; 22 - 25,0% Cr; 1,0% В.
Наплавка твердых сплавов на поверхность деталей увеличивает стойкость последних, уменьшает износ и удлиняет срок работы. Твердые сплавы обладают высокой твердостью (HRC 50 - 90), сохраняющейся, в отличие от закаленной стали, при нагреве до высоких температур значительной хрупкостью, понижающей сопротивление ударным нагрузкам.
Твердые сплавы наплавляют на поверхность деталей, подвергающихся износу; обычная толщина слоя наплавки 1,5 - 2,5 мм.
Механическая обработка наплавленных твердых сплавов производится абразивами. Применяют следующие твердые сплавы.
Литые сплавы, отливаемые в виде прутков диаметром 5 - 6 мм, применяют для наплавки на поверхности деталей, подвергающихся износу при трении о металл (штампы, пуансоны, детали машин). Они отличаются износоустойчивостью при нагреве до 600 - 700' С. К ним относятся: сормайт, содержащий 2,5- 3% С; 25 - 31% Cr; 3,5% Ni, и ВК-3 (стеллит) с содержанием 1- 1,5% С; 28 - 32% Cr; 4 - 5% W; 58 - 62% Со.
Литые сплавы наплавляют газовым пламенем и электрической дугой при помощи угольного или металлического электрода.
При наплавке сплава газовым пламенем (флюс - бура) поверхность металла нагревают сильно науглероженным пламенем для понижения температуры плавления поверхностного слоя основного металла. После расплавления металла на небольшую глубину присаживают расплавленный присадочный пруток из сормайта или сплава ВК-3. Охлаждение детали производят в песке.
Зернистые сплавы используют в виде грубозернистого порошка с зернами размером 1 - 3 мм из материалов, которые после наплавки на деталь превращаются в твердый сплав. Зернистые сплавы применяют для наплавки на поверхности деталей, подвергающихся износу при соприкосновении с породой (детали землеройных машин). К такой группе твердых металлов относятся:
Наименование Состав в %
Сплав сталинит С - 8 - 10; Mn - 13 - 17; Cr - 16 - 20; остальное - Fe
Сплав Вокар С - 9,5 - 10,5; W - 85 - 87
Висхом-9 С - 6; Mn - 15; Cr - 5; остальное - чугунная стружка
Наплавка зернистых сплавов производится дуговой сваркой угольным электродом на постоянном токе при прямой полярности. Перед наплавкой деталь тщательно очищается от окислов и загрязнений, после чего на нее равномерно наносится тонкий слой сплава, расплавляемый затем дугой. Обычно наплавку сталинита производят в два слоя. Желательно по окончании наплавки деталь отжигать при температуре около 900' С с последующим медленным охлаждением.
Трубчатые зернообразные сплавы ТЗ имеют высокую твердость, используют для наплавки бурового инструмента (долота, шарошки). Их изготовляют в виде трубчатых стержней из малоуглеродистой стали диаметром 6-8 мм, наполненных зернами из карбида вольфрама, борида хрома и др.
Высокой износостойкостью обладает сплав КБХ10, содержащий борид хрома, применяемый для наплавки изделия из стали, подвергающегося значительному воздействию абразивной среды. Наплавленный слой металла содержит 2,0 - 2,26% С; 25% Cr; 2,4% В, остальное - Fe. Наплавку сплавов ТЗ производят газовым пламенем или электродугой.
Металлокерамические сплавы в виде пластин из карбидов вольфрама, карбидов титана, карбидов хрома, сцементированных кобальтом или никелем, применяют для режущего и бурового инструмента.
Карбидохромовые твердые сплавы имеют удельный вес в два раза меньший, чем удельный вес вольфрамокобальтовых сплавов, и в 3 - 4 раза меньшую стоимость; сплав может наплавляться на сталь.
Металлокерамические сплавы припаиваются к державке инструмента медью или латунью; нагрев осуществляют газовым пламенем, в машинах для контактной сварки или высокочастотным нагревом.
Плавленые карбиды по химическому составу состоят почти из чистого сплавленного карбида вольфрама; обладают наиболее высокой твердостью и значительной хрупкостью. Отдельные куски наплавленных карбидов ввариваются в расплавленную поверхность инструмента так, чтобы они несколько выступали над поверхностью основного металла. Поверхностное оплавление обычно осуществляется индукционным нагревом.
При работе инструмента происходит более быстрый износ основного металла, чем режущих граней кусков плавленых карбидов, в результате чего выступающие острые грани карбидов хорошо разрушают горную породу при бурении.
Для электрошлаковой наплавки используют специальные электроды, обеспечивающие получение наплавленного слоя толщиной не менее 15 мм нужной твердости. Наибольшее применение при электрошлаковой наплавке имеют порошковые трубчатые электроды.
Для наплавок тонких слоев металла применяют электроимпульсные способы - электроискровой и вибродуговой. При электроискровой наплавке используют в качестве источника тепла искровой разряд незначительной длительности (тысячные доли секунды). При каждом импульсе тока расплавляется и переходит на изделие с плавящего электрода небольшое количество металла, что позволяет наплавлять даже острие резца; толщина наплавленного слоя составляет менее 0,1 мм.
При вибродуговой наплавке (рис. 29) можно наносить на изделие слой металла толщиной от 0,5 мм и более.
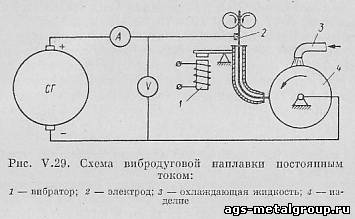
Процесс наплавки состоит из одинаковых циклов, в каждом из которых происходит замыкание электрода с наплавляемой поверхностью детали, размыкание и образование кратковременной дуги. Подача электрода к изделию до замыкания составляет 50 циклов в секунду при частоте вибрации в 50 гц. Сварочная головка производит подачу проволоки и вибрацию электрода. В зону плавления непрерывно подается вода или 4-процентный раствор соды. Вибродуговая наплавка успешно применяется для восстановления изношенных деталей небольшого размера.
§ 29. Пайка металлов и сплавов
Пайкой называют процесс соединения металлов, находящихся в твердом состоянии, путем расплавления присадочного металла- припоя, имеющего температуру плавления более низкую, чем температура плавления основного металла. Между расплавленным припоем и основным металлом происходят процессы взаимного растворения и диффузии, в результате чего получается прочное соединение деталей. Поверхность металлов, соединяемых пайкой, необходимо тщательно очистить от окислов и загрязнений; зазор между деталями должен быть небольшим, но оптимальным для каждой комбинации металл - припой. Окислы с поверхности деталей удаляют травлением в кислотах. Пайку часто производят с применением флюсов, назначение которых состоит в улучшении смачиваемости и защите припоя и основного металла от окисления. Иногда применяются самофлюсующиеся припои. Пайка производится двумя способами - твердыми и мягкими припоями. Для пайки твердыми припоями применяются латунь, медь, серебро, имеющие температуру плавления выше 500' С. Предел прочности соединений, паянных твердыми припоями, составляет до 45 кГ/мм² (450 МПа); нагрев изделий под пайку осуществляют газовым пламенем, электричеством . (сопротивлением, высокочастотным нагревом). В массовом производстве применяют пайку в печах и в соляных ваннах.
Пайка мягкими припоями осуществляется при температуре плавления их ниже 400 С. Прочность паяных соединений при этом составляет до 5 - 7 кГ/мм² (50 - 70 МПа).
Для пайки пищевой посуды и медицинской аппаратуры используют припой ПОС-90: 90% Sn; 0,1 - 0,15',4 Sb; примеси Cu, Bi, As не более 0,25%; остальное - Pb; температура начала плавления 183' С. Для пайки латуни, меди, железа применяют припой ПОС-40: 40% Sn, 1,5 - 2,0 Sb; примеси не более 0,25%, остальное - Pb.
Для пайки изделий, работающих при повышенных температурах, используют припой с содержанием 97,5% Pb, 2,5% Ag; температура начала плавления 304' С.
Для малоответственной пайки применяют припой, содержащий 13% Sn; 27% Pb; 50% Bi, 10% Cd, с температурой плавления 80' С.
Нагрев деталей при пайке мягкими припоями производят паяльниками, газовыми горелками, погружением в расплавленный припой, покрытый сверху флюсом и др. В качестве флюса используются канифоль, хорошо очищающая медь и латунь от окислов; раствор хлористого цинка - 25 - 50% и нашатыря - 5 - 20% (остальное вода); стеарин для пайки свинца и свинцовых сплавов и др.
Значительные трудности вызывает пайка алюминия вследствие образования тугоплавкой окиси алюминия Al₂O₃. После тщательной очистки и обезжиривания поверхности изделия производится пайка мягкими припоями, содержащими 60% Cd, 40% Zn или 55% Sn, 25% Zn и 20% Cd, с применением флюса, состоящего из хлористого цинка (73%) и фтористого натрия (27%). Производится также пайка алюминия без применения флюса методом ультразвуковой пайки, при которой окисные пленки разрушаются вследствие воздействия ультразвуковых высокочастотных колебаний.
При серийном производстве применяются автоматическая пайка изделий т. в. ч., контактная и ультразвуковая, обеспечивающие высокую производительность и хорошее качество соединения металлов.