ОБРАБОТКА НА ФРЕЗЕРНЫХ СТАНКАХ
§ 30. Фрезерование и основные типы фрез
Фрезерование - один из высокопроизводительных и распространенных способов обработки металлов резанием.
Фреза представляет собой режущий инструмент, обладающий несколькими зубьями, причем каждый из них можно рассматривать как резец (рис. 51). При фрезеровании главное (вращательное) движение осуществляет фреза, а движение подачи - заготовка, реже фреза.
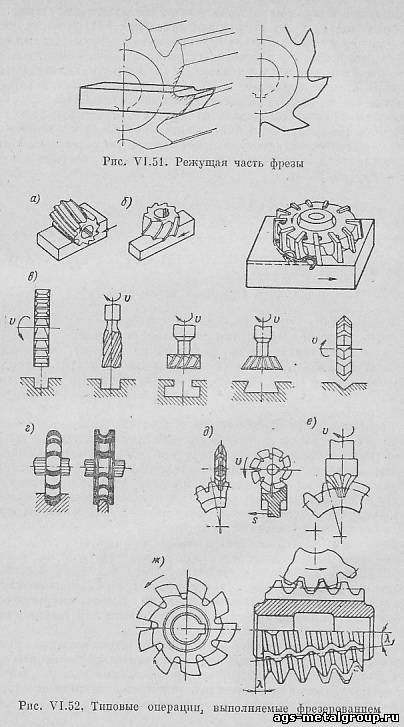
Фрезерованием производится обработка плоскостей, пазов, фасонных поверхностей, разрезка металла. Имеются фрезы для обработки тел вращения, резьб и зубьев зубчатых колес. Основные типовые операции, выполняемые фрезерованием с применением различного типа фрез, показаны на рис. 52.
По конструкции фрезы разделяются на следующие:
а) цельные, изготовляемые полностью из высококачественного инструментального материала;
б) напайные, изготовляемые из конструкционных сталей, причем на рабочие части зубьев напаиваются пластинки из высококачественных инструментальных материалов. Эти фрезы более трудоемки в изготовлении, менее прочны, но более экономичны. Напайными обычно изготовляются фрезы средних размеров, оснащенные пластинками из быстрорежущей стали или твердых сплавов;
в) наборные, состоящие из корпуса, изготовляемого из легированной конструкционной стали, и вставных быстрорежущих или твердосплавных зубьев-ножей, закрепляемых в корпусе фрезы механическими средствами (клиньями, штифтами и т. д,). Наборными изготовляются крупные фрезы.
По назначению фрезы разделяются на следующие типы: цилиндрические (рис. 52, а) и торцевые (рис. 52, б) для обработки плоскостей; дисковые, концевые, пазовые и угловые (рис 52, в) для обработки канавок и пазов; фасонные для обработки фасонных поверхностей (рис. 52, г); модульные дисковые (рис. 52, д) и пальцевые (рис. 52, е) для обработки зубьев зубчатых колес.
На специальных фрезерных (зуборезных) станках используют червячные фрезы (рис. 52, ж), а на специальных резьбофрезерных - резьбовые.
§ 31. Элементы фрез
Фреза состоит из корпуса (тела) и режущих зубьев. Каждый режущий зуб фрезы имеет такие же элементы и углы, как и резец. Геометрические элементы режущей части фрезы показаны на рис. 53, а.
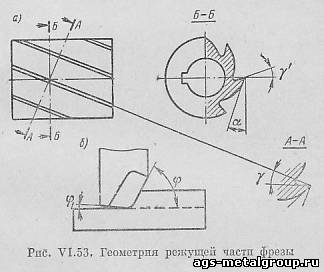
Главный передний угол γ рассматривается в плоскости, нормальной к главной режущей кромке и проходящей через данную точку (сечение А - А). Иногда передний угол задается в плоскости, нормальной к оси фрезы, γ'. Для фрез из быстрорежущей стали передний угол принимается в пределах 10 - 20˚. Главный задний угол α рассматривается в плоскости, нормальной к оси фрезы (сечение Б - Б). Иногда задний угол задается в нормальном сечении к главной режущей кромке αn. Для фрез из быстрорежущих сталей αn колеблется в пределах 10 - 30˚.
Торцевые фрезы характеризуются также углами в плане (рис. 53, б) и углом наклона главной режущей кромки. Главный угол в плане φ чаще всего равен 60˚. Вспомогательный угол в плане φ₁ для торцевых фрез составляет 2 - 10˚. Угол наклона главной режущей кромки у торцевых твердосплавных фрез λ = 0 ÷ + 15˚.
Затачивание фрез производится по передней или задней поверхности. Фрезы, затачиваемые по задней поверхности (рис. 54, а), имеют плоскую (прямозубые фрезы) или цилиндрическую (винтовые фрезы) заднюю поверхность и называются фрезами с остроконечным зубом. Эти фрезы просты в изготовлении и легко перетачиваются. Кроме того, по мере перетачивания прочность зуба увеличивается.
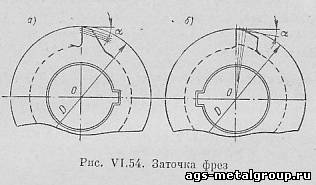
У фрез, затачиваемых по передней поверхности (рис. 54, б), задняя поверхность выполнена по архимедовой спирали, что позволяет сохранять профиль зуба при его перетачивании. Однако прочность зубьев при этом снижается. Такие фрезы называются фрезами с затылованным зубом.
Фасонные, модульные и резьбовые фрезы делаются обычно с затылованными зубьями, остальные - с остроконечными.
§ 32. Элементы резания
При фрезеровании, так же как и при других видах обработки, режимы резания характеризуются скоростью резания, величиной подачи и глубиной резания, а кроме того, шириной фрезерования В (рис. 55).
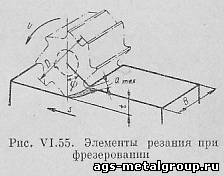
Скоростью резания υ при фрезеровании называется окружная скорость наиболее удаленных точек режущих зубьев фрезы. Она может быть вычислена по формуле:

где D - наружный диаметр фрезы в мм; n - число оборотов фрезы в минуту.
Экспериментальные исследования показывают, что в общем случае скорость резания, допускаемая режущими свойствами фрезы, может быть подсчитана по следующей формуле:
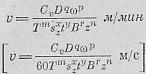
где Cυ - коэффициент, характеризующий механические свойства металла; D - диаметр фрезы в мм; Т - стойкость фрезы в мин; Sz - подача на один зуб фрезы в мм/зуб; t - глубина резания в мм; В - ширина фрезерования в мм; z - число зубьев фрезы; ω - угол наклона винтовой канавки фрезы; r, n, q, p, m, x, y - показатели степеней (выбираются в зависимости от типа фрезы).
Значения коэффициента Cυ и показателей степеней принимаются по соответствующим справочникам.
Слой металла, снимаемый за один проход фрезы, называется глубиной резания t. Она измеряется в мм (рис. 55).
Величина перемещения детали относительно оси фрезы называется подачей S.
При фрезеровании различают три значения подач: подача на зуб Sz - величина перемещения заготовки относительно фрезы за время ее поворота на один зуб (в мм/зуб); подача на оборот So - величина перемещения заготовки относительно фрезы за один ее оборот (в мм/об); минутная подача Sm - скорость перемещения заготовки относительно фрезы (в мм/мин).
Подачи при фрезеровании связаны между собой следующей зависимостью; Sm = Son = SzZ · n мм/мин, где z - число зубьев фрезы; n - число оборотов фрезы в минуту.
Толщина стружки при фрезеровании - величина переменная. Каждый зуб фрезы выполняет работу только во время незначительной части оборота; большую часть оборота он проходит не участвуя в процессе резания. При этом зуб охлаждается, что положительно влияет на его стойкость. Для продолжения стружкообразования зуб должен вновь врезаться в срезаемый слой.
Если направления вращения фрезы и перемещения заготовки не совпадают (рис. 56, а), нагрузка на зуб увеличивается постепенно, так как толщина среза изменяется от нуля при входе зуба в обрабатываемый металл до максимума при выходе зуба из металла. Такой метод фрезерования называется встречным фрезерованием. Зуб работает из-под корки, надламывает и выбрасывает ее из зоны резания, что очень важно при обработке деталей, имеющих литейную корку или окалину. Недостаток встречного фрезерования состоит в том, что усилие резания р, направленное вверх, стремится оторвать деталь от стола, что при больших сечениях среза приводит к вибрации и ухудшению чистоты поверхности.
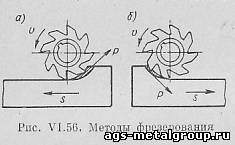
Если направления вращения фрезы и перемещения заготовки совпадают (рис. 56, б), зуб сразу подвергается максимальной нагрузке. Усилие резания Р прижимает заготовку к столу. Большая загрязненность и твердость корки приводят в этом случае к резкому снижению стойкости фрезы. Но при отсутствии корки, как показала практика, этот способ фрезерования, называемый попутным, обеспечивает большую стойкость фрезы, лучшую чистоту обработанной поверхности и меньший расход мощности. Однако попутное фрезерование возможно только на тех станках, которые имеют специальные устройства для устранения зазора в паре винт - гайка.
Максимальная толщина стружки (толщина среза) αmах в обоих случаях равна αmах = Sz sinψ, где ψ - угол контакта фрезы с деталью (рис. 55).
Площадью сечения стружки Fmax называется произведение ширины фрезерования на максимальную толщину стружки Fmax = Bαmax = BSz sinψ
§ 33. Силы резания и мощность
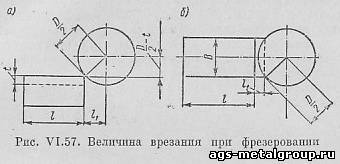
Основное время при фрезеровании (рис. 57) определяется по формуле:
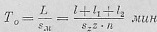
где Ь - общая длина прохода фрезы в направлении подачи в мм; l - длина фрезеруемой поверхности в мм; l₁ - путь врезания фрезы в мм; l₂ - перебег фрезы в мм; Sm - минутная подача в мм/мин; Sz - подача на один зуб в мм; z - число зубьев фрезы; n - число оборотов фрезы в минуту.
Величина врезания при фрезеровании цилиндрической фрезой (рис. 57, a) определяется по формуле l₁ = √t(D-t), где t - глубина резания в мм; D - диаметр фрезы в мм.
Величина врезания при симметричном фрезеровании торцевой фрезой (рис. 57, б) определяется по формуле l₁ = 0,5(D-√D²-В²), где В - ширина фрезеруемой поверхности.
Величина перебега l₂ берется от 1 до 5 мм в зависимости от диаметра фрезы.
В процессе фрезерования на каждый зуб фрезы действуют силы резания, направление и величина которых различны в зависимости от характера фрезерования и направления подачи. Для прямозубой цилиндрической фрезы суммарную равнодействующую силу сопротивления срезаемого слоя R можно разложить на касательную или окружную Pz и радиальную Py или горизонтальную Ph и вертикальную Pυ (рис. 58) составляющие.
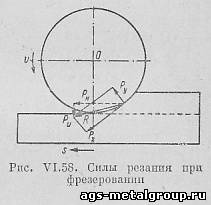
При фрезеровании фрезой с винтовым зубом образуется еще осевая составляющая, направление которой зависит от направления спирали фрезы.
Окружная сила резания Pz определяется по формуле:

где Cp - коэффициент, характеризующий материал и условия обработки; t - глубина фрезерования в мм; Sz - подача на один зуб фрезы в мм; В - ширина фрезерования в мм; z - число зубьев фрезы; D - диаметр фрезы в мм.
По тангенциальному усилию Pz определяют крутящий момент на шпинделе станка:

где D - диаметр фрезы в мм.
По крутящему моменту можно определить мощность, расходуемую на резание, и произвести расчет шпинделя и фрезерной оправки на прочность.