НОВЫЕ МЕТОДЫ СВАРКИ
§ 30. Холодная сварка
Холодная (прессовая) сварка высокопластичных металлов (алюминия, меди, серебра, титана и др.) производится без подогрева под большим давлением, что сопровождается их пластической деформацией; при этом атомы соединяемых деталей сближаются на такое же расстояние, на котором они находились внутри металла. Холодная сварка применяется обычно для получения соединений встык и внахлестку. Удельное давление на рабочую поверхность пуансона составляет 30 - 100 кГ/мм² (300 - 1000 МПа).
При сварке листов толщиной 0,2 - 15 мм из высокопластичных металлов свариваемые поверхности должны быть тщательно очищены и обезжирены. Холодная сварка применяется главным образом для сварки листов, тонкостенных труб, оболочек, проводов и др.
Форма пуансонов подбирается в зависимости от вида соединения. При точечной сварке используют цилиндрические, прямоугольные и фасонные пуансоны. При шовной сварке применяют ролики диаметром 50δ (δ - толщина листа). Необходимое давление обеспечивается винтовыми, гидравлическими; рычажными и эксцентриковыми прессами.
На рис. З0 приведена схема холодной сварки. Пуансон 2 под действием пресса погружается в свариваемые алюминиевые детали 1 на глубину 70 - 80% толщины детали. Пуансон перемещается в стальных направляющих стаканах 3, которые своим давлением устраняют выпучивание металла. В местах соприкосновения пуансона с металлом происходит значительная деформация, и детали в плоскости АА свариваются.
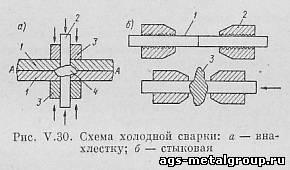
При сварке встык (рис. З0, 6) стержни 1 зажимают стальными губками 2, имеющими насечки во избежание проскальзывания стержней. При сдавливании стержней происходит сварка; образовавшийся грат 3 легко удаляется.
§ 31. Сварка трением
Сварка трением применяется для соединений встык стержней, труб, инструментальных заготовок, для приварки днищ газовых баллонов и др. После нагрева торцов деталей производят их осадку, в результате чего получают прочное неразъемное соединение. Промышленность изготовляет специальные станки для сварки трением.
Сварка трением имеет ряд следующих преимуществ перед другими способами сварки: простота и надежность процесса; возможность автоматизации; незначительное потребление мощности и энергии; надежность сварки различных металлов (бронза- сталь, медь - сталь и др.).
Для сварки трением при монтаже оборудования в случае отсутствия необходимого сварочного оборудования можно использовать токарные станки.
Производительность машины МП-1 для сварки трением составляет 150 сварок в час стальных деталей, у которых диаметр поверхности трения равен 10 - 22 мм.
§ 32. Сварка токами высокой частоты и электронным лучом
Сварка токами высокой частоты. Металл нагревают индуктированным током и затем детали сваривают с применением давления или плавления. Изделие помещают в индуктор, представляющий собой обычную катушку из медной трубки, охлаждаемой водой, с небольшим числом витков. При пропускании тока высокой частоты индуктор образует переменное магнитное поле той же частоты, которое создает вторичные индуктированные токи в изделии, помещенном в индуктор.
Сварка электронным лучом. Сущность сварки заключается в нагреве изделия бомбардировкой его поверхности пучком электронов в вакуумированном до 1 х 10⁻⁴ - 1 х 10⁻⁵ мм. рт. ст. пространстве. Электроны имитируются из катода специальной электроннолучевой пушкой и ускоряются высоким напряжением. Электрическая система собирает поток электронов в пучок. Магнитная линза окончательно формирует острый луч, и струя электронов направляется к местам сварки. В результате локализации большой мощности в небольшом объеме металл быстро расплавляется. Этот способ особенно ценен для сварки тугоплавких металлов: вольфрама, молибдена, титана и других металлов и сплавов.
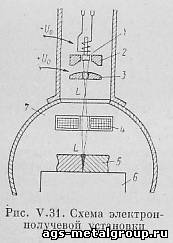
На рис. 31 приведена схема электроннолучевой установки. В вакуумированной камере 7 (вакуум ~ 10⁻⁵ мм рт. ст.) находятся следующие элементы: катод 1, фокусирующий наконечник 2 (из вольфрама или из гексаборида лантана), который вместе с анодом 3 имеет форму вогнутой линзы для создания более собранного потока электронов; анод, расположен на расстоянии 3 - 10 мм от катода; электромагнитная линза 4 и свариваемая деталь 5, закрепленная на столе 6.
Между катодом и анодом создается ускоряющее напряжение (10 000 - 30 000 в) для образования потока электронов в виде пучка, проходящего через отверстие анода и затем через электромагнитную катушку 4. Последняя превращает поток электронов в тонкий луч, образующий на детали бомбордируемое пятно размером до 1 мм².
Процесс сварки можно регулировать изменением параметров режима сварки: электронного тока, напряжения, прерывания луча и изменением скорости его перемещения по изделию. Электроннолучевые установки для сварки деталей применяются на ряде промышленных предприятий.
§ 33. Ультразвуковая сварка
Сварка осуществляется с использованием ультразвуковых колебаний металлов частотой 15 - 170 кгц и, кроме того, производится сжатие деталей с заданными усилиями. В месте сварки возникают значительные силы трения, повышающие температуру металла, что способствует пластической деформации микровыступов; происходит дробление поверхностных пленок, обеспечивающее перемещение атомов металла при значительно меньшем давлении, чем при холодной сварке. В зоне контакта при этом образуется прочное неразъемное соединение деталей.
Ультразвуковую сварку применяют для сварки внахлестку изделий из листов толщиной до 1 мм, из высокопластичных металлов (алюминия, меди, никеля, циркония, аустенитных сталей) методом точечной и роликовой сварки.
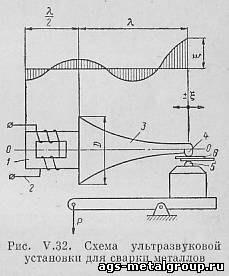
На рис. 32 приведена схема ультразвуковой установки для сварки металлов. Магнито-стрикционный вибратор 1 (преобразователь) представляет сердечник с навитой на него обмоткой, питающейся от высокочастотного генератора. К вибратору крепится (обычно пайкой) волновод 3, имеющий коническую или криволинейно-коническую форму. Наконечник 4 волновода сделан из твердой инструментальной стали. Между наконечником и опорным электродом 5 зажимается свариваемое изделие 6, находящееся под давлением рычажно-пневматической и рычажно-грузовой системы.
При подаче напряжения на катушку 2 вибратор совершает колебание вдоль оси ОО и передает их волноводу (λ - длина волны звуковых колебаний; ξ - амплитуда колебаний наконечника).
Ультразвуковая сварка обеспечивает соединение тонких листов без расплавления металла с незначительной их деформацией. Прочность такого соединения почти равна прочности основного металла.
§ 34. Диффузионная сварка металлов в вакууме
Диффузионная сварка производится в специальной вакуумной камере при разрежении 10⁻³ - 10⁻⁵ мм. рт. ст. В вакуумной камере изделие подвергается нагреву т. в. ч. (для стали 900 - 1200' С) и сжатию в местах сварки под давлением 2 - 5 кГ/мм² (20 - 50 МПа) гидроцилиндров.
Ввиду того что сварка проводится в вакууме, можно сваривать детали из однородных и разнородных металлов. Химический состав кроме диффузионной зоны сварного соединения практически не изменяется. При сварке в вакууме металл с поверхности, как правило, не покрывается окисленной пленкой, а некоторые из имеющихся на металле пленок удаляются. Соединяемые поверхности деталей перед сваркой необходимо тщательно очищать.
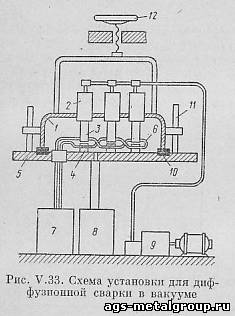
На рис. 33 приведена схема установки для диффузионной сварки в вакууме. В вакуумной камере установленные на подставке 4 детали подвергают нагреву высокочастотным индуктором 6 от лампового генератора 7 и сжатию жаростойким штоком 3 гидроцилиндров 2. Давление в гидроцилиндрах осуществляют масляным насосом 9. Для герметизации камеры кожух 1 с уплотнением из вакуумной резины 10 устанавливают на столе 5. Вакуум в камере обеспечивается системой насосов 8. Кожух поднимается вверх по направляющим 11 с помощью винта 12.
§ 35. Плазменная обработка металлов
Плазменная обработка металлов применяется для плавки, резки, сварки и наплавки тугоплавких металлов (молибдена, тантала, вольфрама, циркония и др,).
Плазма представляет собой массу хаотически движущихся оголенных ядер и оторванных от них электронов - ионизированный газ. Плазменное состояние вещества представляет источник энергии с особо высокой температурой. В лабораторных условиях под руководством акад. Л. А. Арцимовича получена температура около 40 000' С. Для практических целей такая высокая температура не требуется.
Плазменная струя получается при дуговом разряде между электродами при обжатии столба (например, продувкой газа) обычно аргона или смеси аргона с другим газом. Особенно большое значение имеет центральная струя пламени, называемая плазменным шнуром, в котором частицы движутся с огромной скоростью, увлекая за собой свежие слои ионизированного газа. Образование плазменного шнура происходит при сжатии пламени магнитным полем дуги или внешним охладителем. Степень ионизации в плазменном шнуре весьма значительная, избыточное давление очень большое, температура плазменного пламени составляет 10 - 15 тыс.'С, давление газа 2 - 3 ат, ток 400 - 500 а, скорость струи более 15 000 м/сек. Расплавление сопла не происходит из-за, нахождения шнура в теплоизолирующих кольцевых слоях малоионизированного газа и холодной тонкой пленки газа, скользящей по медным стенкам сопла, охлаждаемого водой.
Мощность плазменной струи и напряжение дуги регулируются расположением электрода в канале.
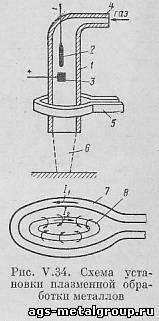
Для сварки используют различные установки (рис. 34). Электроды 2 и 3 находятся в кварцевом цилиндре 1. Между электродами образуется дуга, создающая первоначальную ионизацию газа, поступающего через отверстие 4. При поступлении ионизированного газа в плоскость высокочастотного индуктора 5 (20- 80 мггц) в поле его действия образуются непрерывные потоки кольцевых плазмоидов, представляющие собой кольцевой разряд, сжимаемый его собственным магнитным полем. При использовании высокочастотных горелок, в которых система индуктора 7 и газовое кольцо 8 становятся трансформатором (индуктор 7 является первичной обмоткой с его током и плазмоид 8 - вторичным витком с эквивалентным током I₂), создается поток высокочастотной плазмы (на рисунке не показан).
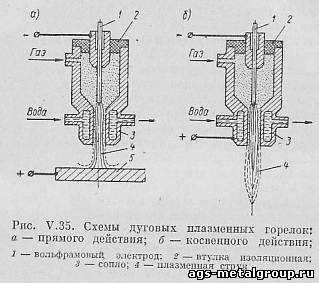
Для сварки, резки, плавки металлов успешно применяют дуговые плазменные горелки (рис. 35): прямого действия для обработки металлов и косвенного действия для обработки диэлектрических и полупроводниковых материалов.
Дуга возбуждается в среде аргона [давление 3 - 4 ат (0,3 - 0,4 МПа)] между вольфрамовым электродом (катодом) и соплом (анодом), охлаждаемым водой. Сопло имеет отверстие для выхода из камеры плазменной струи, представляющей поток ионизированных частиц газа с температурой 10 000 - 18 000' С.
§ 36. Сварка пластмасс
Термореактивные пластмассы при нагреве разрушаются (обугливаются) и сварке не подвергаются, а термопластические пластмассы (термопласты) подвергаются сварке.
Термопласты не имеют резко выраженной температуры плавления; они обладают коэффициентом теплового расширения, в 5 - 6 раз превышающим коэффициент теплового расширения металла. При высокой температуре нагрева термопласты теряют свои физические свойства и переходят из твердого состояния в пластическое и затем в вязко-текучее состояние. Процесс сварки термопластов значительно сложнее, чем сварка металлов.
Нагрев пластмасс для сварки необходимо проводить равномерно и быстро, не допуская перегрева и недогрева.
Сварные соединения пластмасс такие же, как и металлов: стыковые, угловые, тавровые, внахлестку. При стыковом соединении разделка кромок осуществляется под углом 60 - 70' С.
Применяются следующие способы сварки пластмасс.
Сварка нагретым газом. Нагрев разделки кромок деталей обычно осуществляют горячим сжатым воздухом (250 - 280' С), нагретым в специальных электрических или газовых горелках. Для устранения окисления пластмасс иногда нагрев производят горячим сжатым азотом или углекислым газом. Коробление свариваемых деталей снижается струей газа небольшого сечения 3 - 5 мм. Температуру электронагрева воздуха регулируют реостатом или индуктивным сопротивлением.
Сварка нагревательным элементом (контактным теплом). Источником нагрева служит металлический элемент, нагреваемый электрическим током, расположенным между свариваемыми деталями. После нагрева пластмассы до размягчения удаляют нагревательный элемент, а размягченные поверхности деталей сжимают и получают прочное соединение.
Сварка токами высокой частоты. Этот способ заключается в нагреве изделия в высокочастотном электрическом поле и сжатии деталей после их разогрева до пластического состояния. Производительность сварки т. в. ч. в 5 раз выше производительности других способов сварки; прочность соединения соответствует прочности основного материала.
Сварка пластмасс осуществляется также методами трения и ультразвуком аналогично сварке металлов. При ультразвуковой сварке в отличие от сварки металлов колебания производят в направлении приложения давления, перпендикулярно к свариваемой поверхности изделия.
Для сварки пластмасс т. в. ч. выпускаются специальные сварочные машины.